March 2013
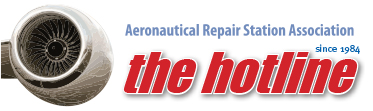
News
Sarah says: Welcome to ARSA’s new blog
By Sarah MacLeod, ARSA executive director
So, ARSA is blogging – for anyone that doubts the association is by and for the membership; this is one more example of how open it is to commentary from all directions. Blogs can be cumbersome and time consuming – we pledge this one will deliver knowledgeable exchanges with honest messaging. Indeed, the association will ensure the content remains relevant, so, yes, we will remove content that does not further the education, knowledge, skills or policy of the aviation maintenance industry.
To start the discussion, I welcome feedback on topics that need knowledge to resolve. For example, most aviation businesses hold certificates issued by civil aviation authorities of various governments yet do not have a regulatory compliance office similar to those organized for Occupational Safety and Health Administrations or Environmental Protection Agency or even tax regulations. Rather than ensuring the entire company mitigates non-compliant risk uniformly, enterprises with multiple locations in various countries allow the local management “satisfy” the agencies’ requests. Maybe this is one of the reasons local inspector preference can cost small, medium and large companies so much money from “non-standardization.”
ARSA concludes successful 2013 Annual Repair Symposium
From March 20-22, ARSA held its 2013 Annual Repair Symposium, highlighting the association’s legislative and regulatory successes this year and providing members with up-to-date information critical to maintaining their certifications.
The Annual Repair Symposium began Wednesday with a successful Legislative Day on Capitol Hill, where members spoke with their lawmakers about the economic importance of the MRO industry, the impact the foreign repair station certification ban is having on the growth of their businesses, and the need to provide the FAA with the resources required to carry out its mission.
On Thursday, panelists provided association members with updates on the regulations governing the maintenance industry, the design and production of civil aviation articles, and pressing issues facing aviation maintenance customers.
Members also heard from ARSA President Gary Fortner, who expressed confidence in the group’s continued efforts to aggressively address key issues before regulatory, legislative, and business leaders. Fortner also highlighted ARSA’s efforts, through the Positive Publicity Campaign, to promote the safety and economic achievements of the maintenance industry.
The Symposium ended on a high note, as Federal Aviation Administration (FAA) Administrator Michael Huerta spoke about the important role ARSA plays with the FAA and credited the association’s executive director, Sarah MacLeod, for her leadership. He also praised the maintenance community for its contribution to ensuring the safety of our aviation system.
Be sure to attend next year’s Annual Repair Symposium held March 19-21, 2014 to receive critical regulatory updates and hear from industry leaders on important issues facing aviation maintenance.
President’s message
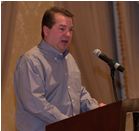
Editor’s Note: ARSA President Gary Fortner provided ARSA members with an overview of the association’s recent activities and goals in remarks delivered at the 2013 Annual Repair Symposium’s Membership Meeting and Breakfast. The following is the text of Mr. Fortner’s prepared remarks.
Good morning, my name is Gary Fortner, the president of ARSA. It is an honor, on behalf of the board of directors, to call to order the Annual Membership Meeting and State of the Association.
First, please allow me to introduce our directors. The association prides itself on ensuring each segment of our multi-faceted industry is represented on the association’s board. I’d ask that each board member stand as I call their name and explain their role.
Gary Jordan of Jordan Propeller Service serves as the association’s vice president and ensures we understand the issues impacting propeller maintenance.
Jim Perdue of SONICO serves as ARSA treasurer. Jim and I make sure component maintainers’ interests are known, since those businesses make up the vast majority of ARSA’s membership.
Ian Cheyne of BBA’s Dallas Airmotive represents engine maintenance providers.
Gary Hudnall of Jet Center Medford covers the interests of general aviation.
Dave Latimer, from TIMCO, represents companies that work on large aircraft.
Immediate past ARSA President Hanno Loss of Lufthansa Technik represents the association’s international members.
And, while not able to be with us this week, Basil Barimo of the NORDAM Repair Group ensures various corporate, business and airline maintenance issues are addressed and Chris Erickson from Erickson AirCrane represents the helicopter industry.
This past year was a big one for the association.
ARSA’s legislative program continues to grow and increase the industry’s visibility on Capitol Hill. The past two days you have heard about ARSA’s top legislative priorities and the successes we’ve had this past year. Those successes would not have been possible without collective action. Engagement and participation are the cornerstone of any successful legislative program, and ARSA had plenty of it this past year.
For starters, numerous member companies invited congressional leaders and staff to their facilities. Last month, Barfield, Inc., hosted Rep. Mario Diaz-Balart (R-Fla.) at its Miami location. In June, Component Repair Technologies in Ohio hosted a staffer from Sen. Rob Portman’s (R-Ohio) office and in August, my company, Fortner Engineering, welcomed Rep. Adam Schiff (D-Calif.).
Let me just say that Rep. Schiff has never been a supporter of repair stations. In fact, he has voted against our positions numerous times. As personal testimony to the impact facility visits can have, especially with our opponents, Rep. Schiff later sent a letter to TSA Administrator Pistole about the impact the foreign repair station certification ban is having on our industry.
Because of his visit to my facility, Rep. Schiff has a better understanding of our industry and our issues. Facility visits are the best way to educate lawmakers, and the summer break is a great time to do it. If you haven’t already done so, bombard Daniel and Josh right after breakfast and ask them to help organize a facility visit at your location. Not only will you build a relationship with local leadership, you’ll get the chance to have a real impact in the legislative process moving forward.
This past year also marked the resurgence of ARSA PAC. The “Part 145 Club” was launched to encourage broader participation and it certainly worked. More than 100 members gave solicitation consent and a record 42 gave a collective $10,035, allowing ARSA PAC to contribute $5,000 to congressional campaigns.
Additionally, members sent nearly 100 letters to Congress through ARSA’s grassroots website ARSAaction.org, and yesterday, 41 of you stormed Capitol Hill to hold meetings with lawmakers.
To wrap up my comments on ARSA’s legislative program, last April, I was able to get a first-hand look at Congress in action when I testified at a House Aviation Subcommittee hearing about the excellent work repair stations within the United States and around the world are doing to ensure aviation safety. The hearing was an eye-opening experience and it reaffirmed why legislative advocacy must be an integral part of ARSA’s activities. It also reaffirmed how important it is for people like me and you to participate in the process. My involvement in this organization and my local community gave me the opportunity to promote my industry in front of those making policy decisions that directly impact my business. If we all choose to act when given the opportunity, ARSA’s legislative team will continue to make great strides on our behalf.
As you heard in yesterday’s regulatory update session, ARSA continues to make frequent contact with aviation authorities on a range of issues.
ARSA continues to find strength in numbers by working with industry partners to ensure agency policy strikes the right balance between regulatory requirements and business obligations. For example, ARSA re-wrote advisory circular 145-11, guidance for repair station compliance with the U.S./EU safety agreement, and last April, ARSA joined the Aerospace Industries Association and the General Aviation Manufacturers Association to request assistance in resolving MAG tagging requirements.
Through its correspondence with EASA and other aviation authorities, ARSA is expanding its international footprint. In December, executive staff traveled to Montreal for meetings with the International Air Transport Association to discuss regulatory and legislative advocacy cooperation. ARSA has also asked to participate on the EASA safety standards consultative committee to ensure that repair facilities have a seat at the table when rulemaking activities are discussed.
Here in the U.S., ARSA continues to fight the good fight with regulators and business leaders alike.
Ensuring maintenance instruction availability is still a top priority for the association. This year, ARSA asked the Supreme Court to intervene. While the writ ARSA filed in support of ICA availability was subsequently denied, the association was able to assert on a very public stage that when a federal agency isn’t following its own regulations, the federal courts must ensure that the public has redress.
More concrete headway was made when the FAA responded to a three-year-old request for legal interpretation. The agency confirmed that all CMMs referenced in an ALS are part of the ICA and that modifications to the ALS are changes in type design that trigger requirements that the CMM be made available. The agency further confirmed that design approval holders must make the ALS and referenced CMMs available to a properly rated repair station in possession of a component to be worked on, a contract, or work order.
In the ICA workshop breakout immediately following breakfast, Marshall will be talking about this document and other tools that certificate holders may use in their quest for maintenance instructions.
In a major victory for the aviation industry, in December, the FAA withdrew its faulty legal interpretation of maintenance duty time limitations, which had erroneously concluded that the rule rigidly required one day off out of every seven days. It was ARSA’s complaint, noting that the agency’s interpretation overlooked the plain language of the rule, which prompted the FAA’s reevaluation. While the rule required air carriers, and their maintenance providers, to rewrite schedules at significant cost in order to accommodate a wrongheaded bureaucratic action, the subsequent victory clearly shows the value of actively engaging with government when it strays from its regulatory perimeters.
To that same end, ARSA recently engaged in two FAA rulemakings that would directly impact repair stations with FAA certification.
Last spring, the FAA released a notice of proposed rulemaking for 14 CFR part 145. ARSA spent abundant resources to ensure its response comprehensively addressed the concerns and interests of all repair stations. While the proposal means to align regulations, current business models, and future safety management system requirements, the association pointed out several instances where the proposed rule deviates from that original purpose. For example, the rule does not include a line maintenance rating, which would put FAA ratings in line with Canadian and European systems, and it seeks to separate the operations specifications from the certificate, which would unnecessarily burden FAA inspectors and industry.
In its latest quest for justice, ARSA submitted comments to the FAA’s air carrier contract maintenance requirements proposed rule. The proposed rule is the direct result of Section 319 if the FAA Modernization & Reform Act of 2012, the latest FAA reauthorization bill. The association stressed that the agency’s NPRM goes beyond the legislative mandate and misconstrues the plain language of the legislation resulting in a confusing proposal that duplicates existing rules. ARSA’s comments include suggested regulatory language that recognizes existing rules, narrowly targets the mandated provisions to avoid confusion, and preserves operational realities for air carriers and repair stations.
ARSA members also have a role to play in ensuring ARSA’s regulatory program is successful. Contact ARSA and let us know how a rule will affect your business, and submit comments to agency rulemakings. Industry input is a vital part of the rulemaking process and one that we should all take advantage of when given the opportunity.
Outside the legislative and regulatory arenas, ARSA continues to improve its membership outreach and programs.
This past fall, ARSA.org received a much needed overhaul. And it’s not just a pretty face. This coming year it will be loaded with additional functionality, such as a members-only section allowing for enhanced member benefits, and increased efficiencies through online payment processing and automatic membership renewals.
Thanks to the continued support of ARSA’s positive publicity campaign, or PPC, and the hard work of the PR committee, updated industry economic data will be officially released in the next few weeks. The data has become a critical piece in helping congressional leaders understand how harmful regulations and legislation affect jobs and the economy. I can say that it’s incredibly helpful when I can visit my congressman’s office and tell him or her the exact economic impact my industry has in his or her state. Right now, congressional leaders are all about the numbers, and, thanks to member monetary support, the PPC has given us the resources to make our voices louder on Capitol Hill.
In conclusion, allow me to thank you for your attendance and reiterate the importance of getting involved in your association. While I am grateful for the opportunity to do my part, the association gives much in return. Through my participation on the board of directors, giving to the political action committee and the PPC, attending Legislative Day and thereafter engaging my lawmakers at home, I have been able to not only raise my company’s profile, but help to ensure that the industry’s voice is heard by key audiences.
As ARSA’s President, I pledge to ensure the association continues to push the envelope. I thank the ARSA staff for their continual hard work on our behalf. It is truly a special organization, one dedicated to the progress of our industry, and I am proud to play such a key role. With that, I look forward to seeing everyone at next year’s Symposium, scheduled for March 19-21, 2014 here at the Ritz Carlton.
I hereby adjourn the 2013 annual membership meeting.
Legal briefs
The air carrier and repair station regulatory relationship: Part 3
By Craig Fabian, ARSA vice president of regulatory affairs & assistant general counsel
Previous installments of this series discussed the air carrier and repair station relationship in the United States generally, as well as the maintenance regulations forming the foundation for interface between these parties. Specifically, we explored the maintenance performance rules in Title 14 Code of Federal Regulations (14 CFR) section 43.13, which delineates what information is used to perform work (§ 43.13(a)), how that work must be performed (43.13(b)), and also provides that an air carrier maintenance manual is normally an acceptable means of complying with those requirements (§ 43.13(c)). We noted how that rule couples with a repair station’s obligation in § 145.205(a) to follow the “applicable sections” of an air carrier’s maintenance manual. For repair stations, the end result of these clear regulatory connections is that it must follow the “how to” instructions contained in an air carrier’s maintenance manual.
The issue, however, does not end with that conclusion. The reason is that § 145.205(a) also requires a repair station to follow an air carrier’s maintenance program. Unlike the regulatory clarity for a repair station to follow applicable sections of an air carrier’s maintenance manual, the “program” requirement is blurred. That is, the applicable rules must be carefully deciphered to give proper meaning to the regulatory text. Unfortunately, instead of providing such close analysis, Federal Aviation Administration (FAA) guidance on the topic contains significant misconceptions which seriously impact the air carrier and repair station relationship. Indeed, the agency suggests that an air carrier’s maintenance manual is an element of the carrier’s maintenance program, which entirely swallows distinctions within the rules.
Therefore, in tackling the subject of air carrier maintenance programs we must first visit the regulations containing an air carrier’s manual requirements. This is an important step in establishing the regulatory structure and unwinding the jumbled guidance which has glossed over the differences between “manual” and “program.” In doing so, our focus is drawn to the requirements in part 121 instead of part 135, since it appears the detailed provisions of that part, along with the historical nature of such carriers to perform maintenance without significant reliance on repair station contractors, may have led to the present confusion. Today, with repair stations performing the vast majority of maintenance for part 121 air carriers, the existing regulatory framework must be recognized.
In particular, the part 121 rules state that a carrier can prepare the part of its air carrier manual containing maintenance information and instructions in printed form or other forms acceptable to the Administrator (§ 121.133). Similarly, the distribution and availability requirements for an air carrier’s manual refers to format for “the maintenance part of the manual” (§ 121.137(c)). Directly in-line with these provisions is the general manual content requirement for “instructions and procedures for maintenance, preventive maintenance, and servicing,” (§ 121.135(b)(17)) which coincides with “the methods, techniques, and practices contained in the maintenance manual or the maintenance part of the manual of the holder of an air carrier operating certificate” in § 43.13(c). These “how to” instructions are the “applicable sections” of the air carrier’s maintenance manual a repair station must follow under § 145.205(a).
Separately, the general air carrier manual provision requires the inclusion of time limitations, or standards for determining time limitations, for overhauls, inspections, and checks of airframes, engines, propellers, appliances, and emergency equipment (§ 121.135(b)(18)) and airworthiness inspections, including instructions covering procedures, standards, responsibilities, and authority of inspection personnel (§ 121.135(b)(20). A repair station must also account for these “program” items when performing maintenance under § 145.205(a). However, as we will explore further next month, it reinforces that an air carrier’s maintenance program and maintenance manual are not one in the same.
ARSA on the Hill
By Daniel Fisher, ARSA vice president of legislative affairs
In March, ARSA’s legislative team was focused on preparing for and executing a successful Legislative Day (see related article on Legislative Day).
The association continued to educate new and returning lawmakers about the industry’s legislative priorities, including TSA’s failure to finalize repair station security regulations and the need for Congress to permit certification of new foreign repair stations.
ARSA participated in a roundtable discussion with House Aviation Subcommittee Chairman Frank LoBiondo (R-N.J.) about issues important to the aviation maintenance and manufacturing sectors. Members of ARSA’s legislative team also attended the Aero Club of Washington luncheon to hear new Transportation & Infrastructure Committee Chairman Bill Shuster (R-Pa.) discuss the aviation issues at the top of the committee’s agenda.
Regulatory lookout
NTSB recommends safety improvements for maintenance
On March 12, the National Safety Transportation Board (NTSB) released five safety alerts that address common aviation accidents and offer steps that can be taken to lessen their likelihood.
“Mechanics: Manage Risks to Ensure Safety,” the only maintenance-related alert, provides recommendations for aviation technicians to ensure aircraft are safe to fly after being serviced.
Bringing a common sense approach to improving safety, the NTSB called attention to the dangerous impact of human fatigue and suggested taking the necessary steps to ensure technicians are not overworked. The Board also highlighted the need to carefully follow manufacturers’ instructions to safeguard against improperly completed maintenance. In addition, the NTSB suggested that someone other than the mechanic performing work inspect the aircraft afterward.
NTSB developed the recommendations to inform the broader aviation community of simple ways to reduce risk and limit the potential for tragic accidents.
Quality time
Editor’s note: The views and opinions expressed by contributing authors do not necessarily state or reflect those of ARSA, and shall not be used for endorsement purposes.
Legal waypoints: Prime / subcontractor relationships: The “flow down” factor
By Steven E. Pazar, attorney at Law, 11 Carriage House Lane, Boxford, Massachusetts 01921. © 2013 Steven E. Pazar ALL RIGHTS RESERVED.
Steven is an experienced counselor to businesses operating in many industries, including aviation. He provides templates, tools, and training to improve contracting efficiency, close deals faster, and control costs.
The “flow down” provision is a common tool used by a prime contractor to simplify the preparation of a subcontract agreement. Rather than repeat and revise the provisions of its prime contract in the actual subcontract document, the prime uses a flow down clause to protect itself from a drafting gap between the two documents. A simple flow down provision in a subcontract agreement may read as follows:
“The Subcontractor agrees to be bound to the Contractor by the terms of the prime contract and to assume to the Contractor all the obligations and responsibilities that the Contractor by those documents assumes to the Owner, except to the extent that the provisions contained therein are by the terms or by law applicable only to the Contractor.”
While generally protective of the prime contractor, this provision is often viewed by subcontractors as “standard” language. By creating an out of sight, out of mind dynamic, the flow down is susceptible to being discounted by subcontractors as they review proposed subcontract documents. Asking for a copy of the prime contract (even with key commercial terms redacted) only creates more review work for contracts administrators and lawyers. Once in-hand, the prime contract must be reviewed in detail with an eye to substituting the subcontractor for the prime contractor (and the prime contractor for the owner), as those terms appear in the document. The proposed flow down terms must be read in concert with the proposed subcontract so that areas of inconsistency, redundancy, and ambiguity can be resolved in the final subcontract agreement.
Needless to say, this can be a complicated process. It requires an attention to detail and patience that many subcontractors do not feel they have the negotiating strength to employ. The flow down dynamic, by its nature, creates an environment for disagreement regarding the interpretation and application of not just one set of terms, but two: the prime contract terms and the subcontract terms. If not handled with care, resolving flow down issues can derail the focus on other important commercial terms. Likewise, ignoring the presence of the flow down as a means to avoid complications can have a significant downside for the subcontractor if issues or disputes arise down the road.
Flow Down Do’s and Don’ts:
- Do request a copy of the prime contract (OK if key commercial terms are redacted).
- Do assess whether the flow down applies only to the scope of work (or particular specifications) or is more general in nature.
- Do consider limiting the application of the flow down to a specific list of provisions to suit your needs.
- Do consider drafting the flow down so that it applies in a reciprocal manner.
- Don’t agree to a flow down provision before the prime contract is finalized and available for review.
- Don’t convince yourself that the protections the prime has negotiated for itself in the prime contract will necessarily be of benefit to you as a subcontractor.
Note: The sample provision above is for illustration purposes only and is not intended for use without appropriate review in your jurisdiction.
Employment law & repair stations: Attention employees: read, review, and understand your employee handbook
By Jonathan W. Yarbrough, Constangy, Brooks & Smith, LLC, 80 Peachtree Rd., Ste. 208, Asheville, NC 28803-3160. © 2013 Jonathan W. Yarbrough ALL RIGHTS RESERVED
Jonathan is experienced representing employers in employment law issues; his pragmatic approach helps keep relationships with employees from becoming difficult. Please contact him for questions regarding employment relationships.
Employers understand the need for employee handbooks. Not only does it make sense to let your employees know what the employer expects of them, but it is also the employer’s best defense against discrimination, wage, and hour lawsuits, as well as unemployment claims. However, recent cases have demonstrated that it is not sufficient to simply provide an employee handbook and require employees to acknowledge that they have received and read it.
Here is some advice for employers that will help ensure employees understand the employer’s policies:
1. As laws affecting the employment relationship continually change and evolve, the importance of regularly reviewing and updating the handbook is critical. Here are some recent changes that employers should be aware of:
- As of March 2013, employers with 50 or more employees should have updated their Military Family and Medical Leave Act (FMLA) policies.
- Any employer may, but is not required to, include a provision allowing for exigency extended leave. Because the Equal Employment Opportunity Commission has now taken the position that attendance at work is not necessarily an essential function of the job under the Americans with Disabilities Amendments Act (ADAA), consider notifying employees that exigency extended leave may be granted if it can be reasonably accommodated. At the very least, the provision provides evidence that the employer is aware of this requirement.
- Even if you have a carefully worded social media policy, consider including a statement that nothing in the policy is intended to prohibit an employee’s exercise of rights under Section 7 of the National Labor Relations Act. This is the “concerted activity” provision that has become a source of many unfortunate lawsuits where employees have received retaliation for posting critical comments about their employer on the internet.
- Again, in the age of technology, employee handbooks routinely include provisions notifying an employee that the employer has the right to access electronic information on any company-owned electronic device, including computers, email accounts, and networks – all aspects of storage and transmission. Employers should make it abundantly clear that an employee’s expectation of privacy does not extend to the workplace. Not only does this provision protect intellectual property and trade secrets, but it also ensures data security and unauthorized use of company equipment for personal communications.
2. Here are five tips for insuring that employees read, review, and understand the policies.
- Make sure that the policies are written in clear and understandable language – consider using a larger font size for the handbook – and that they are comprehensive without being repetitive or wordy.
- Consider regular meetings to review and discuss various aspects of the handbook, particularly harassment, drug testing, social media, and privacy policies, as well as absentee and general standards of behavior policies. One possibility, particularly in connection with privacy policies that are triggered every time an employee accesses or creates information on company owned machines or networks, is to consider adding a pop-up privacy statement reminding employees that they should have no expectation of privacy associated with their use of company equipment. Pop-ups can be also be used as a daily or weekly reminder on any particular policy.
- Make sure that policies are consistently and fairly enforced. If an employer has policies that are ignored or rarely enforced, they may be subject to allegations of discrimination, or may even be held unenforceable.
- Any investigation into policy violations, particularly those that involve intrusion into what employees may consider a privacy right, should be done only with a legitimate business reason such as the need to protect sensitive information or to prevent harassment, threats of violence, or suspected drug use. Incidentally, random drug testing must only be done if the employer has a legitimate and articulatable reason for conducting the test.
- Be aware of the federal, state, and common laws when drafting and enforcing policies. Of particular concern with respect to privacy policies is the federal Electronic Communications Privacy Act (ECPA). This act prohibits the intentional interception of any wire or electronic communication or intentional disclosure or use of the information. ECPA does include a business-extension exception which allows an employer to monitor employees’ electronic communications in the ordinary course of business or if employees consent to having their electronic communications intercepted. Employers should also be aware that the Stored Communications Act (SCA) prohibits unauthorized access to stored electronic communications. Employers violate the SCA if they intentionally access stored electronic communications or exceed the authorization given.
Membership
Member spotlight
On April 2, the Greensboro City Council announced it will offer $400,000 to incentivize TIMCO Aviation Services to expand at the Piedmont Triad International Airport. TIMCO is looking into six possible locations and is still seeking $4 million from North Carolina. The company plans to announce their decision by the end of April.
TIMCO plans to invest $32 million into the expansion project, which includes building the $30 million hangar facility and hiring 400 employees over three years.
Founded in 1990, TIMCO Aviation Services is one of the largest independent providers of airframe MRO services around the globe. Originally performing airframe and base maintenance, the company’s work now also includes engine MRO services, aircraft seat manufacturing and parts, comprehensive engineering design and interiors manufacturing, and line maintenance services.
For more information, visit http://www.timco.aero/index.html
Are you an ARSA member who would like to be in the “Member Spotlight?” If so, please contact Jess Hammett at Jess.Hammett@arsa.org.
Have you seen this person?
Each month, the hotline spotlights key regulatory, legislative, and business leaders making important contributions to the aviation industry. This month we look at Jim Perdue, vice president and sales manager of Sonico, Inc.
Jim Perdue is vice president of Sonico, Inc., Moses Lake, Wash. and is on the company’s board of directors. Jim began full time employment with Sonico in 1989 after graduating from the University of Washington with a degree in business and graduate studies at Embry Riddle University in Florida. He has served Sonico in various capacities in preparation to one day become CEO.Jim is active in community service organizations, including the Rotary Club and the Moses Lake Chamber of Commerce. He also serves on ARSA’s board of directors as treasurer.To learn more about Jim Perdue please click here.
A member asked…
Q: We are planning on performing repairs to components that are only installed on military aircraft. What are the FAA requirements for a repair station doing this work?
A: The FAA issued guidance on this topic in Order 8900.1, volume 6, chapter 9, section 14, which notes that a repair station performing maintenance for the military is not using the privileges of its certificate. It also recognizes the root of confusion over this issue in stating that: “Title 14 CFR [Code of Federal Regulations] does not regulate U.S. military aircraft maintenance; however, the U.S. military strives to maintain the highest level of safety and often requires a contracting repair facility to have a part 145 certificate.”
Industry news
Maintenance competition recognizes success
From March 13-15, AMTSociety held its Sixth Annual Maintenance Skills Competition (MSC) to test the abilities of aviation maintenance professionals and students.
The MSC brought together 23 different teams from around the world competing in five event categories: military, commercial aviation, general aviation, school, and MRO/OEM. The 14 events ranged from basic safety wiring and turbine engine troubleshooting, to electrical/avionic troubleshooting.
Apart from various prizes given for each category, the event featured the William F. “Bill” O’Brien Award for Excellence in Aircraft Maintenance, awarded to FedEx Team LAX as the group with the best overall score. MSC also presented the Charles E. Taylor Professional AMT Award to U.S. Coast Guardsman AET 2 Michael Bosch for being the most professional, team-spirited competitor in attendance.
Held annually, the event promotes a positive image of the aviation maintenance industry by demonstrating the professionalism and technical expertise of maintenance personnel from around the world.
International news
India to create new aviation authority
India recently began ramping up efforts to replace its Directorate General for Civil Aviation (DGCA) with a stronger regulatory body, fleshing out the new agency’s responsibilities to oversee the aviation industry.
The Indian Civil Aviation Authority (CAA) would monitor safety issues and take steps to modernize airports and air traffic management services. The agency would be autonomous and have complete financial and regulatory oversight of the aviation industry.
Specifically, CAA would have the authority to request information, conduct investigations, and punish individuals, companies, and government departments for failing to comply with issued regulations.
Given the aviation industry’s rapid expansion in recent years and DGCA’s inability to keep up, Indian lawmakers are expected to introduce legislation creating CAA sometime this session of parliament.
Welcome new members
● Alpha Aircraft Services of America, New Braunfels, Texas
● Aviation Technical Services, Everett, Wash.
● Chloe Ann Alexander, New Port Richey, Fla.
● PAS MRO, Inc., Irvine, Calif.
● TSA Rewinds Florida Inc. dba Aircraft Armature Inc., Opa Locka, Fla.
● Windsor Airmotive – West Chester A Division of Barnes Aerospace, West Chester, Ohio
Regulatory compliance training
Click here to test your knowledge on §145.1 Applicability, the part that describes how to obtain a repair station certificate.
Previous 12 issues:
2013: | Jan | Feb | ||||||||
2012: | Mar | Apr | May | Jun | Jul | Aug | Sep | Oct | Nov | Dec |
the hotline is the monthly publication of the Aeronautical Repair Station Association (ARSA), the not-for-profit international trade association for certificated repair stations. It is for the exclusive use of ARSA members and federal employees on the ARSA mailing listFor a membership application, please call 703 739 9543 or visit www.arsa.org.
This material is provided for educational and informational purposes only. It does not constitute legal, consulting, tax or any other type of professional advice.
Law, regulations, guidance and government policies change frequently. While ARSA updates this material, we do not guarantee its accuracy. In addition, the application of this material to a particular situation is always dependent on the facts and circumstances involved. The use of this material is therefore at your own risk.
All content in the hotline, except where indicated otherwise, is the property of ARSA. This content may not be reproduced, distributed or displayed, nor may derivatives or presentations be created from it in whole or in part, in any manner without the prior written consent of ARSA.
ARSA grants its members a non-exclusive license to reproduce the content of the hotline. Employees of member organizations are the only parties authorized to receive a duplicate of the hotline.
ARSA reserves all remaining rights and will use any means necessary to protect its intellectual property.
© 2013 Aeronautical Repair Station Association