April 2013
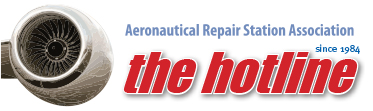
Table of Contents
Latest News
Sarah Says
New ARSA Webinar Program Announced; Navigating Online FAA Resources Next
ARSA Praises European Legislators’ Efforts on ICAs
ARSA Launches Repair Station Security Rule Countdown Clock
ARSA Educates Congress on Economic Impact of MRO Industry
ARSA Releases New State Data Fact Sheets
ARSA Urges House Ways & Means Committee to Simplify Tax Code
Legislative News
Senate Committee Studies Aviation Safety
Obama Signs Legislation to End ATC Furloughs
Obama Administration Releases Budget Proposal
House Members Write White House in Opposition to User Fees
Legal Briefs
ARSA on the Hill
Final Documents/Your Two Cents
Quality Time
Legal Waypoints
Employment Law & Repair Stations
Membership
Member Spotlight
Have You Seen This Person
A Member Asked
Get 10% off on membership dues by utilizing ARSA’s Members getting members program
Advertise Today in ARSA’s Newsletters and Website!
Interested in exhibiting or sponsoring the 2014 Repair Symposium?
Industry News
International News
Welcome New Members
Regulatory Compliance Training
Upcoming Events
Previous 12 issues
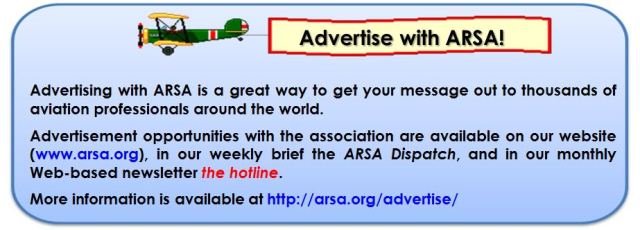
Latest News
By Sarah MacLeod, ARSA executive director
This week ARSA Executive Director Sarah MacLeod discusses the importance of investing in your employees. To read MacLeod’s blog, as well as other commentary issued during the month of April, please visit http://blog.arsa.org/
New ARSA Webinar Program Announced; Navigating Online FAA Resources Next
ARSA’s online training courses are open to anyone interested in learning more about the business of aviation, particularly on regulatory safety subjects. The association revises these courses often, and they are accessible through the WebEx platform.
ARSA’s offering weekly webinars with experts from Obadal, Filler, MacLeod & Klein to address a variety of business and compliance issues confronting the aviation industry. Instructors will work off a PowerPoint presentation which will be provided to participants.
Click here for more information.
ARSA Praises European Legislators’ Efforts on ICAs
On April 19, ARSA sent a letter to two members of the European Parliament commending their recent inquiries to the European Commission regarding original equipment manufacturers making maintenance manuals available to MROs. Read more at http://arsa.org/arsa-praises-european-legislators-efforts-on-icas/
ARSA Launches Repair Station Security Rule Countdown Clock
On March 15, during testimony before the U.S. House of Representatives Transportation Security Subcommittee, Transportation Security Administration (TSA) Administrator John Pistole confirmed that the final repair station security rule is being reviewed by the Office of Management and Budget (OMB). Read more at http://arsa.org/legislative/issues/aviation-policy/lift-the-ban/
ARSA Educates Congress on Economic Impact of MRO Industry
ARSA told Congress in a letter about the significant economic impact the aviation maintenance industry has in communities throughout the country and urged lawmakers to keep the sector’s contributions and safety record in mind when considering legislative proposals. Read more at http://arsa.org/arsa-educates-congress-on-economic-impact-of-mro-industry/
ARSA Releases New State Data Fact Sheets
ARSA recently announced a new report that provides a comprehensive economic review of the Maintenance, Repair and Overhaul (MRO) marketplace. As part of its ongoing efforts to educate political leaders, the association has developed fact sheets highlighting the economic impact the aviation maintenance community has on each U.S. state. Read more at http://arsa.org/news-media/economic-data/
ARSA Urges House Ways & Means Committee to Simplify Tax Code
Aviation maintenance companies need a simpler tax code and greater tax certainty to continue to grow and create jobs ARSA told the U.S. House of Representatives Committee on Ways & Means. Read more at http://arsa.org/arsa-urges-house-ways-means-committee-to-simplify-tax-code/
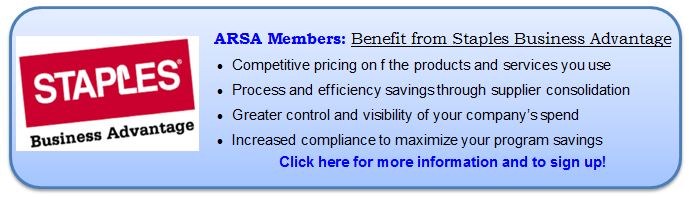
Legislative News
Senate Committee Studies Aviation Safety
On April 16, the U.S. Senate Committee on Commerce, Science, & Technology held a hearing titled “Aviation Safety: FAA’s Progress on Key Safety Initiatives” to discuss the Federal Aviation Administration’s (FAA) headway in implementing aviation safety programs. Read more at http://arsa.org/senate-committee-studies-aviation-safety/
Obama Signs Legislation to End ATC Furloughs
On May 1, President Obama signed legislation that permits the transfer of up to $253 million from the FAA’s Airport Improvement Program (AIP) or any other agency “program or accounts” to its operations budget. Read more at http://arsa.org/obama-signs-legislation-to-end-atc-furloughs/
Obama Administration Releases Budget Proposal
On April 10, the Obama administration unveiled its fiscal year 2014 budget proposal, which contained several policies strongly opposed by the aviation industry. Read more at http://arsa.org/obama-administration-releases-budget-proposal/
House Members Write White House in Opposition to User Fees
In April, 223 members of the U.S. House of Representative wrote President Obama in opposition to the Administration’s continued efforts to support a $100 per flight fee on commercial and general aviation. Read more at http://arsa.org/wp-content/uploads/2013/04/UserFeeLettertoPresident-20130405.pdf
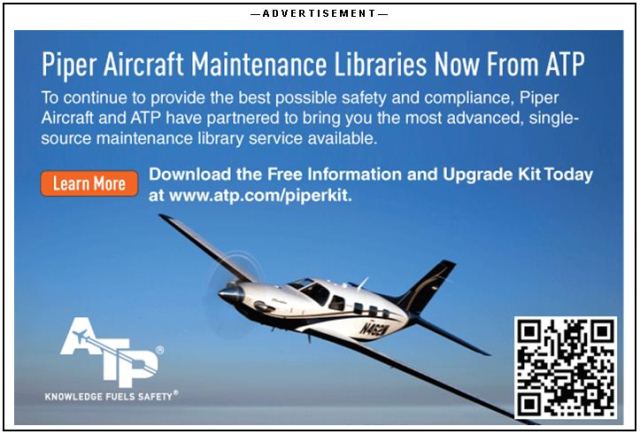
Legal Briefs
The Air Carrier and Repair Station Regulatory Relationship: Part 4
By Craig Fabian, ARSA vice president of regulatory affairs & assistant general counsel
Last month, we explored the general air carrier manual rule in Title 14 Code of Federal Regulations (14 CFR) part 121 and focused on its requirement for “instructions and procedures for maintenance, preventive maintenance, and servicing” (§ 121.135(b)(17)). That provision corresponds with “the methods, techniques, and practices contained in the maintenance manual or the maintenance part of the manual of the holder of an air carrier operating certificate” (§ 43.13(c)) and identifies the “how to” instructions that are the “applicable sections” of the air carrier’s maintenance manual a repair station must follow (§ 145.205(a)), which we discussed in previous articles in this series. Essentially, this is the part of the air carrier manual containing maintenance information and instructions (§121.133) or “the maintenance part of the manual” (§121.137(c)).
In addition to “how to” instructions, the general air carrier manual rule requires the inclusion of time limitations, or standards for determining time limitations, for overhauls, inspections, and checks of airframes, engines, propellers, appliances and emergency equipment (§ 121.135(b)(18)), and airworthiness inspections, including instructions covering procedures, standards, responsibilities, and authority of inspection personnel (§ 121.135(b)(20). A repair station must also account for these “program” items when performing maintenance for an air carrier (§ 145.205(a)). Stated differently, these items control use of the “how to” instructions in the air carrier’s maintenance manual. It does not mean an air carrier’s maintenance program and maintenance manual are one and the same.
Establishing the differences between an air carrier “maintenance manual” and “maintenance program” leads us to the more specific maintenance provisions in the rules (14 CFR part 121, subpart L). As mentioned above, the program dictates application of the “how to” instructions so it is no surprise to find the manual must contain the programs “that must be followed in performing maintenance, preventive maintenance, and alterations of that certificate holder’s airplanes, including airframes, aircraft engines, propellers, appliances, emergency equipment, and parts thereof” (§ 121.369(b)). (As a side note, this provision directly contradicts existing Federal Aviation Administration (FAA) guidance suggesting that an air carrier’s maintenance manual is an element of the air carrier’s maintenance program.)
In other words, there is a direct relationship between the identified “technical elements” of the maintenance program and the instructions for performing the work in the maintenance manual. Indeed, central to the rule describing maintenance program requirements is ensuring that maintenance tasks “performed by [the air carrier], or by other persons, are performed in accordance with the [air carrier’s] manual” (§ 121.367(a)). The focus is clearly on properly following the “how to” instructions in the maintenance manual as dictated by the “technical” aspects of the air carrier’s maintenance program. For repair stations, that rationale is reflected in the fact that it must follow the air carrier’s “program and applicable sections of its maintenance manual” (§ 145.205(a)). The general air carrier program requirements apply (§ 121.367), and the applicable sections of the maintenance manual that must be followed by repair stations are those containing technical aspects of the program and “how to” instructions. The entirety of “program” elements contained in the air carrier manual (§ 121.369(b)(1) through (b)(9)) do not apply to a repair station performing the work.
With the vast majority of air carrier maintenance today being performed by repair stations, it is time for the agency to recognize these regulatory features in its guidance. Distinctions between “administrative” and “technical” program requirements should be made to recognize the role of repair stations and emphasize the work performed.
ARSA on the Hill
By Daniel Fisher, ARSA vice president of legislative affairs
In April, ARSA’s legislation team continued implementing its “lift the ban” lobbying effort and worked with congressional leaders to ensure legislation is ready for introduction by June 14.
On March 15, during testimony before the House Transportation Security Subcommittee, Transportation Security Administration Administrator John Pistole confirmed the Office of Management & Budget is reviewing the final repair station security rule for 90 days. Working with our allies on Capitol Hill, the association’s goal is to have a bill repealing the foreign repair station certification ban ready for introduction by the end of the review period. To watch the countdown, visit http://arsa.org/arsa-launches-repair-station-security-rule-countdown-clock/.
To assist in our lobbying efforts, the association delivered new economic data to Capitol Hill educating lawmakers on the MRO industry’s economic impact.
The legislative team also coordinated the attendance of two congressional staffers (with Florida Sens. Nelson (D) and Rubio (R)) at the April 5 Miami outreach meeting conducted by ARSA Executive Vice President Christian Klein.
Finally, ARSA PAC is ramping up its fundraising for 2013. To learn more about ARSA PAC, visit: http://arsa.org/about-arsa-pac/.
Final Documents/Your Two Cents
“Final Documents”: This list includes Federal Register publications such as final rules, Advisory Circulars (ACs), policy statements and related material of interest to ARSA members. For proposals opened for public comment, see “Your two cents.” The date shown is the date of publication or other official release.
“Your Two Cents”: This is your chance to provide input on rules and policies that will affect you. Agencies must provide the public notice and an opportunity for comment before their rules or policies change. Your input matters. Comments should be received before the indicated due date; however, agencies often consider comments they receive before drafting of the final document begins.
“Final Documents” and “Your Two Cents” are available at http://arsa.org/final-documents-your-two-cents/.
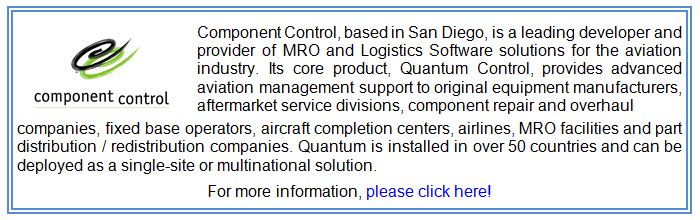
Quality Time
Editor’s note: The views and opinions expressed by contributing authors do not necessarily state or reflect those of ARSA, and shall not be used for endorsement purposes.
Legal Waypoints: Flow Down / Consequential Damages Case Study – Costa v. Brait
By Steven E. Pazar, attorney at Law, 11 Carriage House Lane, Boxford, Massachusetts 01921. © 2013 Steven E. Pazar ALL RIGHTS RESERVED.
Steven is a counselor to businesses operating in many industries, including aviation. He provides templates, tools and training to improve contracting efficiency, close deals faster and control costs.
A recent case decided by the Supreme Judicial Court of Massachusetts illustrates how a flow down provision can work in the context of a claim for consequential damages. The case of Costa v. Brait Builders Corporation, 463 Mass. 65, 972 N.E.2d 449, (Mass., 2012), involves several areas of dispute between a prime (general) contractor and one of his subcontractors on a municipal construction project. One of the lessons learned is a keen reminder of the power of simple flow down language and good contract review practices.
Background: In June 2004, Costa entered into a subcontract with Brait Builders Corporation to perform site work on a municipal construction project. The project consisted of earthwork such as digging trenches for underground utilities and diverting surface water. Work began on the project in mid-2004 but by early January 2005 the relationship between Costa and Brait was unraveling. Brait sent a threatening letter alleging Costa had left the work site under manned and unmanned. Costa replied alleging delay and added expenses caused by Brait. This was followed with more reciprocal accusations related to water accumulation and water removal from the work site. Shortly thereafter, Costa wrote advising Brait that site work would be discontinued due to extreme weather conditions. On the same day, Brait fired back announcing he was terminating the subcontract for unacceptable performance and barring Costa from the work site.
The Case: In May 2005, Costa filed suit against Brait alleging breach of the subcontract by obstructing performance, failing to pay amounts owed, and barring him from the work site. Some five years later (August 2010), the case went to trial. The jury returned a verdict in favor of Costa awarding general damages ($199,228), and consequential and incidental damages ($133,648) as well as statutory damages, attorney’s fees and interest, all totaling approximately $1,124,000. Both parties appealed the verdict for various reasons.
Consequential Damages: Prior to trial, Brait made a motion for a directed verdict arguing that consequential damages were precluded by a provision of its general contract with the municipality that was incorporated into the subcontract with Costa. The motion was denied. At the close of the trial, Brait moved for a judgment notwithstanding the verdict on a similar basis. That motion was also denied.
The first paragraph of the subcontract contained what was called an “incorporation by reference” clause. This clause stated that the terms of the general contract were expressly incorporated into the subcontract. In addition the subcontract also contained the following flow down provision:
“The Subcontractor agrees to be bound to the Contractor by the terms of the [general contract] and to assume to the Contractor all the obligations and responsibilities that the Contractor by those documents assumes to the awarding authority, except to the extent that provisions contained therein are by the terms or by law applicable only to the Contractor.”
A key provision of the general contract (between Brait and the municipality) stated the following:
“The Contractor waives Claims against the Owner for consequential damages arising out of or relating to this Contract. This includes: (1) damages incurred by the Contractor for … losses of financing, business and reputation, and for loss of profit except anticipated profit arising directly from the Work.”
The Appeal: On appeal Brait argued that the combination of these provisions working together act to preclude Costa’s claim for consequential damages. The Supreme Judicial Court of Massachusetts agreed, remanded the case and ordered the judgment be amended to strike the jury’s award of consequential damages. The court stated that “so-called ‘flow down’ clauses, pursuant to which the contractor’s obligations ‘flow down’ to the subcontractor, are an acceptable and common method for general contractors to limit risk.” In this instance the subcontract “unambiguously incorporates” the general contract, and the general contract “unambiguously precludes recovery of consequential damages”.
Employment Law & Repair Stations: Deadline is May 7, 2013 for New I-9 Employment Eligibility Verification Forms
By Jonathan W. Yarbrough, Constangy, Brooks & Smith, LLC, 80 Peachtree Rd., Ste. 208, Asheville, NC 28803-3160. © 2013 Jonathan W. Yarbrough ALL RIGHTS RESERVED
Jonathan is experienced representing employers in employment law issues; his pragmatic approach helps keep relationships with employees from becoming difficult. Please contact him for questions regarding employment relationships.
The United States Citizenship and Immigration Services (USCIS) has revised the I-9 Employment Eligibility Verification Form. All employers must complete the Form I-9 to verify employment eligibility for every new hire. The USCIS made the new I-9 forms available for use as of March 8, 2013. In order to accommodate employers who needed more time to make the necessary modifications, especially those who are using Electronic Form I-9, the agency extended the final date for implementation for 60 days. That deadline is now upon us.
The new forms can be accessed online by visiting the USCIS website at www.uscis.gov, or they can be ordered by calling 1-800-870-3676. A Spanish-language version of the new Form I-9 is also available at the USCIS website but may only be used in Puerto Rico. Note: Employers do not need to complete the new form I-9 for current employees for whom there is already a properly completed form on file, unless re-verification is necessary. In fact, unnecessary verification may violate section 274B of the Immigration and Naturalization Act, which prohibits discrimination.
The USCIS has expanded the new I-9 form to three pages with a revised layout. Instructions for completion are more detailed and include what are intended to be clearer explanations of the specific information required. There are new data fields to collect the employee’s email address and telephone number as well as the foreign passport number and country of issuance if the employee uses their I-94 and foreign passport as authorization to work.
As with the old Form I-9, the revised form contains three sections. Section 1 collects identifying information about the employee and requires the employer to attest to whether the employee is a U.S. citizen, noncitizen national, lawful permanent resident, or alien authorized to work in the United States. The employee is required to provide the employer with documentation evidencing his or her identity and authorization to work in the particular employment.
The purpose of Section 2 of the form is to collect identifying information about the employer as well as the identity and authorization that the employee has presented in Section 1 and which the employer has reviewed. This section must be provided within three business days of the employee’s hire.
Section 3 of the I-9 form collects information with respect to the employee’s continued employment authorization. The section is completed when either Section 1 or Section 2 of the form expires, or if the employee is rehired within three years from the date the original form was executed. The information in this section could include a name change if completing this Section 3 is otherwise required.
Employers must retain the Form I-9 for three years after the hire date or for one year after the date employment ended, whichever is later. It must also be made available for inspection by the U.S. Immigration and Customs Enforcement (ICE), the Department of Justice (DOJ) and the Department of Labor (DOL).
As of May 7, 2013, employers should be using Form I-9 with a revision date of “(Rev. 03/08/13)N.”
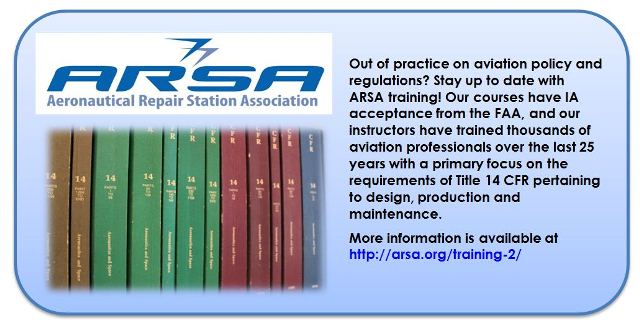
Membership
Member Spotlight: Barfield Inc., Miami, Fla.
On April 5, Barfield Inc. hosted ARSA Executive Vice President Christian Klein for an industry briefing of dozens of aviation maintenance professionals from around the Miami area.
A longtime supporter of ARSA and an active member, Barfield makes certain to get the most out of its association membership.
“Barfield is proud to be part of ARSA and was more than happy to host the Miami-Outreach,” said Barfield Vice President of Quality Robert Arnett. “For those who were not able to attend the recent Symposium and Legislative Day, it gave the opportunity to communicate some of the current issues ARSA is working on that affect many of us in the industry. ARSA has also been very instrumental in assisting us with my fight against the ban on foreign repair stations. Their courteous and knowledgeable staff has proven to be a very valuable asset.”
Founded in 1945 by James W. Barfield and acquired by Sabena Technics in 2007, Barfield Inc. has served the aviation industry for more than 65 years. Barfield has complete capabilities to test, repair, and/or overhaul avionics, instrument, and electronic components in excess of 25,000 part numbers that span all aircraft markets, including commercial, corporate, regional helicopters, and general aviation. It serves as an authorized warranty repair station for 15 European and three U.S. original equipment manufacturers (OEMs), as well as six ground support OEMs.
For more information, visit www.barfieldinc.com
Are you an ARSA member who would like to be in the “Member Spotlight?” If so, please contact Jess Hammett at jess.hammett@arsa.org.
Have You Seen This Person?
Each month, the hotline spotlights key regulatory, legislative, and business leaders making important contributions to the aviation industry. This month we look at Peggy Gilligan, associate administrator for aviation safety for the Federal Aviation Administration (FAA).
Peggy Gilligan became associate administrator for aviation safety on January 5, 2009, after serving as the FAA’s deputy associate administrator for 14 years. She has been with the agency since 1980.
In October 2011, Peggy accepted the Roger W. Jones Award for Executive Leadership. American University’s School of Public Affairs annually grants this award to two federal senior executives who have shown exceptional leadership while devoting themselves to a career of public service.
In May 2009, Peggy and her industry co-chair accepted the Robert J. Collier Trophy in recognition of the Commercial Aviation Safety Team’s (CAST) work in developing an integrated data-driven strategy that reduced aviation fatalities in the United States by 83 percent over 10 years. Peggy serves as the government co-chair of CAST — a joint industry/government group committed to improving aviation safety by reducing the risk of accidents.
In April 2006, Peggy and her industry co-chair received the Laurel Award from Aviation Week & Space Technology magazine for improving aviation safety and “reducing the risk of fatalities in world aviation” through CAST. The annual award recognizes the extraordinary accomplishments of individuals and teams in aviation, aerospace, and defense.
Peggy was chief of staff at the FAA, serving four administrators. She also served in the chief counsel’s office in Washington and as a staff attorney in the FAA’s eastern region in New York. Peggy is a 1979 graduate of Boston University School of Law and a 1975 graduate of Manhattanville College, Purchase, NY. She resides in Washington, DC.
A Member Asked…
Q: We are planning to perform work on components for the U.S. military and issue FAA 8130-3 tags when we are finished. The articles are identical to components we repair for civilian customers who operate the commercial version of the aircraft, and we will use the same manufacturer instructions to perform maintenance. However, our FAA inspector says we cannot issue an 8130-3 if the components are shipped to the U.S. military. Is this correct?
A: No, even though the FAA may not have jurisdiction over the work performed for the military that does not prevent the repair station from performing maintenance in accordance with part 43 and issuing an 8130-3. Indeed, the part could eventually be transferred onto a civilian aircraft of the same type. Last month, the FAA issued guidance covering this topic in Order 8900.1, volume 8, chapter 7, section 1 (link) that provides in pertinent part: “No current regulation prohibits a maintenance provider from completing an airworthiness release, or from completing any other form to record activities that the FAA regulates, or that falls under FAA jurisdiction. Additionally, when a maintenance provider approves work on an article for RTS [return to service] using its FAA certificate number, and that article gets installed on an aircraft not identified in § 43.1 , the certificate holder doesn’t bring itself under the FAA’s enforcement jurisdiction for that maintenance. However, if the article gets installed on an aircraft identified in § 43.1, the maintenance provider is subject to the FAA’s enforcement jurisdiction for that maintenance…”
Get 10% off on membership dues by utilizing ARSA’s Members getting members program
The best form of advertising is word of mouth. Use the Members Getting Members Toolkit to recruit an ARSA member and your company will receive a discounted membership rate for your next membership term. Get more information at http://arsa.org/membership/members-getting-members/
Advertise Today in ARSA’s Newsletters and Website!
ARSA recently updated its menu of advertising opportunities for arsa.org, the hotline and the ARSA Dispatch. Take advantage of these great opportunities today to showcase your company, a new product or event. For more information go to http://arsa.org/advertise/
Interested in exhibiting or sponsoring the 2014 Repair Symposium?
As the maintenance industry’s top event devoted exclusively to regulatory compliance, the ARSA Symposium attracts a highly qualified professional audience. Use this opportunity to promote your company while showing support for ARSA. Get more information at http://arsa.org/news-media/events/arsa-annual-repair-symposium-sponsorship/
Industry News
Blue Ridge CC’s Dyen Awarded Instructor of the Year
On April 15, Blue Ridge Community College Aviation Maintenance Technology Program Associate Professor Fred Dyen was awarded the Ivan D. Livi Aviation Maintenance Educator of the Year Award presented at the annual Aviation Technician Education Council (ATEC) Conference. The award recognizes long-term outstanding performance of an aviation maintenance technology instructor who has had a direct impact on students. Read more at http://arsa.org/blue-ridge-ccs-dyen-awarded-instructor-of-the-year/
International News
Malaysian MRO Industry Emerging as Regional Leader
This year, Malaysia’s aviation maintenance industry is poised to emerge as one of the Asia-Pacific region’s leading airframe and engine overhaul markets.
According to the Malaysian Investment Development Authority, the government agency tasked with promoting the development of the manufacturing and services sectors in Malaysia, the island nation’s $900 million MRO industry is expected to grow by an astounding ten percent this year.
The third largest MRO market in the region after Singapore and Hong Kong, Malaysia is looking to attract foreign investors to its aviation industry, particularly the aviation maintenance segment. This year alone, the country hopes to double its funding for the aviation industry to nearly $1.5 billion, more than a third of which is derived from foreign entities.
Welcome New Members
● A&R Aviation Services, Inc., Tumwater, WA
● David Hall, Jacksonville, AR
● Falcon Crest Accessories, Houston, TX
● Icon Aerospace LLC, Monroe, NC
● Master Air Parts, Inc., Santa Maria, CA
● Sargent Aerospace and Defense, Miami, FL
● Skytech Aviation, Inc., Oakland Park, FL
Regulatory Compliance Training
Click here to test your knowledge on §145.3 Definition of terms, the part that describes how to obtain a repair station certificate.
Upcoming Events
RAA 38th Annual Convention – May 6-9, 2013 — Montreal, Quebec – ARSA Executive Director Sarah MacLeod to moderate session entitled, “Maintenance Issues,” on May 8th at 4pm.
AMROI – May 22-23, 2013 – Jakarta, Indonesia – ARSA Executive Director Sarah MacLeod to address audience during panel discussion entitled, “International Perspective: Strengthening bilateral cooperation in aviation safety and maintenance regulations,” on May 22nd at 10am.
Previous 12 issues:
2013: | Jan | Feb | Mar | ||||||
2012: | Apr | May | Jun | Jul | Aug | Sep | Oct | Nov | Dec |
the hotline is the monthly publication of the Aeronautical Repair Station Association (ARSA), the not-for-profit international trade association for certificated repair stations. It is for the exclusive use of ARSA members and federal employees on the ARSA mailing list. For a membership application, please call 703 739 9543 or visit http://arsa.org/membership/join/
This material is provided for educational and informational purposes only. It does not constitute legal, consulting, tax or any other type of professional advice.
Law, regulations, guidance and government policies change frequently. While ARSA updates this material, we do not guarantee its accuracy. In addition, the application of this material to a particular situation is always dependent on the facts and circumstances involved. The use of this material is therefore at your own risk.
All content in the hotline, except where indicated otherwise, is the property of ARSA. This content may not be reproduced, distributed or displayed, nor may derivatives or presentations be created from it in whole or in part, in any manner without the prior written consent of ARSA.
ARSA grants its members a non-exclusive license to reproduce the content of the hotline. Employees of member organizations are the only parties authorized to receive a duplicate of the hotline.
ARSA reserves all remaining rights and will use any means necessary to protect its intellectual property.
© 2013 Aeronautical Repair Station Association