2017 – Edition 10 – November 3
Table of Contents
Note: The order of material varies in hotline emails, but is always presented the same on this landing page. Readers scrolling through content on or printing this page will find it organized consistent with the table of contents.
Sarah Says
SLC 2017
ARSA Works
Legal Briefs
ARSA on the Hill
Quality Time
Training
Membership
Resources
Industry Calendar
Sarah Says
Not So Fast
By Sarah MacLeod, Executive Director
A key facet of ARSA’s work is to see things through until the end – no matter how long it takes, how many times the association is told “no” or how many “experts” tell it to give up.
This determination stems from the leadership of ARSA’s management firm, Obadal, Filler, MacLeod & Klein, P.L.C. (see an example in this edition’s “Legal Brief”). The long experience of the firm’s lawyers has taught them that managing the intersection of business and government is not a task for those who scare easily.
When you’ve invested time and effort into an outcome, it feels great to celebrate the achievement. However, seeing things through to the end requires discipline; you can’t assume the job is done or rely on the word of others without confirming for yourself and knowing how to follow up.
An Oct. 25 article posted to Aviation Week’s MRO Network indicated that the FAA is “looking for industry professionals who want to join an [ARAC] working group that will endeavor to improve Part 145 repair station guidance material.” Unfortunately, we’re not quite there yet. ARSA has worked hard (and long) to get ARAC tasked to overhaul guidance related to the repair station rule, but the actual task has not yet been issued by the FAA or accepted by the rulemaking advisory body.
When the work is underway, ARSA will take a leading role – it’s active and well-documented support of ARAC makes the association perfectly situated to perform this work – and interested industry professionals should be ready for support. However, even if someone inside the agency is hankering to form the working group, the effort of making it necessary is not yet done.
ARSA will see it through, just like it always does.
SLC 2017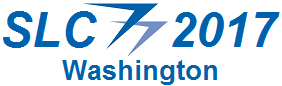
MRO Leaders “Engage for Effect” at 2017 ARSA SLC
By Christian A. Klein, Executive Vice President
Gaining visibility is critical in Washington, D.C. There are thousands of organizations competing for limited attention from policymakers on Capitol Hill and in the executive branch. Having the ear of government officials is critical to shaping legislation (like the pending FAA bill) and regulatory policy (the rules themselves and how they’re enforced).
With the new administration and new Congress, ARSA has made “engaging for effect” a theme in 2017. It’s imperative that government decisionmakers know that there IS an aviation maintenance sector (you’d be amazed by how many don’t!), understand what we do and how government actions affect maintenance markets, costs of doing business and efficiency.
Engagement was the theme of ARSA’s 2017 Strategic Leadership Conference (SLC), which was held in Washington, D.C. on Oct. 18 and 19. Dozens of senior executives representing ARSA member companies from around the world converged on the city to make our industry’s voice heard.
Over the course of the two-day conference, attendees got up close and personal with the U.S. government. FAA Administrator Michael Huerta presented a keynote speech that emphasized the importance of cooperation between government and industry to build on our outstanding safety record. Former ICAO Air Navigation Commissioner Bill Voss highlighted opportunities to engage internationally to make regulation more efficient. A panel of senior executives from AAR, HAECO Americas and First Aviation discussed strategies for affecting government outcomes. Another team of experts from HEICO, NORDAM and the cargo airline industry discussed ways to support the development of independent repairs. To top it off, a senior executive from Southwest Airlines discussed operator priorities in the FAA reauthorization debate.
But participants didn’t just sit in their seats all day, they actively engaged. Attendees first divided into groups and met with lawmakers on Capitol Hill. Then the focus shifted to the executive branch with a visit to the White House complex to meet with administration officials to discuss regulatory reform, tax policy and career technical education. The message from the administration was loud and clear: We want to work with the industry and we need your input.
Attendees came away from the conference both with new insights about what’s happening – and what might happen – in the Washington, D.C. and, just as importantly, how to affect the process.
We need to keep the momentum going and aggressively insert maintenance into policymaking. ARSA is a strong advocate for your interests, but you must be as well. The next opportunity to come to the nation’s capital and help move our collective agenda forward is March 14 – 16 when the association will be hosting its Legislative Day and Annual Repair Symposium. Mark your calendars and plan to join us for what’s sure to be another top-flight learning and engagement opportunity.
To see everything that happened when maintenance leaders “engaged for effect” in Washington, D.C., visit review this edition of the hotline or visit arsa.org/slc-2017.
What Happened In Washington
See what happened when the maintenance community “engaged for effect” in the American capital:
Online: arsa.org/slc-2017
Twitter: @ARSAWorks, @caaklein, @LevantoAir and #AVMROSLC17
Digital Companion for Participants (Password Protected): arsa.org/slc-materials-2017
What is SLC? Click here to visit the main event page to learn more. Interested in ARSA events, including the 2018 Legislative Day and Annual Repair Symposium? Click here to see the association’s event calendar.
Thank you to all 2017 SLC sponsors. To learn more about the organizations that stepped up to facilitate engagement for the maintenance community, click the logos below.
Gold Sponsors
![]() |
![]() |
|
![]() |
![]() |
|
![]() |
![]() |
Silver Sponsors
![]() |
![]() |
|
![]() |
![]() |
|
![]() |
![]() |
Supporters
![]() |
![]() |
|||
![]() |
![]() |
Component Repair Technologies & A Moment of Calm
Special thanks to Component Repair Technologies for its Gold Level Sponsorship of ARSA’s 2017 Strategic Leadership Conference in Washington, D.C. As participants took on a full schedule of events, meetings, receptions and engagement, CRT’s support provided a moment of calm during Thursday’s networking break.
CRT helped maintenance industry leaders focus as they “engaged for impact” in the U.S. capital.
AAR, Early Rising & a White House Briefing
Special thanks to AAR Corp. for its Gold Level Sponsorship of ARSA’s 2017 Strategic Leadership Conference in Washington, D.C. The company’s support put participants’ Thursday breakfast on the table. After starting early, attendees needed that energy to tackle the SLC’s full agenda, which included a White House policy briefing.
AAR Corp. helped maintenance industry leaders rise to the occasion as they “engaged for impact” in the U.S. capital.
HAECO Americas & The Boss
Special thanks to HAECO Americas for its Gold Level Sponsorship of ARSA’s 2017 Strategic Leadership Conference in Washington, D.C. The company is a long-time supporter of the association and lent its name to this year’s keynote address, which was provided by FAA Administrator Michael Huerta.
Through its commitment to SLC, HAECO Americas took the lead on behalf of maintenance senior executives as they “engaged for impact” in the U.S. capital.
ARSA Works
New ARSA Guidance Clarifies Duty-Free Aviation Parts Importation Rules
ARSA has released new guidance aimed at helping the aviation maintenance industry import parts for repair in order to more efficiently do business internationally.
Under U.S. law and international agreements, many aircraft parts may be imported into the United States duty-free. However, inconsistent interpretation of Customs rules has forced repair stations to divert resources to navigating a complex regulatory web and in some cases paying import duties they do not owe.
ARSA’s new Advisory 2017-01 provides an overview of the World Trade Organization’s Agreement on Trade and Civil Aircraft and rules adopted in the United States to implement the treaty obligations. The document also delves into relevant Customs regulations and legal opinions to answer a basic question: Must parts be airworthy to qualify for duty-free treatment? ARSA’s conclusion, with which Customs concurs, is that airworthiness is not a relevant factor in the duty-free determination. The association’s guidance examines the various conditions that must be met to avoid tariffs and identifies best practices to properly document imports. The association has also released a new on-demand training session (see below) about the parts importation issue.
The guidance and training were developed in direct response to questions raised by ARSA members at the association’s 2017 Symposium in Washington, D.C. “Issues like the tariff treatment of aircraft parts and inconsistent enforcement have a direct impact on our members’ bottom lines,” ARSA Executive Vice President Christian A. Klein said. “We hope these new resources, particularly [Advisory 2017-01], will help repair stations save time and money while more efficiently serving their international customers.”
The guidance is available for free to ARSA members and may be ordered by visiting arsa.org/publications or completing the form below.
To see all of the association’s resources for establishing duty-free rates, visit arsa.org/regulatory/customs.
An on-demand session describing the issue and reviewing the advisory is available in this edition’s training section.
Have Regulatory Reform Ideas? The White House Wants to Hear Them
With all the media stories about what the Trump administration has not accomplished, few have focused on an important untold story: the success of the president’s regulatory reform initiatives.
During his first six months in office, President signed 14 resolutions passed by Congress under the Congressional Review Act undoing regulations adopted during the last year of the Obama administration. Prior to Trump taking office, the CRA had only successfully been used once before. While intelligent people will disagree about the merits of the regulations repealed under the CRA, Congress and the administration have demonstrated how effectively it can be used at the start of an administration to undo policies put in place by the new president’s predecessor.
In addition to the legislative CRA activity, the White House is pushing regulatory reform within the executive branch from the top down and bottom up. President Trump has issued several executive orders relating to regulatory issues, including requiring two regulations to be repealed for each new regulation issued, a net-zero economic impact of newly adopted regulatory policies, and the formation of bodies within every agency to review regulations and recommend improvements. Trump’s new department and agency heads have also sought to undo Obama-era regulations seen as harmful to the economy.
While the Trump administration clearly has specific rules in its crosshairs, during ARSA’s recent Strategic Leadership Conference, White House officials made it clear they want additional input about regulations that need to change or go away entirely. With that in mind, there is a significant opportunity for associations like ARSA to recommend regulatory changes. Since the association has worked aggressively through ARAC for aviation-safety-related matters, it is particularly interested in hearing about non-FAA issues (e.g., EPA, OSHA, etc.) that affect repair stations.
Members with regulatory reform ideas should contact Christian Klein at christian.klein@arsa.org.
U.S., China Continue Bilateral Cooperation with “Risk Based” IPA
On Oct. 17, the FAA and the Civil Aviation Administration of China (CAAC) concluded Implementation Procedures for Airworthiness (IPA) under the Bilateral Aviation Safety Agreement (BASA) signed by the United States and China in 2005. The purpose of the IPA is for both agencies to define the civil aeronautical products and articles eligible for import into each country, the process for obtaining eligibility for import and the means for providing continued support.
The IPA provides paths to approval through both acceptance and validation. Applications for validation will determine what kind of approval is necessary – streamlined, limited or full technical – by analyzing 15 Safety Elements. These elements, as part of the work plan to be co-developed by the FAA and CAAC, will dictate the scope and depth of the validating authority’s technical review.
“This IPA with China is the first bilateral established with an emerging partner that employs a risk-based, systems approach to validation,” the FAA said in an announcement message to industry stakeholders. “It is a full scope, reciprocal agreement, which means that the terms apply equally to either authority when acting as the validating or certificating authority. While each authority will apply the same processes, the results, with respect to the level of involvement, may vary greatly.”
The agreement is posted on the bilateral agreement listing section of the FAA website: www.faa.gov/aircraft/air_cert/international/bilateral_agreements/baa_basa_listing. For aviation businesses, Aircraft Certification Office branches can help with questions regarding specific projects.
Final Documents/Your Two Cents
This list includes Federal Register publications, such as final rules, Advisory Circulars and policy statements, as well as proposed rules and policies of interest to ARSA members.
Legal Briefs
Editor’s note: This material is provided as a service to association members for educational and informational purposes only. It does not constitute legal or professional advice and is not privileged or confidential.
Compliance Over a Dead Body – Lessons on a Long-Fought-For Exemption
By Sarah MacLeod, Executive Director and Brett Levanto, Vice President of Communications
When dealing with a regulator, being “right” only gets you half way. You have to be accurate in your interpretation of the rules, armed with the technical capabilities and data to reinforce your position and then willing to see it through until the end (see “Not So Fast” in this edition).
The ARSA website is littered with examples (the association’s team is still “fighting for your right to surrender” three years after the update to 145.55…and that’s nothing). Recently, though, the association’s management firm Obadal, Filler, MacLeod & Klein, P.L.C. provided a case in point by virtue of an indefatigable client.
In 2014, Stone Aviation International (SAI) obtained foreign military surplus UH-1 composite main rotor blades. They had been produced to an FAA-approved design and possessed the same part numbers as blades produced in the United States by the design and production approval holder. Though they were manufactured according to the specifications of those on American military helicopters, the specific blades had been manufactured for and declared surplus by a foreign military. As a result, they failed to meet the criteria in 14 CFR § 21.9(c) requiring military articles be declared surplus by the U.S. armed forces in order to be sold as suitable for installation on type-certificated aircraft.
Initially, there was mass confusion about where the blades fell in the regulations. After the company queried the FAA, the agency’s personnel reached consensus that they could not be sold for use or used on restricted category helicopters.
Facing this initial refusal, SAI contacted OFM&K. Based on the firm’s counsel and supported by data collected from various designees, mechanics, rotor blade repair specialists, consultants and agency personnel, the company developed an initial “pathway for approval.” Unfortunately, the proposal faced additional misunderstanding within the agency before being delegated to the company’s principal maintenance inspector (PMI).
After an apparently successful audit and examination, the Flight Standards Service indicated the blades would subsequently be add to Advanced Composite Structures Florida’s (ACSF) capability list. Unfortunately, the agency never followed through – SAI was forced to go back to the compliance drawing board.
We constructed a new plan: OFM&K would spearhead a request for exemption under Advanced Composite Structures Florida’s (ACSF), the FAA repair station with appropriate ratings and capabilities. The request would be based on verifiable data, the company’s inspection of the blades against the design specification and the aviation safety rules’ fundamental requirements of airworthiness. Based on the new approach, both the firm and its new client were confident despite the countless aviation lawyers, compliance firms and even FAA officials consulted by the company who insisted the blades were a “dead end.”
The request for exemption was submitted in January, 2017 and supplemented in June before its acceptance was finally published in September – four years and multiple rejections after the blades were initially purchased. The exemption allows ACSF to maintain the rotor blades and offer them to restricted category operators. It requires the company to issue an FAA form 8130-3 for each. The maintenance release will be based upon the proprietary process submitted during the exemption process and added to the repair station’s quality procedures. The process is the reason the FAA accepted ACSF’s assertion that it can establish each blade meets agency-approved design, operating and maintenance requirements. This is the first time the agency has granted an exemption on foreign military surplus articles.
“ACSF has requisite design and production data and historical records to enable it – and the FAA – to make competent airworthiness determinations,” the grant of exemption states. “The FAA agrees with ACSF that this exemption would be in the public interest because many restricted category type-certificated helicopters…fly missions under contract for federal, state and local governments.”
Good data supported the exemption, but OFM&K made it happen. When the SAI/ACSF first went looking for compliance help, other lawyers said ‘no.’ Everyone said ‘no.’ There were even some voices at the FAA whose ‘no’ was accompanied by an ‘over my dead body.’ The firm (and ARSA) can say ‘yes’ – or at least ‘why not’ – more often than others because our team understands the reality of the aviation safety rules. We don’t stop after one reading of a regulation and we sure as hell won’t stop because of an unsupported ‘no’ from a regulator.
ACSF is now working to fulfill the obligations of the exemption, which will allow the long-awaited delivery of those composite main rotor blades to market. As business ramps up, both ARSA and OFM&K will continue to share news, updates and lessons-learned from the process. Stay tuned to both the hotline and Dispatch and review content at potomac-law.com/blades-pay-off.
ARSA on the Hill
FAA Bill on the Back Burner While Congress Focuses on Tax Reform
By Christian A. Klein, Executive Vice President
Just before the hotline went to press, the nation’s capital got its first look at the long-awaited tax reform bill from the House Ways & Means Committee, the Tax Cuts and Jobs Act. The prospects for tax reform were given a big boost in recent weeks with passage of budget resolution that will allow the tax legislation to avoid a filibuster by Senate Democrats.
The focus on taxes has taken the spotlight off FAA reauthorization, ARSA’s top legislative priority for the current Congress. Much of the FAA bill, which establishes a multi-year budget blueprint for the agency and gives Congress the opportunity to affect aviation policy, is non-controversial. However, the bill has been held up in the House by language that would privatize the nation’s air traffic control system and in the Senate by a provision that would provide more flexibility for pilot training. Given the challenges of resolving those issues and the fact that the current FAA funding law doesn’t expire until March 31, Congress has turned its attention to taxes, one of the Trump administration’s top agenda items.
On first look, the House tax bill mirrors priorities announced earlier this year by senior administration officials and congressional leaders. For businesses, that would mean lowering the corporate tax rate to 20 percent, reducing rates for pass-through companies, changing the way U.S. companies operating internationally are taxed and 100 percent expensing of capital investments. The number of tax brackets for individuals would be reduced to three, the alternative minimum tax would be repealed and the standard deduction would be increased and simplified.
While the broad parameters have been known for some time, there are myriad details yet to be worked out. In recent days, the focus has been on whether the changes would be done immediately or phased-in over a period of years to reduce the negative budget impact. There has also been considerable speculation and anxiety about the possible fate of current deductions and credits as lawmakers look to simplify the tax code and reduce the cost of tax reform.
The home mortgage interest deduction has attracted particular attention. Although the tax reform framework developed by administration and congressional negotiators would preserve the interest deduction, raising the standard deduction would mean fewer taxpayers would itemize which would, in turn, reduce the impact of the mortgage provision. That concern led the National Association of Homebuilders, one of the nation’s most powerful lobbying organizations, to come out against the House bill in advance of its release.
As the bill’s potential impact on various industries become clear, it’s a virtual certainty that other lobbying organizations will join NAHB in opposition. That’s not a death knell for tax reform, but it does underscore the challenges with undertaking major overhaul of the code; every provision is there because someone thought it would be a good idea and often fought hard to put it there. Getting tax reform done will building trust in the eventual outcome and require convincing enough people they will be better off under the new system.
ARSA is closely monitoring developments and will prepare an analysis for members as details become clear. In the meantime, we welcome input – particularly from tax and finance experts at member companies – about the possible consequences of reform. Send your comments to ARSA Executive Vice President Christian A. Klein at christian.klein@arsa.org.
FAA Bill Maintenance Amendments Box Score
ARSA Proposal | In House Bill | In Senate Bill |
Adding “aviation maintenance” to stakeholders on new Certification & Oversight Advisory Committee | Yes – Amendment by Rep. Hank Johnson (D-Ga.) and Rob Woodall (R-Ga.) adopted in committee by voice vote | Yes – Amendment by Sen. Jim Inhofe (R-Okla.) adopted in committee by voice vote |
Asking FAA to explore ways to enhance value of repairman certificates | No – Rep. Eddie Bernie Johnson (D-Texas) has filed amendment | Yes – Amendment by Sen. Jim Inhofe (R-Okla.) adopted in committee by voice vote |
Directing FAA to undertake rulemaking to reinstate voluntary surrender of repair station certificates | No – Rep. Dan Webster (R-Fla.) has filed amendment | Yes – Amendment by Sen. Jim Inhofe (R-Okla.) adopted in committee by voice vote |
Directing GAO to study causes, effects and solutions to aviation technician shortage | Yes – Amendment by Rep. Cheri Bustos (D-Ill.), Brenda Lawrence (D-Mich.) and Bruce Westerman (R-Ark.) adopted in committee by voice vote | No – ARSA is working to identify sponsor |
Creating grant program to support aviation maintenance workforce development initiatives | No – ARSA is working to identify sponsor | No – Sens. Jim Inhofe (R-Okla.) and Richard Blumenthal (D-Conn.) planning to sponsor amendment on Senate floor |
Say Thanks To Our Champions!ARSA is fortunate have several members of Congress are going to bat for repair stations and supporting maintenance-related FAA bill amendments. If someone from your state is on the list below, please shoot a quick note of thanks. It doesn’t have to be anything fancy and could be as simple as: “Thank you for your leadership on aviation maintenance issues in the FAA bill. As a member of the YOURSTATE repair station industry, I sincerely appreciate your efforts on our behalf.” (Clicking on the names below will open up a blank email address to their aviation staffers.) |
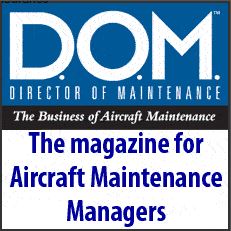
Quality Time
Editor’s note: The views and opinions expressed by contributing authors do not necessarily state or reflect those of ARSA and shall not be used for endorsement purposes.
Is My Company Required to Register Under ITAR?
By Thomas McVey, Esq., Williams Mullen
Note: This article contains general, condensed summaries of actual legal matters, statutes and opinions for information purposes. It is not meant to be and should not be construed as legal advice. For more information, please visit our website at www.williamsmullen.com or contact the author.
A frequently asked compliance question from companies dealing with government contracts is whether they are required to register under the International Traffic In Arms Regulations (ITAR).
ITAR are State Department controls that regulate defense products, technical data and services. Under 22 CFR §122.1, parties that manufacture, export or temporarily import “defense articles” or furnish “defense services” are required to register with the Directorate of Defense Trade Controls (DDTC) within the State Department. It is important to note that even parties engaging solely in domestic manufacturing of defense articles are required to register even if they do not import or export. Under § 122.1, engaging in such activity “requires only one occasion of manufacturing or exporting, or temporarily importing, a defense article or furnishing a defense service” to trigger this registration requirement. In addition, parties that engage in defense “brokering” (see below) and freight forwarders that perform services under the Foreign Military Sales program are also required to register under ITAR.
Defense Articles
Defense articles are any items that are listed on the U.S. Munitions List defined in § 121.1. The USML is a list of twenty-one categories of items covering a wide array of products, parts, components, technical data, software and services that are useful in defense applications. These include products in the aerospace, maritime, communications, IT/computer/software, electronics, optical, toxicological/biological and other industries. To assess if a company is required to register, it must start by reviewing the USML to determine if products or services with which it is involved are listed.
Companies that frequently are required to register under ITAR include:
- Federal contractors involved in defense, intelligence, security, homeland security and energy contracts;
- Subcontractors and second/third tier suppliers of parts, components, subsystems, accessories and attachments used in such contracts;
- IT, computer, software, data security and similar firms involved in defense applications;
- Companies engaged in projects involving classified information (USML Category XVII is “Classified Articles, Technical Data, and Defense Services”);
- Companies engaged in the repair, refurbishment and maintenance of defense products and systems, and logistics activities related to such items;
- Companies that perform military training or provide military advice; and
- Companies that receive research grants and contracts from the DOD including under SBIR and similar programs;
- Manufacturers of firearms, ordinance and related equipment, gunsmiths;[1]
- Universities (especially those that receive research grants and contracts from defense agencies); and
- Firms involved in engineering and technical services related to defense projects.
Since the USML covers not just end items but also certain subsystems, parts and components, many second and third tier suppliers that do not consider themselves to be in the defense industry are nonetheless required to register. In addition, firms that merely perform services and do not supply any products may be required to register in certain circumstances.
48 CFR Subpart 225.79 and § 252.225-7048
It has become common for federal prime contractors involved in defense projects to require their subcontractors to register under ITAR, and this has created significant confusion among subcontractors and suppliers. This requirement is due in part to the Defence Federal Acqusition Regulations (DFARS) 225.79 and 252.225-7048,[2] which apply to many federal defense contracts.[3] Based on these requirements, prime contractors are increasingly concerned that if their subcontractors commit ITAR violations (such as failing to register), the prime contractors could also have liability. Consequently, prime contractors are frequently requiring that their subcontractors register under ITAR and adopt ITAR compliance programs. If a prime contractor is registered, this does not relieve the subcontractor of the responsibility to register separately – each firm must conduct its own assessment and register individually if required. Subcontractors that are registered and have ITAR compliance programs in place often create less compliance risk for prime contractors and thus are frequently more desirable candidates for subcontract awards.
ITAR registration is a mechanism for the U.S. Government to track firms involved in the U.S. defense industry. In addition, registration is a prerequisite for a company to apply to DDTC for licenses, Technical Assistance Agreements (TAAs) and other authorizations. Since it takes up to 60 days for a registration to become effective, failure to register can result in significant delays in obtaining licenses, TAAs and authorizations. DDTC also advises that registration is required for a company to rely on ITAR exemptions.
Registration Procedure
As part of the registration process, the registrant is required to submit documentation that demonstrates it is incorporated or otherwise authorized to do business in the United States. The registration documents must include a certification by an authorized senior officer stating if the registrant, its affiliates and officers, directors and principals (i) have ever been indicted, charged or convicted of violating certain criminal laws; or (ii) are ineligible to contract with or receive export/import licenses from the U.S. Government. In addition, the registrant must identify if it is owned or controlled by a foreign party, and provide an explanation of such ownership or control, including the identities of the foreign person or persons who ultimately own or control the registrant.
Penalties
Penalties for ITAR violations include civil and criminal fines of up to $1,000,000 per violation and 20 years imprisonment, including personal liability for the company’s officers, directors and employees. Failure to register is listed as an ITAR violation in 22 CFR § 127.1(b)(2) and (b)(3).[4]
Exemptions and Broader ITAR Requirements
There are certain exemptions from the registration requirement.[5] However it is important to note that even if a company is exempt from registration, it may still be subject to other requirements under ITAR and therefore not relieved of the responsibility for complying with these other requirements. Such requirements include:
- Obtaining export and temporary import licenses for the export/import of defense articles.
- Obtaining authorizations for the transfer/disclosure of ITAR-controlled technical data and software to foreign nationals in the U.S. (including foreign national employees of the U.S. contractor).
- Entering TAAs authorized by DDTC for the performance of defense services.
- Restrictions on reexports and retransfers and reporting and recordkeeping requirements.
(A more detailed list of requirements under ITAR are set forth in ITAR For Government Contractors, published by WilliamsMullen.)
Brokers and FMS Freight Forwarders.
Registration is also required for ITAR “brokers” under 22 CFR § 129.3. Brokers are parties that facilitate the sale or transfer of ITAR-controlled products, services and technical data by others, even if they are not direct principals in the transaction.[6] Brokers are also subject to other requirement under ITAR including the requirement to obtain advance authorization from DDTC for certain transactions, reporting requirements, recordkeeping requirements and restrictions on engaging in transactions involving countries identified in 22 CFR § 126.1. In addition, as referenced above, pursuant to ITAR § 126.6(c)(6)(i), U.S. freight forwarders performing services under the Foreign Military Sales (FMS) program are required to register with DDTC.
Empowered Official.
Registrants are required to appoint an “empowered official” as part of the registration process. This is a U.S. person directly employed by the registrant that has a position of authority for policy and management within the company and is:
(i) legally empowered by the registrant to sign license applications;
(ii) understands the requirements of the export laws and penalties for violating them; and
(iii) has the independent authority to inquire into any aspect of a proposed transaction, verify the legality of the transaction and refuse to sign any license applications without adverse recourse from the company.
Other Requirements.
Other obligations under the ITAR registration requirement that frequently apply to government contractors include:
- Amendments. If there are changes in the key information submitted in the registration statement, the registrant is required to notify DDTC of such changes in writing within five days of the event.
- Annual Renewal. The registration must be renewed annually, provided that the company continues to engage in activities that trigger the registration obligation.
- ITAR Recordkeeping Requirements. Registrants are required to maintain records of their ITAR activities for a five-year period (and longer in certain instances) pursuant to 22 CFR § 5.
Registration is only part of the broader obligations that may apply to government contractors under ITAR. Contractors should understand the specific requirements that may arise in their particular activities and use care to comply with these in their business operations. For a more detailed discussion of these requirements see ITAR For Government Contractors , published by WilliamsMullen. Additional articles on ITAR, EAR and U.S. sanctions programs are available at: “Export Articles.”
Footnotes
[1] DDTC has provided specific guidance regarding the requirement for gunsmiths to register under ITAR which is available at: https://www.pmddtc.state.gov/compliance/documents/ITARRegReqFirearmsManufacturers.pdf
[2] DFAR 252.225-7048(b) and (e) provide in pertinent part:
(b) The Contractor shall comply with all applicable laws and regulations regarding export-controlled items, including, but not limited to, the requirement for contractors to register with the Department of State in accordance with the ITAR. The Contractor shall consult with the Department of State regarding any questions relating to compliance with the ITAR and shall consult with the Department of Commerce regarding any questions relating to compliance with the EAR. * * *
(e) The Contractor shall include the substance of this clause, including this paragraph (e), in all subcontracts.
[3] These provide that contractors are required to comply with ITAR and the Export Administration Regulations in performing the relevant contracts and are required to “flow down” this requirement to their subcontractors.
[4] 22 CFR §127.1(b)(3) provides as follows: “(b) It is unlawful: * * * (3) To engage in the United States in the business of either manufacturing or exporting defense articles or furnishing defense services without complying with the registration requirements. For the purposes of this subchapter, engaging in the business of manufacturing or exporting defense articles or furnishing defense services requires only one occasion of manufacturing or exporting a defense article or furnishing a defense service.”
22 CFR §127.1(b)(2) provides as follows: “(b) It is unlawful: * * *(2) To engage in the business of brokering activities for which registration and a license or written approval is required by this subchapter without first registering or obtaining the required license or written approval from the Directorate of Defense Trade Controls. For the purposes of this subchapter, engaging in the business of brokering activities requires only one occasion of engaging in an activity as reflected in §129.2(b) of this subchapter.”
[5] 22 CFR §122.1(b) provides as follows: “(b) Exemptions. The registration requirements of paragraph (a) of this section do not apply to:(1) Officers and employees of the U.S. Government acting in an official capacity; (2) Persons whose pertinent business activity is confined to the production of unclassified technical data only; (3) Persons all of whose manufacturing and export activities are licensed under the Atomic Energy Act of 1954, as amended; or (4) Persons who engage in the fabrication of articles solely for experimental or scientific purposes, including research and development.” See also 22 CFR §129.3(b) for exemptions for registration by brokers.
[6] See 22 CFR §129.2.
Thomas McVey is the Chair of the International Practice Group at Williams Mullen in Washington DC where he advises clients on export control issues under ITAR, the Export Administration Regulations and the OFAC Sanctions Laws.
Training
School’s In Session – ARSA’s Experts at 2018 HELI EXPO
Going to HAI HELI-EXPO 2018 in Las Vegas? ARSA’s great regulatory minds will be there, and a front-row seat in their classroom is waiting for you.
Marshall S. Filler and Sarah MacLeod, the association’s foremost experts in regulatory compliance (and managing members of the firm of Obadal, Filler, MacLeod & Klein, P.L.C.) will be leading both professional education courses and rotor safety challenge sessions at HAI HELI-EXPO. Register now to make the most of your time in Las Vegas and get to the head of class.
Though Filler and MacLeod are known for their zealous advocacy on behalf of maintenance organizations, their long experience with compliance issues makes their sessions substantially valuable to any aviation professional.
Professional Education Courses - Provided by OFM&K
Drug & Alcohol Testing Programs: Regulatory Basics to Business Needs
Drug & Alcohol Testing Programs: Regulatory Basics to Business Needs
Feb. 25, 2018 – 1:00 p.m. to 5:00 p.m.
Sarah MacLeod
This course reviews the drug and alcohol testing requirements in Titles 14 and 49 of the Code of Federal Regulations (CFRs). It will also provide guidance on setting up these programs, including instruction on how safety sensitive functions are defined, as well as information about avoiding many common testing program mistakes that can subject companies to enforcement action.
Public Aircraft
Public Aircraft
Feb. 25, 2018 – 8:00 a.m. to Noon
Marshall S. Filler
This course provides instruction on the statutory provisions and FAA guidance governing public aircraft operations. It covers the basic requirements for an aircraft to be operated as a public aircraft, what constitutes an eligible governmental function, and the practical implications of using the same aircraft to conduct both civil and public operations. It also discusses the FAA policy regarding operations conducted under contract for a government entity.
Regulatory Comprehension for Maintenance
Regulatory Comprehension for Maintenance
Feb. 26, 2018 – 8:00 a.m. to Noon
Marshall S. Filler and Sarah MacLeod
This course covers the FAA’s authority, process for promulgating rules, and organization, then walks through the general requirements in Title 14 of the Code of Federal Regulations to explain how its various components are linked together in a “regulatory chain” that must be comprehended by aviation businesses.
Rotor Safety Challenge Sessions - Provided by ARSA
Building a Positive Relationship with the Government
Building a Positive Relationship with the Government
Feb. 27, 2018 – 8:30 a.m. to 9:30 a.m.
This session provides a road map for building a positive relationship with civil aviation authorities. It begins by describing the rules that should always be considered when engaging with aviation safety regulators, then provides instruction on how to introduce your company and maintain consistent contact — not just when there’s a problem. The session concludes by providing strategies for maintaining a professional relationship with regulators.
No pre-registration required.
Best Practices in Maintenance Recordkeeping
Best Practices in Maintenance Recordkeeping
Feb. 28, 2018 – 2:15 p.m. to 3:15 p.m.
This session explores the regulatory responsibilities of creating and maintaining maintenance records. It will help participants to define:
- Regulatory responsibilities of the operator versus the maintenance provider in creating and maintaining maintenance records
- How obligations can be shifted by contract but not under aviation safety regulations
- Maintenance recordkeeping regulations, the documents essential to making airworthiness determinations.
No pre-registration required.
Can’t make it to Las Vegas? The association provides plenty of opportunity for you to learn from its experts. Click here to check out the constantly-expanding library of ARSA online training.
FAA Investigation & Enforcement Powers
This session reviews 14 CFR part 13, which defines the FAA’s powers of investigation and enforcement. It walks through the rule in order to explain its organization and define the procedures and authority contained within each of the nine subparts. To support this general overview, the session highlights key sections and phrases within each subpart.
Instructors: Sarah MacLeod & Brett Levanto
Click here to register and get access for 90 days.
Registration for an ARSA-provided training session includes:
- Unlimited access for 90 days to the recording made available after the live session is complete.
- A copy of the presentation and all reference material with links to relevant resources and citations.
- A certificate upon completion of the class, as well as any test material.
The association’s training program is provided through Obadal, Filler, MacLeod & Klein, P.L.C., the firm that manages ARSA. To go directly to OFM&K’s online training portal, visit PotomacLaw.inreachce.com. To learn more about the association’s training program and see course availability, visit arsa.org/training.
Importing Aircraft Parts for Maintenance – Establishing Duty Free Rates
The session reviews the World Trade Organization’s exemption of civil aviation products and parts from import duties and describes the U.S. implementation of rules and guidance to support duty-free importation. It then walks through the association’s resources for ensuring that eligible imports are made free of Customs tariffs.
Instructor: Christian A. Klein
Click here to register and get access for 90 days.
Registration for an ARSA-provided training session includes:
- Unlimited access for 90 days to the recording.
- A copy of the presentation and all reference material with links to relevant resources and citations.
- A certificate upon completion of the class, as well as any test material.
The association’s training program is provided through Obadal, Filler, MacLeod & Klein, P.L.C., the firm that manages ARSA. To go directly to OFM&K’s online training portal, visit PotomacLaw.inreachce.com. To learn more about the association’s training program and see course availability, visit arsa.org/training.
From the FAA – The Road to Maintenance Perdition
The FAA’s “Maintenance Hangar” on faasafety.gov contains information and resources the agency has produced or compiled to support safety in maintenance operations. The “toolbox” section includes alerts, guidance, tips, training information, posters and handout materials. Members of the maintenance community working on U.S.-registered aircraft should become familiar with these resources; at the very least they help highlight the areas considered most important by the agency.
To provide a taste of the content available in the “maintenance hangar,” this edition of the hotline is taking a look at the FAASTeam’s Notice “Good Intentions + Lack of Knowledge = Fatal Consequences.” Just like the proverb says, the road to Hell is paved with good intentions.
The “Maintenance Hanger” can be found at: www.faasafety.gov/content/TabLanding.aspx?tab=mechanics.
Regulatory Compliance Training
By ARSA Training and Regulatory Teams
Test your knowledge of 14 CFR § 65.14 – Security disqualification.
Click here to download the training sheet.
Membership
AerSale’s Barimo Brings Leadership, Technical Expertise to ARSA Presidency
The ARSA board of directors has announced the election of its new president: Basil Barimo, chief operating officer of AerSale, an international aviation sales and services company based in Coral Gables, Florida. The selection was made during the board’s annual meeting, which followed the 2017 Strategic Leadership Conference in Washington, D.C.
Barimo launched his aviation career in 1987 as an aerospace engineer with McDonnell Douglas before serving in a range of leadership roles with U.S. Airways and then AvBorne Heavy Maintenance. He is personally familiar with the role of aviation trade associations, having worked with airlines and American regulators to shape industry policy as vice president of operations and safety at the Air Transport Association (now Airlines for America). He first joined ARSA’s board when working for the NORDAM Group, where he was executive vice president, repair group prior to accepting the COO position at AerSale in 2017.
ARSA’s board of directors represents a broad range of international maintenance interests. Board members direct the association’s work to best serve the aviation community. Barimo most-recently served as ARSA vice president before moving into the association’s top volunteer leadership position. As an executive for AerSale, a global leader in aftermarket aircraft, material and management services, he will bring both his professional perspective and technical experience to bear on ARSA’s work in 2018. Warner Calvo, 2017 present and director of quality and safety at Coopesa, R.L, will remain on the board as a representative of international members.
“The maintenance industry is changing,” Barimo said. “Markets are growing, technolgy is advancing and our workforce is evolving. While these changes produce new challenges for my colleagues and I, they also reinforce the core importance of ARSA’s role. No matter who our customers are, what equipment we have or who’s doing the work, we need to engage together on behalf of the industry. I’m eager to help lead that work for the next year.”
During the meeting, Dave Latimer, vice president of regulatory compliance for HAECO Americas, was elected vice president and Ian Cheyne, chief technical and regulatory officer of Dallas Airmotive, became treasurer. Barimo, Latimer and Cheyne will each serve one year terms.
For more about the board of directors, click here.
For more about the SLC, click here.
PartnerShip Update – Truckload Shipment Quotes
Do you have a truckload shipment ready to be sent out? One way to quickly and efficiently get it on its way is to have all the information necessary before calling for a quote. Below is a list of tips to follow before picking up a phone or shooting out an email.
(1) Know the Basics Where is the shipment picking up and where is it going? Are appointment times necessary – does the shipment need a specific pickup or delivery time/date? How many pieces, what type of packaging is being used, and what is the weight of the goods? All of these questions need to be answered before getting a truckload rate.
(2) Equipment Type – Truckload shipments can have many different requirements – dry van, flat bed, refrigerated, to name a few. Determining the correct option for your specific shipment is an important part of the truckload shipping process and can affect variables like carrier availability. Need more help determining which equipment your shipment requires? Check out this post on truckload equipment options for more information.
(3) Commodity – What are you shipping? A basic description of the contents is enough to get you an accurate rate on your pending truckload shipment.
(4) Value of the Shipment – It is important to know the value of the goods you are transporting. Even though most carriers have cargo legal liability coverage, typically these policies have limits of $100,000 per trailer; there is no longer any federal requirement for motor carriers to carry cargo insurance. If your shipper knows the value of your move, they should be able to ensure the carrier that moves your load has adequate coverage or even obtain additional coverage if necessary.
PartnerShip, the company that manages the ARSA Shipping Program, offers competitive rates on truckload shipments to all association members! PartnerShip has created relationships with dozens of national and regional truckload carriers to help you save time and money. Even when your freight shipment is a full or partial truckload, requires specialized equipment, or is being exported or imported – PartnerShip has the connections to help you with a solution. Receive a competitive rate on your truckload shipment by visiting PartnerShip.com/TLQuote today. If you have any questions or would like more information about the program, visit PartnerShip.com/ARSA or call 800-599-2902.
Quick Question – Business Breakdown
In order to help its members manage regulatory requirements, ARSA is constantly learning about where repair stations are performing their work. What markets are most important? What new business areas are emerging?
This month’s “Quick Question” borrows from a key question on ARSA’s annual member survey:
Note: Complete the survey directly on this page. You may have to scroll down in the embedded window in order to click the “Done” button.
If you have questions or want to provide additional information, contact Brett Levanto (brett.levanto@arsa.org).
Click here to see what questions have been asked and answered…and keep a lookout for more.
A Member Asked…
Q: This question arose concerning used parts brought into inventory after Oct. 1, 2016 for use in work performed under the U.S.-EU Maintenance Annex Guidance (MAG). Does the MAG require used parts to have a FAA Form 8130-3 in the same manner as for new parts?
My position is that the parts documentation requirements in changes five and six to the MAG are export requirements for new parts and do not extend to used parts. Therefore, used parts brought into inventory after Oct. 1, 2016 do not require FAA Form 8130-3 with dual release.
Please advise if I’m understanding this correctly.
A: Used parts have nothing to do with the October 2016 date. “Used” parts have always required special treatment by the MAG but for different reasons.
When a component is sent to another repair station for maintenance functions, if that repair station is not EASA approved, the originating repair station has to treat the second as a “non-certificated” source, i.e., the second repair station does not have an EASA approval and is therefore “non-certificated” for dual release purposes. In that case, the originating repair station must verify by inspection or test that the work is performed properly. For example, putting the “used” unit that was repaired by a “non-certificated” source in a top assembly and returning that top assembly to service would suffice.
When a component is “recovered” internally from a unit that is beyond economical repair or from another “top assembly” that is owned by the repair station, the “maintenance” of that internal component would be handled in accordance with the RSQM procedures. At the very least the work would be recorded in the “top assembly” work order or in some other manner and yes, the repair station would be performing that work under its FAA/EASA rating and would not need to tag the “internal” part with an FAA 8130-3 provided the work on the “recovered” part is associated with the top assembly or in some other manner explained in the RSQM.
Some repair stations leave the “original” unit’s work order open until all the “repairable” or “serviceable” parts are “used” in other work orders associated with a top assembly. Some repair stations “close” the original work order after “white tagging” the “repairable” or “serviceable” units. In either event, EASA recognizes “internally recovered” parts under its EASA part 145 and the FAA recognized that concept here: arsa.org/continue-in-service.
To see all of ARSA’s work related to the FAA-EASA MAG and parts documentation requirements, visit arsa.org/mag.
Have a question for ARSA? Click here to let us hear it.
Make ARSA’s Voice Your Own: Advertise
ARSA has a menu of advertising opportunities for arsa.org, the hotline and the ARSA Dispatch.
Take advantage of these great opportunities today to showcase your company, a new product or event. For more information go to arsa.org/advertise.
Stand Up for ARSA by Sponsoring in 2017
In order to provide world-class resources for its members, the association depends on the commitment of the aviation community. By sponsoring events and activities, supporters can help ARSA’s work on behalf of repair stations to endure.
Need a place to start? For information about opportunities, including sponsorship of the Strategic Leadership Conference in October (click here for info), contact Vice President of Communications Brett Levanto (brett.levanto@arsa.org).
Resources
ARSA strives to provide resources to educate the general public about the work of the association’s member organizations; should you need to provide a quick reference or introductory overview to the global MRO industry, please utilize AVMRO.ARSA.org.
AVMRO Industry Roundup
ARSA monitors media coverage on aviation maintenance to spread the word about the valuable role repair stations play globally by providing jobs and economic opportunities and in civic engagement. These are some of this month’s top stories highlighting the industry’s contributions.
You can explore these stories through ARSA’s Dispatch news portal.
Industry Calendar
China Aviation & MRO Aftermarket Conference – Shanghai – Nov. 8-9
Commercial Aero Engine Forum – Shanghai – Dec. 5-6
Aerospace & Defence MRO South Asia Summit – New Delhi – Jan. 18-19
Airline Engineering & Maintenance: Middle East – Dubai – Jan. 22
MRO Middle East – Dubai – Jan. 23-24
Aero-Engines Americas – Fort Lauderdale, Florida– Jan. 31-Feb. 1
MRO Latin America – Panama City, Panama – Feb. 14-15
HAI HELI-EXPO – Las Vegas – Feb. 27-March 1
MRO East Asia – Hanoi, Vietnam – March 7-8
ARSA Legislative Day & Annual Repair Symposium – Arlington, Virginia – March 15-17
ATEC Annual Conference – Arlington, Virginia – March 15-17
MRO Americas – Orlando, Florida – April 10-12
Previous Editions
2017: | Jan | Feb | Mar | Apr | May | June | July | Aug | Sept | Oct | ||
2016: | Jan | Feb | Mar | Apr | May | June | July | Aug | Sept | Oct | Nov | Dec |
2015: | Jan | Feb | Mar | Apr | May | June | July | Aug | Sept | Oct | Nov | Dec |
2014: | Jan | Feb | Mar | Apr | May | June | July | Aug | Sept | Oct | Nov | Dec |
2013: | Jan | Feb | Mar | Apr | May | June | July | Aug | Sept | Oct | Nov | Dec |
2012: | June | July | Aug | Sept | Oct | Nov | Dec |
the hotline is the monthly publication of the Aeronautical Repair Station Association (ARSA), the not-for-profit international trade association for certificated repair stations. It is for the exclusive use of ARSA members and federal employees on the ARSA mailing list. For a membership application, please call 703.739.9543 or visit http://arsa.org/membership/join/. This material is provided for educational and informational purposes only. It does not constitute legal, consulting, tax or any other type of professional advice. Law, regulations, guidance and government policies change frequently. While ARSA updates this material, we do not guarantee its accuracy. In addition, the application of this material to a particular situation is always dependent on the facts and circumstances involved. The use of this material is therefore at your own risk. All content in the hotline, except where indicated otherwise, is the property of ARSA. This content may not be reproduced, distributed or displayed, nor may derivatives or presentations be created from it in whole or in part, in any manner without the prior written consent of ARSA. ARSA grants its members a non-exclusive license to reproduce the content of the hotline. Employees of member organizations are the only parties authorized to receive a duplicate of the hotline. ARSA reserves all remaining rights and will use any means necessary to protect its intellectual property.
© 2017 Aeronautical Repair Station Association