2016 – Edition 8 – Sept. 2
Table of Contents
Levanto’s Lead
2016 Strategic Leadership Conference – Montreal
ARSA Works
Legal Briefs
ARSA on the Hill
Regulatory Outlook
Quality Time
Training
Membership
AVMRO News Portal
Upcoming Events
Levanto’s Lead – Is ARSA in Your 2017 Budget?
By Brett Levanto, Vice President of Communications
In May, Sarah MacLeod and Daniel B. Fisher used their hotline columns to highlight ARSA’s need for member support. “The Price of Success” and “It’s an Investment!” highlighted how resource-intensive it is to be the voice of the aviation maintenance industry.
ARSA depends on members to recognize the value of the association’s work and to invest in its and their futures. At this time of year, many organizations are compiling their budgets for 2017—it is the time to ensure ARSA has a place in that financial plan. It is also an opportunity for individuals to plan the time needed to participate in the association’s events and activities. These actions assure, ensure and insure that any time or money spent equates to an equally high return on investment.
Think of your support for ARSA across five pillars – each is needed for strength:
- Membership – When will yours lapse? Get the dues amount in the budget and keep access to ARSA’s wide range of member benefits.
- Events – The Annual Repair Symposium is the civil aviation maintenance community’s premier event for regulatory compliance and networking. Equally important but more labor intensive is the Strategic Leadership Conference. A small, discussion-focused venue for long-range compliance planning and networking. Book the time and earmark travel funds to ensure participation.
- Training – Did you know ARSA’s constantly-expanding training library already has more than 30 on-demand sessions for immediate viewing? Budget for your whole team to “attend” throughout the year—money expended will be returned triple-fold the next time a compliance issue raises its head.
- Sponsorship – Event content, publicity programs and member resources are a result of the generosity of industry partners who invest in ARSA through sponsorship. Set aside funds to help highlight the good work of your company and further the efforts of the association.
- Member getting member campaign—who or what other business can help you get something for free? Ten percent of every paid members’ dues you refer will be credited to your membership fee; at the same time, you can benefit from contact with potential partners, suppliers or customers.
Find a way to work for ARSA; the association will be able to continue providing an unprecedented return on investment.
2016 SLC – Oct. 5-6, 2016
By ARSA Membership Team
The ARSA Strategic Leadership Conference provides industry leaders from around the world an informal setting to discuss important issues facing aviation maintenance. Federal agencies, congressional leaders, customer representatives and industry partners are invited to share ideas, objectives and solutions to common issues.
Registration is now open for the 2016 SLC, hosted in Montreal at the headquarters of the International Air Transport Association (IATA). For the first time, ARSA has opened the previously invitation-only event to the broader aviation maintenance community. Space is extremely limited to facilitate discussion between attendees; register now to ensure you have a seat at the table. (Click here to add the SLC to your Microsoft Outlook Calendar.)
For more information and to register, click here.
Gold Sponsors |
||
![]() |
Gold |
![]() |
![]() |
Gold |
Silver Sponsors
|
||||
![]() |
![]() |
![]() |
||
![]() |
![]() |
![]() |
Supporters |
||||
![]() |
s |
![]() |
![]() |
Click any sponsor logo to visit the organization’s website.
Kickoff Reception – An Evening with Michael Lawson
By ARSA Membership Team
Thank you to First Aviation Services for its Gold Level Sponsorship of the 2016 Strategic Leadership Conference, hosted by IATA in Montreal on Oct. 5-6.
Specifically, First Aviation’s support will give attendees an evening reception, during which they could meet the Honorable Michael Lawson, the United States’ Ambassador to ICAO. As a special guest at the SLC’s kickoff event on Wednesday, Oct. 5, Ambassador Lawson will share his thoughts on the American role in the global aviation community.
SLC Space is Limited – Register Now
Register now to meet the ambassador on Wednesday night and stick around for a full Thursday agenda, which includes more speakers from ICAO in addition to representatives from IATA, the FAA and other international aviation bodies. Share your expertise and benefit from your colleagues’ insight during discussions of international regulatory cooperation, technical workforce development and global political risk.
When the U.S. Senate confirmed Ambassador Lawson in 2014, ARSA profiled him for the hotline newsletter. As you plan your trip to Montreal, take a look back at that edition and learn a little about the ambassador: Click here.
Accommodations – Don’t Sleep in the Cold
By ARSA Membership Team
Time is running out to book hotel accommodations for the 2016 Strategic Leadership Conference in Montreal. Since you’ll need your rest before and after a full day of in-depth discussion with maintenance industry executives, you’d better reserve a room before the Sept. 5 deadline.
Hotel accommodations have been arranged at the W Montreal, just across Square Victoria from IATA.
W Hotel Montreal
901 Square Victoria
Montreal, Quebec, H2Z 1R1, Canada
Group rate for SLC attendees has now passed. Please contact Caroline Kneip (caroline.kneip@arsa.org) directly should you need to make a reservation.
ARSA Works
To see all the ways ARSA works as the voice of the aviation maintenance industry, visit the ARSA Works page.
ARSA Supports FAA’s Resolution of “Vexing” Housing Issue
By ARSA Regulatory Team
On Aug. 25, ARSA supported the FAA’s interim final rule clarifying that repair stations holding a limited airframe rating did not need to provide housing that enclosed the largest type of aircraft listed on its Operations Specifications (OpsSpecs).
The association applauded the agency’s efforts to resolve this vexing issue, although conducting a rulemaking was unnecessary. The agency could have simply interpreted the hangar requirement as applying only to repair stations working on aircraft instead of airframe components. Both terms are clearly defined in 14 CFR § 1.1; abiding by the plain text of the regulations would have obviated the need to create a new rule to conform existing agency practice.
For further analysis, check out the “Legal Brief” in this edition.
CRI ARC Members Add Clarity to RCCB Proposal
By ARSA Regulatory Team
On Aug. 24, ARSA joined five other members of the Consistency in Regulatory Interpretation Aviation Rulemaking Committee (CRI ARC) on comments on FAA Draft Order 8000.RCCB, “Regulatory Consistency Communication Board (RCCB).”
The group praised the agency for creating the RCCB, one of the CRI ARC’s six recommendations. To assist in that process, the submission provided a series of suggestions to eliminate vagueness from the board’s structure and authority as described in the draft order.
“While the draft order provides a more streamlined process, the devil is in the details,” the comments said. “The procedure must be in enough detail to ensure it can be followed, audited and appropriate metrics gathered for review and analysis for validity and/or improvement of the process or its outcomes.”
The group’s specific suggestions include establishing a clear decision-making hierarchy, delineating the RCCB’s role with regard to other vehicles for regulatory resolution (e.g., requests for legal interpretations, CSI submissions) and identifying a person or position ultimately responsible for ensuring intended outcomes. These improvements will enable the board to effectively promote consistency of regulatory interpretation and application in line with the CRI ARC’s original report.
The association’s regulatory team helped organized signatories on the comments, which were drafted by the General Aviation Manufacturers Association. Representatives from the Aerospace Industries Association, Airlines for America, the National Air Carrier Association and the Regional Airline Association also signed.
To read the comments in full, click here.
Help ARSA, AMT Magazine Celebrate Young Aviation Talent
By ARSA Communications Team
ARSA’s commitment to building the aviation maintenance workforce of the future means celebrating the excellence of the men and women who already keep the world safely in flight. The association encourages its members to celebrate outstanding young personnel through Aircraft Maintenance Technology Magazine’s Next Gen Awards.
Criteria for selection include job commitment, industry involvement and contribution, professional achievement and innovation. Anyone working in any aviation maintenance field who will be 39 years old or younger on Nov. 1, 2016 is eligible for nomination. Winners will be featured in the magazine’s November/December issue and celebrated on AviationPros.com.
Click here to learn more and nominate someone today.
Anyone submitting a nomination is encouraged to contact ARSA’s Vice President of Communications Brett Levanto, so the association can join AMT Magazine in celebrating the best of this community’s young talent. Through its experience with the awards program in 2015, ARSA saw first-hand the vital importance of celebrating the maintenance industry’s most valuable resource: its people.
Legal Briefs
Editor’s note: This material is provided as a service to association members for educational and informational purposes only. It does not constitute legal or professional advice and is not privileged or confidential.
Housing Requirements – Out with the Old, in with the Old?
By Ryan Poteet, Regulatory Affairs Manager
On Aug. 25, ARSA supported the FAA’s interim final rule clarifying that repair stations holding a limited airframe rating did not need to provide housing that enclosed the largest type of aircraft listed on its Operations Specifications (OpsSpecs). While ARSA applauds the agency’s efforts, this vexing issue could have been resolved in a much easier way. Moreover, the interim rule could have eliminated other problems down the road.
The Old Rule
Previously, 14 CFR § 145.103(b) required repair stations holding any airframe rating to have a hangar to enclose the largest aircraft on its OpsSpecs. The plain language of the rule seemed to mandate that repair stations holding any airframe rating must be able to house the largest aircraft it maintained. The FAA took the language to mean that airframe component-only repair stations would not be forced to have a costly hangar that would sit vacant because the facility never worked on an aircraft. For years the FAA issued countless limited airframe ratings to component repair stations that did not have a hangar.
The FAA’s pragmatic approach to the housing requirements came to an abrupt halt in 2015 when a legal interpretation indicated that the housing requirements applied to all airframe ratings, despite the fact that most did not work on aircraft. Aviation safety inspectors then started taking a second look at the large number for component repair stations without hangars. Although no official legal action was taken against repair stations, some were stopped from expanding capabilities, others were told to apply for exemptions, and applicants were placed in limbo. Instead of interpreting the housing requirement as applying only to repair stations working on aircraft instead of airframe components – as those terms are clearly defined by 14 CFR § 1.1 – the agency worked hard and fast to issue a new rule.
The New Rule
The new rule removed § 145.103(b) to ensure repair stations need only provide housing and facilities consistent with their ratings and limitations, as already required by § 145.103(a)(1). For example, now a repair station with a limited powerplant rating may list a certain make and model of powerplant under its limited rating, but intend to maintain only specified component parts of the engine, such as blade or vane repairs. Under the new rule the repair station is only required to provide housing, equipment, materials, and personnel to perform maintenance on blades and vanes.
It is too bad that the agency didn’t apply the same logic to its rating system.
Performance-Based Rating System
Section 145.61(a) gives the FAA discretion to issue limited ratings for work on any particular type of airframe, powerplant, propeller, accessory, or part thereof, as well as for specialized maintenance functions. This performance-based approach enables the agency to determine whether a repair station has the capability to perform the work in accordance with part 43. Unfortunately, the agency still provides a menu of potential limited ratings in § 145.61(b), which has only functioned to limit the FAA’s ability to issue the appropriate rating when the work does not fit neatly into that list. The result—just as with the housing requirement—has been the issuance of limited ratings to repair stations that do not comply with the plain language of the regulation.
Instead of removing § 145.61(b) entirely, as it did § 145.103(b), the agency included a “catch all” limited rating in § 145.61(b)(13). The provision allows the agency to issue a rating for any other purpose it deems appropriate, which is already allowed under
§ 145.61(a).
It’s unclear why the FAA took a performance-based approach to the housing requirements but not for issuing ratings. It should have deleted the menu of options in
§ 145.61(b) and used its discretionary authority in § 145.61(a).
ARSA on the Hill
Show Me What You Got
By Daniel B. Fisher, Vice President of Legislative Affairs
Editor’s Note: This is the third part in a series on being an active constituent. If you have not read the first two installments, navigate using the links below:
Constituents Matter: Congressional State/District Offices
How to Be an Involved Constituent: Town Hall Meetings
If this Congress’ FAA reauthorization process has demonstrated anything, it’s that few elected officials really understand how our industry operates. The easiest way to ensure that your lawmakers understand your business and the positive impact your company has on the both local economy and aviation safety is to host them at your company’s facilities.
Facility visits give members of Congress and legislative staff an opportunity to see first-hand and up close what your company does and how it fits into the aviation industry. It’s also an opportunity for lawmakers to meet your employees (whose votes they want to win) and to show their commitment to the local business community.
Here are simple steps for you to follow when inviting lawmakers for a facility visit. Remember that representatives and senators have tremendous demands on their time, so you must be flexible in scheduling a tour and even be willing to have a congressional staffer come and visit.
Steps to inviting your member of Congress:
Determine your lawmakers. To find your representative and senators, visit freeenterpriseaction.com/9avEPgM. On the upper right-hand side, you can find your lawmakers by entering your address and zip code. Clicking on respective links allows you to view a background and contact information page for each of your elected officials, including websites, Twitter and Facebook pages and Washington, D.C. contract info.
Locate scheduler contact information. Go to arsa.org/wp-content/uploads/2016/08/ARSA-SchedulerList-20160830.xlsx and search the excel spreadsheet for your lawmakers’ schedulers. If the scheduler isn’t listed, please contact us.
Draft an email to the scheduler. Use ARSA’s facility visit request template and be sure to enter pertinent information where indicated. Either place on company letterhead and send as an attachment or copy into the body of an email.
Let us know you’ve sent the request. Either copy me on your request or send a copy after the fact so the legislative team can follow up.
If you don’t receive a response. One week after sending the letter to your lawmaker, call their congressional office to verify that they received your invitation. Tell them your name, what company you’re from and when you sent the request; then ask about the likelihood of a tour, possible timing and be sure to offer that staff may come if the member is not available. Congressional staff are the “issue experts” for members, and it’s just as important that they understand your business!
Schedule the meeting/visit. Once the site visit or meeting is scheduled, let ARSA’s legislative team know. We’ll send you an ARSA briefing packet with information about specific issues you may want to raise, as well as useful background information about your congressional representative.
Enjoy! Make sure you capture the event with photographs. You can share these photos with the visiting member of Congress, who may even display a photo in his or her office. Give them a hat, t-shirt, or other takeaway with your company’s logo so they’ll remember the visit.
Let ARSA know what happened. Whether it’s a facility visit or office meeting, let ARSA know you’ve been in touch. As a politically active member, you may even be featured in ARSA’s publications! Be sure to forward us some of those pictures too!
Keep communication going. Setting up a visit or meeting is an important first step. However, many members find keeping an open dialogue with their congressional staff is beneficial to their business, and the industry. Although we encourage you to talk about the issues important to the industry, businesses face problems every day and sometimes congressional intervention can help. So be sure to keep those communication lines open!
Taking the initiative to invite a member of Congress to your facility is an easy and fun way to raise the profile of your company and your industry. And it’s a great way to build relationships with legislators that will serve your interests down the road.
If you have any questions about planning or scheduling a tour, let me help.
ARSA Tells Congress to Address the Industry’s Skilled Worker Shortage
By ARSA Legislative Team
On Aug. 19, ARSA delivered a letter to the U.S. House of Representatives urging strong support and swift approval of bipartisan legislation to reauthorize, reform and improve the Carl D. Perkins Act, the primary dedicated federal funding source for career and technical education (CTE) programs.
The association’s membership consistently cites the skilled technical worker shortage as a top policy concern. In 2014, ARSA and the Aviation Technician Education Council (ATEC) commissioned a report by researchers at the College of William & Mary examining the aviation industry’s workforce issues. The study, Policy Solutions for a Stronger Technical Workforce, found that with expanding global markets and increased demand for a highly skilled, government-certificated labor force, aviation businesses must overcome looming retirements of more experienced employees, skill gaps and regulatory restrictions on training programs to service current customers and grow to meet new demand.
“Finding the right people with the right skills is difficult, keeping them is even harder,” said Brett Levanto, ARSA’s vice president of communications, nothing three quarters of respondents to the association’s most-recent member survey reported difficulty finding qualified candidates. “Almost universally, our members are optimistic about their business futures. Aviation markets are growing and international partners are coming together, but repair stations can’t be sure they’ll have the technicians they need to take advantage.”
The bipartisan Strengthening Career and Technical Education for the 21st Century Act (H.R. 5587) is a significant step to addressing the skills crisis that plagues just about every U.S. economic sector, from aviation to manufacturing to construction. Specifically, the legislation includes much needed reforms to the Carl D. Perkins Act, which Congress hasn’t reauthorized since 2006, including:
- Aligning CTE programs to the needs of the regional, state and local labor markets.
- Supporting effective and meaningful collaboration between secondary and postsecondary institutions and employers.
- Increasing student participation in work-based learning opportunities.
- Promoting the use of industry recognized credentials and other recognized post-secondary credentials.
In the letter, ARSA’s Vice President of Legislative Affairs Daniel B. Fisher wrote, “Simply put, by making technical education a priority, Congress can help better prepare workers for well-paying careers, ensure that U.S. companies are able to seize new business opportunities and make the United States more competitive in the global economy. Businesses, schools and government officials must collectively commit to tackling the technical education crisis at all levels, and you can take a great step towards enabling that commitment by supporting and swiftly passing H.R. 5587.”
The legislation, which was unanimously approved by the House Education and the Workforce Committee in July, could receive consideration on the House floor when Congress returns to Capitol Hill after Labor Day.
The association encourages members of the aviation maintenance community to get active in support of CTE overhaul. To weigh-in with your lawmakers in support of Perkins Act reauthorization visit: ofmk.freeenterpriseaction.com/VsvkKKI.
On Demand Training: Congressional Testimony
By ARSA Training & Legislative Teams
As the voice of the aviation maintenance industry, ARSA wears a path across Capitol Hill every day. While the association’s legislative team has a deep bench of contacts and long experience sharing the good work of repair stations, lawmakers often need to hear the message directly from their constituents.
As business leaders, community members and technical experts, ARSA members are perfect participants for congressional hearings – MRO executives, managers and technicians can provide the hands on experience and real world insight that legislators need to make good laws.
Join Christian A. Klein and Daniel B. Fisher to make sure you understand why you should want to testify before Congress…and how to own the committee room when you do.
Instructors: Christian A. Klein & Daniel B. Fisher
Click here to register and get access for 90 days.
Registration for an ARSA-provided, on-demand training session includes:
- Unlimited access for 90 days to the recording.
- A copy of the presentation and all reference material with links to relevant resources and citations.
- Upon completion of the class as well as any test material, a completion certificate.
The association’s training program is provided through Obadal, Filler, MacLeod & Klein, P.L.C., the firm that manages ARSA. To go directly to OFM&K’s online training portal, visit PotomacLaw.inreachce.com. To learn more about the association’s training program and see course availability, visit arsa.org/training.
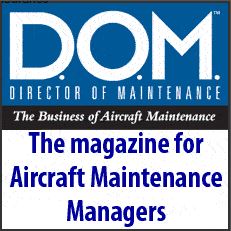
Regulatory Outlook
FAA Confirms Parts Documentation Privileges But Problems Remain
By ARSA Regulatory Team
Update since original release on Aug. 29: On Aug. 31, the FAA issued a revised Notice 8900.380 that clarified the language in paragraph 5.b(1) and (2) to confirm a repair station’s privilege of performing an inspection on any new part received without the documentation required by the MAG. The privilege applies regardless of whether the new part was received before, on or after Oct. 1, 2016. The agency retained the original issue date and Notice number; the revised document is available on the agency’s FSIMS web site at the link below:
http://arsa.org/wp-content/uploads/2016/08/n8900_380_20160831.pdf
On Aug. 29, the FAA, in coordination with the European Aviation Safety Agency (EASA), issued Flight Standards Notice 8900.380 to Aviation Safety Inspectors (ASIs) with oversight responsibility for U.S. repair stations that hold EASA Part-145 certificates. The notice addresses two outstanding issues involving Change 6 to the FAA-EASA Maintenance Annex Guidance (MAG CHG 6).
First, the notice confirms that a repair station may inspect and approve for return to service any new part within its ratings that does not meet the MAG CHG 6 documentation provisions. This codifies a verbal agreement reached on June 17, 2016 at the Maintenance Management Team (MMT) meeting in Washington, D.C. with the FAA, EASA, other national aviation agencies (NAAs) and industry representatives. It confirms such inspections are to be handled like other maintenance activities; Notice 8900.380 describes the agencies’ expectations. (ARSA is developing a procedure that its members may use to accomplish these inspections.)
Second, the notice confirms that the implementation (i.e., compliance) date for the new parts documentation provisions of MAG CHG 6 is Oct. 1, 2016. Some ASIs have been requesting changes to EASA Supplements by Sept. 1, 2016 (90 days after MAG CHG 6 was effective or issued). Therefore, the Notice confirms the Oct. 1, 2016 implementation date for the parts documentation provisions.
“This is a fine step,” said Sarah MacLeod, ARSA’s executive director, noting that the FAA’s confirmation of a repair station’s right to approve a part for return to service is on a long list of the association’s victories related to the MAG’s requirements. ARSA has worked tirelessly to “smooth” implementation of the MAG’s parts documentation requirements since September 2015. The association’s leadership has mitigated far costlier burdens on production approval holders (PAHs) and repair stations that must comply with these new requirements after Oct. 1.”
However, the effort to reverse course on this misguided policy is not over; the industry is awaiting further clarification regarding what parts will be ‘grandfathered” in accordance with the NOTE in MAG CHG 6. ARSA has asked EASA to adopt the reasonable definition of ‘grandfathered inventory.’
“All parts released by the PAH before Oct. 1 with the correct documentation should be grandfathered, period. To limit grandfathered parts only to those in a repair station’s inventory on September 30 instead of focusing on documentation received from the PAH is a wasteful step not only for the agencies but also every maintenance certificate holder, supplier, and customer,” MacLeod said.
To read the complete notice, click here.
For full coverage of the parts documentation issue, stay tuned to arsa.org/MAG.
On Demand – Update on MAG Changes 5 & 6
By ARSA Regulatory Team
Access the update from ARSA’s regulatory team on the parts documentation requirements created by changes 5 and 6 to the U.S.-EU Maintenance Annex Guidance (MAG). Benefit from clarifying questions asked during the live session and discussion of items of specific concern to participants.
Listening Session & Update: U.S.-EU MAG Parts Documentation Requirements
Session Lead: Marshall S. Filler
Click here to register and get access for 90 days.
Registration for an ARSA-provided, on-demand training session includes:
- Unlimited access for 90 days to the recording.
- A copy of the presentation and all reference material with links to relevant resources and citations.
- Upon completion of the class as well as any test material, a completion certificate.
The association’s training program is provided through Obadal, Filler, MacLeod & Klein, P.L.C., the firm that manages ARSA. To go directly to OFM&K’s online training portal, visit PotomacLaw.inreachce.com. To learn more about the association’s training program and see course availability, visit arsa.org/training.
IRS Proposes Significant Restrictions to Estate Tax Discounting Rules
By ARSA Regulatory Team
On Aug. 4, the Internal Revenue Service (IRS) issued a notice of proposed rulemaking (NPRM) restricting the discounting of shareholder stock in family-owned operations for the purpose determining federal estate tax liability. Under current law, married couples are allowed $10.9 million in a lifetime exclusion for federal estate and gift taxes. Assets above the threshold are taxed at a 40 percent federal rate.
Traditionally, the IRS and the courts, for purposes of the federal estate and gift taxes, have permitted the valuation of privately-owned business interests to include a “lack of control” and “lack of marketability” discount because some stakes are worth less since they are harder to sell or represent a minority interest. The proposed rule, which applies to corporations, partnerships and limited-liability companies, disregards any restrictions on liquidation or redemption an heir uses to claim a valuation discount if that restriction either lapses after the transfer or the heir or heir’s family has the ability to remove the restriction after transfer. The IRS is also seeking to eliminate the lack of control discount to assignees.
The agency is accepting comments on its proposal until Nov. 2 and will host a public hearing in Washington, D.C., on Dec. 1.
Final Documents/Your Two Cents
This list includes Federal Register publications, such as final rules, Advisory Circulars and policy statements, as well as proposed rules and policies of interest to ARSA members.
Quality Time
State Department Relaunches Company Visit Program to Assess ITAR Compliance
By Thomas McVey, Esq. and Williams Mullen, a firm of more than 200 attorneys that blends law, government relations and economic development across 16 practice areas.
Editor’s Note: Readers with questions about import and export compliance issues – particularly relating to the application of ITAR – should review Thomas McVey’s previous submissions:
Controlling Your Imports and Exports
Export Compliance: Challenges for Repair Stations (ITAR)
Export Administration Regulations – The Cornerstone of Compliance
And register for the upcoming free webinar:
ITAR and Export Controls For Aeronautical Repair Station Operators
The State Department’s Directorate of Defense Trade Controls (DDTC) has relaunched its Company Visit Program to review compliance activities under the International Traffic In Arms Regulations (ITAR). With its resumption, every repair station with activities regulated under ITAR must understand how the Program works.
Companies are selected for a one to two day visit by DDTC Compliance Office officials under DDTC’s screening criteria. Visits include meetings with senior executives and compliance personnel to review the company’s activities. DDTC has recently issued additional information about the program, including a series of Frequently Asked Questions,[1] The following selected FAQ’s are instructive:
What is the Company Visit Program?
The Company Visit Program entails visits by DDTC officials to U.S. entities registered with DDTC as manufacturers, exporters or brokers of defense articles and defense services, as well as others involved in ITAR-regulated activities, to include foreign companies and foreign governments.What is the purpose of the Company Visit Program?
The program has several purposes. First, it ensures DTCC understands how compliance programs are implemented in accordance with ITAR. Second, the program enables DDTC to gather information to support the directorate’s development of regulatory policy and practice. Finally, DTCC uses site visits to glean, assess and disseminate industry best practices, provide feedback to individual companies on their compliance programs, and share information on compliance programs industry-wide.How is the DDTC team staffed for each visit?
A team typically consists of two or more staff from DDTC, depending on the size of the individual company/site being visited and number of companies/facilities visited per trip. On some visits, staff members from DDTC’s Offices of Licensing and Policy, or other relevant agencies, may participate. One DTCC team member serves as team lead and primary point of contact with the company.How is a visit conducted and what should a company expect?
Once a company is selected for a potential visit, DTCC contacts the company for scheduling. The company can elect not to participate in the visit. Once visit dates are finalized, DTCC sends the company a formal visit notification letter and may request pre-visit materials. Before the visit, DTCC will work with the company to finalize the agenda.At the visit’s opening, DTCC meets with senior management to explain the purpose and agenda. The company should provide an overview of its operations and export activity during opening discussions. Visits generally last one to two days, depending on the purpose and occur on the company’s premises in offices and conference rooms and include tours of business operations departments. At the visit’s conclusion, the DDTC team briefs company senior management and export control staff to share information the team gathered. DDTC invites the company to provide feedback, ask questions, or raise concerns for follow-up.
After the visit, the DDTC team generates an internal report. The team also follows up on company feedback. DTCC will send a formal close-out letter to the company to summarize the visit, indicate best practices, recommend areas for improvement and address feedback, questions or concerns raised by the company. DTCC also requests feedback on the visit’s quality and usefulness and suggestions for improving the program.
It is important to be ready if DDTC requests a visit with your company. Companies are advised not to wait until the last minute but rather have their ITAR compliance house in order in prior to being contacted for a visit.
To make sure your house is in order, join a free export compliance webinar on Thursday, Sept. 8. The session is provided as a benefit to ARSA members, click here for more information and to register.
This article contains general, condensed summaries of actual legal matters, statutes and opinions for information purposes. It is not meant to be and should not be construed as legal advice. For more information, please visit www.williamsmullen.com or contact Thomas B. McVey, 202.293.8118 or tmcvey@williamsmullen.com.
[1] See DDTC company guidance “Company Visit Program (CVP), dated July 17, 2016, available on DDTC website.
Training
The association’s training program is provided through Obadal, Filler, MacLeod & Klein, P.L.C., the firm that manages ARSA. To go directly to OFM&K’s online training portal, visit potomaclaw.inreachce.com. To learn more about the association’s training program and see course availability, visit arsa.org/training.
ARSA’s Rules for Rulemaking
By ARSA Training Team
ARSA’s mastery of the rulemaking process is central to the association’s service to the aviation maintenance community. Faithful followers of “ARSA Works” web posts and newsletter stories will see regular engagement with the FAA and other agencies through their requests for “notice and comment” on various proposals promulgated through the Federal Register.
Every certificate holder should proactively participate in the work of creating, refining and (sometimes) canceling the rules by which the repair station industry is governed. Getting the Code of Federal Regulations – in addition to the litany of agency guidance – right is a shared responsibility that can only be pursued through understanding the rules of rulemaking engagement…from the team that does it every day:
The Rulemaking Process – Overview
Description: This session provides an overview of how federal agencies make regulations that have the force and effect of law. Specifically, it will review the agencies that must follow the Administrative Procedure Act, the procedures governed by the Act as well as other methods by which an agency can obtain recommendations from the public on its rulemaking activities and mandates.
Date & Time: September 14 at 2:00 p.m. EDT
Instructor: Sarah MacLeod
Click here to register (bundle pricing available).
The Rulemaking Process – Effective Comments
Description: This session provides methods for submitting effective comments on FAA rulemaking proposals and on other documents that are posted for feedback from stakeholders.
Date & Time: September 28 at 11:00 a.m. EDT
Instructor: Sarah MacLeod
Click here to register (bundle pricing available).
In addition to participation the live session, registration for an ARSA-provided training session includes:
- Access to the on-demand, recorded version of the webinar to be made available after the live session is complete (or at time of purchase, for on-demand classes).
- A copy of the presentation and all reference material with links to relevant resources and citations.
- Upon completion of the class as well as any test material, a completion certificate.
The association’s training program is provided through Obadal, Filler, MacLeod & Klein, P.L.C., the firm that manages ARSA. To go directly to OFM&K’s online training portal, visit PotomacLaw.inreachce.com. To learn more about the association’s training program and see course availability, visit arsa.org/training.
Hit Me – Three Part Series on Part 21
By ARSA Training Team
Join Marshall S. Filler for a three-part series on 14 CFR part 21, “Certification Procedures for Parts and Articles.” Bundle pricing is available for purchase of the entire series:
Click here to purchase all three sessions together and save.
Part 21 – Overview
Description: This session provides an overview of the aviation safety regulations governing design and production of civil aviation products and articles, and airworthiness certification of civil aircraft.
Date & Time: September 23 at 11:00 a.m. EDT
Instructor: Marshall S. Filler
Click here to register (bundle pricing available).
Part 21 – Type & Production Certificates
Description: This session reviews the elements necessary to obtain design approvals for civil aviation products, including type certificates, amended type certificates and supplemental type certificates. It will explain the requirements for obtaining approval of design changes to those certificates including the changed product rule. Finally, it will describe the design requirements for obtaining a parts manufacturer approval and technical standard order authorization, and for obtaining approval of design changes to those articles.
Date & Time: October 21 at 11:00 a.m. EDT
Instructor: Marshall S. Filler
Click here to register (bundle pricing available).
Part 21 – TSOA, PMA & Other Approvals
Description: This session explains the requirements for obtaining a production approval for civil aviation products and articles. It will explain the elements of an FAA-approved quality system and the method for making revisions to that system. It will also address the privileges and responsibilities of production approval holders including the issuance of airworthiness approvals for aircraft engines, propellers and articles.
Date & Time: November 9 at 11:00 a.m. EST
Instructor: Marshall S. Filler
Click here to register (bundle pricing available).
In addition to participation the live session, registration for an ARSA-provided training session includes:
- Access to the on-demand, recorded version of the webinar to be made available after the live session is complete (or at time of purchase, for on-demand classes).
- A copy of the presentation and all reference material with links to relevant resources and citations.
- Upon completion of the class as well as any test material, a completion certificate.
The association’s training program is provided through Obadal, Filler, MacLeod & Klein, P.L.C., the firm that manages ARSA. To go directly to OFM&K’s online training portal, visit PotomacLaw.inreachce.com. To learn more about the association’s training program and see course availability, visit arsa.org/training.
Free Webinar: Export Compliance Session Provided by Williams Mullen for ARSA
By ARSA Training Team
On Sept. 8, Thomas B. McVey, chair of the international section at Williams Mullen and resource for ARSA members, will host a free webinar on export controls for repair stations.
The session is part of ongoing collaboration between ARSA and McVey, who displayed his experience in international business law during a presentation at the 2016 Annual Repair Symposium and is the author of a continuing series in the monthly hotline newsletter on import/export issues. By joining the free session on Sept. 8, maintenance providers can put his knowledge and experience to good use:
ITAR and Export Controls for Aeronautical Repair Station Operators
Description: An overview of export controls with specific application and examples for parties dealing with aircraft parts, aviation technical services and repairs for commercial and military aircraft.
Date & Time: September 8 at 12:00 at 1:00 p.m. EDT
Instructor: Thomas B. McVey
Click here to register directly with Williams Mullen.
Registration note: This session is hosted by Williams Mullen. Clicking the registration link will direct to the firm’s registration system. A confirmation email will be sent upon registration containing instructions for accessing the session.
By ARSA Training Team
Maintenance providers deal with numerous administrative agencies of the U.S. government. Above and beyond the typical oversight provided American businesses by the departments of Labor, Health, Commerce and others, repair stations must have an intimate understanding of the FAA and NTSB. Get to know these key actors within “the fourth branch of government.”
The Fourth Branch of Government – Administrative Agencies: The FAA & NTSB
This course will review the creation and powers of the two agencies most prominent in civil aviation – the Federal Aviation Administration and the National Transportation Safety Board.
Instructor: Sarah MacLeod
Click here to register and get access for 90 days.
Also On Demand...
Administrative Agencies & Their Powers
Administrative Agencies & Their Powers
Instructor: Sarah MacLeod
Description: This session reviews why federal administrative agencies are created and how they use their powers to regulate activities within their jurisdiction. The course will also cover the basic procedures agencies must follow to create or revise regulations.
Registration for an ARSA-provided, on-demand training session includes:
- Unlimited access for 90 days to the recording.
- A copy of the presentation and all reference material with links to relevant resources and citations.
- Upon completion of the class as well as any test material, a completion certificate.
The association’s training program is provided through Obadal, Filler, MacLeod & Klein, P.L.C., the firm that manages ARSA. To go directly to OFM&K’s online training portal, visit PotomacLaw.inreachce.com. To learn more about the association’s training program and see course availability, visit arsa.org/training.
Help Your Regulatory Knowledge Travel Well with “Going Global” Training Bundle
By ARSA Training Team
International markets mean expanded business opportunities that require an understanding of international regulatory requirements. This session focuses on bilateral airworthiness agreements (BAA) and bilateral aviation safety agreements (BASA). Topics include the purpose and scope of these agreements, the process required to obtain a BASA and how BASAs are structured. The presentation explains specific activities covered in a typical BASA including design approvals and post-design approvals, production and surveillance, export airworthiness approvals, technical assistance between authorities and special arrangements. It also covers bilateral maintenance agreements, their associated special conditions and the latest maintenance developments out of ICAO.
Instructor: Marshall S. Filler
Click here to register and get access for 90 days.
Also On Demand...
Going Global - A Primer on International Regulatory Law
Going Global
Instructor: Marshall S. Filler
Description: This session summarizes the framework for international safety regulation, introduces ICAO’s mechanisms for allocating regulatory responsibilities among member states and addresses the important role bilateral agreements play in enhancing efficiency and facilitating international commerce.
On-Demand – Available Anytime
Registration for an ARSA-provided, on-demand training session includes:
- Unlimited access for 90 days to the recording.
- A copy of the presentation and all reference material with links to relevant resources and citations.
- Upon completion of the class as well as any test material, a completion certificate.
The association’s training program is provided through Obadal, Filler, MacLeod & Klein, P.L.C., the firm that manages ARSA. To go directly to OFM&K’s online training portal, visit PotomacLaw.inreachce.com. To learn more about the association’s training program and see course availability, visit arsa.org/training.
Regulatory Compliance Training
By ARSA Training and Regulatory Teams
Test your knowledge of 14 CFR § 43.5 – Approval for return to service after maintenance, preventative maintenance, rebuilding or alteration.
Click here to download the training sheet.
Special Event: ITAR and Export Controls for Aeronautical Repair Station Operators – Sept. 8 (Free)
The Rulemaking Process – Overview – Sept. 14
Part 21 – Overview – Sept. 23
The Rulemaking Process – Effective Comments – Sept. 28
Antitrust 101 – Oct. 12
Part 21 – Type & Production Certificates – Oct. 21
Part 21 – TSOA, PMA & Other Approvals – Nov. 9
Membership
ARSA Members Featured at Regional Aerospace Event
By ARSA Membership Team
In conjunction with the 2016 Southeastern Aerospace Supplier and Advanced Manufacturing Summit in Winston-Salem, North Carolina, executives representing ARSA members First Aviation Services, Piedmont Propulsion Systems, HAECO Americas and North State Aviation participated in a panel discussion about issues and opportunities for aviation maintenance companies.
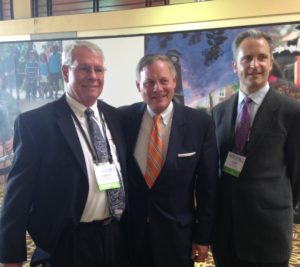
Sammy Oakley, Piedmont Propulsion Systems (left) and First Aviation’s Krotec (right) meet Sen. Richard Burr (R-N.C.) (center) during the Summit.
Josh Krotec, First Aviation Service’s senior vice president and 2016 ARSA Government Affairs Chairman, Kip Blakely, HAECO Americas’ vice president of industry and government relations and James McPhail, North State Aviation’s vice president of strategic planning, spoke about a range of topics pertaining to the aviation maintenance industry, its customers and its suppliers. Specific issues included opportunities for repair stations to support Department of Defense aircraft maintenance requirements and working with local technical schools to ensure a long-term supply of aviation maintenance technicians.
Emphasizing the importance of participating in industry events First Aviation’s Krotec said: “We believe it is imperative in order to promote solutions to issues that all repair stations face and foster discussion of how MROs, aircraft operators and the government can work together to improve safety, airworthiness, and efficiency.”
“It was a very worthwhile conference and great opportunity for networking with other members of the aerospace industry,” said North State’s McPhail. “I’d encourage all ARSA members to participate in these kind of events in their local areas to gain insights about the industry, make new contacts, and learn about the challenges and opportunities facing aerospace companies.”
Member Spotlight – Canadian Aero Accessories
By ARSA Communications Team
In honor of the 2016 SLC’s Canadian location, this month’s Member Spotlight shines on a repair station in Calgary, Alberta.
Canadian Aero Accessories has more than 50 years of experience servicing regional, charter and corporate operators. The company employs a wide range of technical abilities across its electronic, machine, hydraulic, fuel and safety system departments. In conjunction with a library of 16,000 current manuals and stores stocking 1.5 million dollars of certified parts, CAA is dedicated to rapid customer support and prides itself on best-in-class aircraft on ground support.
CAA’s in-house abilities and extensive parts inventory mean no waiting for sub-letting to get components airworthy. The repair station prioritizes human factors training for all employees to ensure quality and safety are priority.
CAA is a new ARSA member. To learn more about its experience and specialties, visit www.cdnaero.com.
Have You Seen This Person? – William R. Voss, Air Navigation Commissioner, ICAO
Bio From The U.S. Mission to the International Civil Aviation Organization (ICAO), icao.usmission.gov
William Voss was nominated by the United States to the ICAO Air Navigation Commission in 2014.
The Air Navigation Commission is a panel of 19 independent experts appointed by countries from around the world. They advise the ICAO Council on the adoption of international standards and oversee the technical panels that develop those standards. Previously Voss served as the President and CEO of the Flight Safety Foundation, an independent non-profit organization that supports international aviation safety activities. During his tenure at the foundation was a widely recognized as an advocate for aviation safety and worked around the world with senior officials, regulators and industry partners to promote best practices and address emerging safety challenges. Prior to that he was the Director of the Air Navigation Bureau at ICAO where he directed the development of international standards, guidance material and the implementation of global programs, such as the implementation of Safety Management Systems and the ICAO Universal Safety Oversight Audit Program.
Voss has been a key resource in the development of the Strategic Leadership Conference agenda. He will share his unique perspective with attendees during lunch on Oct. 6. Don’t miss out, register now.
Make ARSA’s Voice Your Own: Advertise!
ARSA has a menu of advertising opportunities for arsa.org, the hotline and the ARSA Dispatch.
Take advantage of these great opportunities today to showcase your company, a new product or event. For more information go to arsa.org/advertise.
Exhibit, Sponsor the 2017 Repair Symposium
As the maintenance industry’s top event devoted exclusively to regulatory compliance, the ARSA Symposium attracts a highly qualified professional audience.
Use this opportunity to promote your company while showing support for ARSA. Get more information at arsa.org/news-media/events/arsa-symposium/arsa-annual-repair-symposium-sponsorship.
Q: My aviation safety inspector is adamant that I must calibrate my inspection and test equipment to the standard recommended by the manufacturer rather than establish intervals by the equipment’s type, usage and history. Is that correct?
A: Not according to the part 145 final rule preamble, which emphasizes establishing intervals based upon the type and use of the equipment. Specifically, the agency stated:
“The FAA has revised paragraph (b) as proposed to require that a repair station ensure that all test and inspection equipment and tools used to make airworthiness determinations are calibrated to a standard acceptable to the FAA. The FAA will issue guidance regarding what standards will be acceptable to the FAA. The FAA has issued numerous exemptions from the current requirement that calibration be to a standard derived from the NIST when the alternative standard has been accepted by the NIST as adequate. The intent of this provision is to provide more regulatory flexibility. The FAA notes that this paragraph no longer requires that the equipment be calibrated at ‘‘regular’’ intervals. The interval at which measuring and test equipment is calibrated depends on the type and use of the equipment; therefore, the word ‘‘regular’’ does not adequately describe when the equipment should be calibrated. The FAA notes that § 145.211(c)(1)(viii) requires that a repair station’s quality control manual contain a description of the systems and procedures for calibrating measuring and test equipment used in maintaining articles, including the intervals at which the equipment will be calibrated.” (66. Fed. Reg. 41088, August 6, 2001.)
The FAA has since issued guidance in its AC, which is currently under revision, but does not change in the calibration interval and standard aspects—see AC 145-9, issued 7/3/2003, Para 4-12. Also, check out Order 8900.1, Vol. 3, Ch. 9, Sec. 9, Para 6-1800(B), which provides other standards acceptable to the FAA for calibration purposes.
AVMRO News Portal
ARSA strives to provide resources to educate the general public about the work of the association’s member organizations; should you need to provide a quick reference or introductory overview to the global MRO industry, please utilize AVMRO.ARSA.org.
AVMRO Industry Roundup
ARSA monitors media coverage on aviation maintenance to spread the word about the valuable role repair stations play globally by providing jobs and economic opportunities and in civic engagement. These are some of this month’s top stories highlighting the industry’s contributions.
You can explore these stories through ARSA’s Dispatch news portal.
Upcoming Events
the hotline is the monthly publication of the Aeronautical Repair Station Association (ARSA), the not-for-profit international trade association for certificated repair stations. It is for the exclusive use of ARSA members and federal employees on the ARSA mailing list. For a membership application, please call 703.739.9543 or visit http://arsa.org/membership/join/. This material is provided for educational and informational purposes only. It does not constitute legal, consulting, tax or any other type of professional advice. Law, regulations, guidance and government policies change frequently. While ARSA updates this material, we do not guarantee its accuracy. In addition, the application of this material to a particular situation is always dependent on the facts and circumstances involved. The use of this material is therefore at your own risk. All content in the hotline, except where indicated otherwise, is the property of ARSA. This content may not be reproduced, distributed or displayed, nor may derivatives or presentations be created from it in whole or in part, in any manner without the prior written consent of ARSA. ARSA grants its members a non-exclusive license to reproduce the content of the hotline. Employees of member organizations are the only parties authorized to receive a duplicate of the hotline. ARSA reserves all remaining rights and will use any means necessary to protect its intellectual property.
© 2016 Aeronautical Repair Station Association