2017 – Edition 11 – December 8
Table of Contents
Note: The order of material varies in hotline emails, but is always presented the same on this landing page. Readers scrolling through content on or printing this page will find it organized consistent with the table of contents.
Christian’s Corner
Symposium 2018
ARSA Works
Legal Briefs
ARSA on the Hill
Quality Time
Training
Membership
Resources
Industry Calendar
Christian’s Corner
For ARSA’s Health and Your ROI, Get Active in 2018
By Christian A. Klein, Executive Vice President
As an ARSA member, your company supports the association’s zealous advocacy for the international aviation maintenance industry, which results in a better regulatory and business environment for repair stations. Paying member dues is only the first step.
If all you’re doing is paying dues and reading the hotline each month, you’re not taking full advantage of ARSA’s resources…nor are you maximizing the return on your ARSA investment.
Let’s make 2018 the year you take full advantage of your basic investment and determine how to increase that commitment and enhance your return:
(1) Attend the 2018 ARSA Symposium … and bring your next generation of talent along.
Held in March of each year, the symposium is ARSA’s flagship event. It’s the best forum to learn about regulatory developments, share best practices, network and engaged in collective action. The symposium includes a day and half of regulatory content with presentations by FAA and other international regulators, a full day of lobbying on Capitol Hill and (new this year) a day of meetings for industry executives with top administration officials.
If you’re a regular symposium attendee, budget to bring additional team members. If you’ve never been but others from your facility attend, see how to get onboard. The event needs to be part of your company’s professional development plan; the growing challenge of developing and retaining talented personnel makes it vital to get the next generation of industry leaders to the symposium.
The 2018 Annual Repair Symposium, including Legislative Day and the new Executive to Executive (E2E) Breifings, will be held from March 13-16, 2018 in Arlington, Virginia (and Washington, D.C.). To learn more, visit: arsa.org/news-media/events/arsa-symposium.
(2) Make ARSA part of your company’s 2018 training strategy.
Did you know that ARSA has a library of more than 60 on-demand training sessions on a wide range of topics including instructions for continued airworthiness, part 145, international compliance, surviving audits and much, much more? Sessions are led by the association’s regulatory experts and available online and on-demand so you and your team members can view them whenever it’s most convenient (even on a smart phone). The system administers multiple-choice tests and issues certificates for session completion. The program will continue to grow in 2018 and beyond, with ARSA’s team adding new courses and rolling out a fully-updated human factors training program.
At $75 per hour and with bulk-purchase discounts available, the association’s training is an affordable way to “stay smart, safe and out of trouble”. As you’re designing your 2018 training plan and budget, remember that ARSA helps meet obligations while significantly reducing cost. (Contact Brett Levanto at brett.levanto@arsa.org for information about training sessions and options for up-front purchase of bulk “subscriptions.”)
To learn more, visit: arsa.org/training.
(3) Use ARSA publications to improve compliance.
Whether you’ve been in business for years or are a new entrant into the aviation maintenance marketplace, ARSA publications are an outstanding resource. The association provides model manuals, supplements, forms and other materials to help ensure regulatory compliance. In order to provide access to a higher-level of service, the association is working with its management firm Obadal, Filler, MacLeod & Klein, P.L.C. to advise certificate holders or applicants and customize publications to fit specific needs (stay tuned). A complete curriculum on how to become a certificated repair station will also become part of the association’s training program.
Whether you’re in need of a tune-up or your manuals require a complete overhaul, take advantage of the resources ARSA provides.
To learn more, visit: arsa.org/publications.
(4) Leverage ARSA’s resources to build your influence.
ARSA’s regulatory and legislative advocacy for the industry has saved repair stations untold thousands of dollars and, in some cases, kept members in business. By leveraging the association’s advocacy expertise, you and your company can become more politically influential, support ARSA’s work and ensure your company stays ahead of trends and problems.
Symposium week – which was celebrated in (1) above – provides opportunities to get actively engaged:
Legislative Day participants spend time on Capitol Hill with other ARSA members educating members of Congress and congressional staff. With FAA funding set to expire at the end of March, the timing is perfect to build momentum for ARSA-supported workforce and regulatory provisions in the reauthorization bill.
Executive Forum, which ARSA is connecting with its spring meeting for the first time, will give senior leaders from international aviation maintenance companies a chance to engage with the executive branch. In meetings with appointed and career officials from government agencies, participants will connect the dots between what is said on Capitol Hill and what is being done (or contemplated) by the federal workforce.
ARSA is proud of the industry-leading companies that compose its membership and grateful for their support and confidence. For the health of the association and your own return on investment, it’s time to get active and there is no time like the present.
Symposium 2018
Plan Now for ARSA’s Premier Event (It’s Growing)
Registration will open in January for the 2018 Annual Repair Symposium, which will be held from March 13-16, 2018 in the nation’s capital alongside ARSA’s Legislative Day and (the new) Executive to Executive (E2E) Briefings.
As in past years, the main Symposium program – with all the great regulatory and industry content participants have come to expect – will take place on Thursday and Friday (March 15 & 16) with Legislative Day on Wednesday (March 14). To make the conference even more valuable, this year ARSA is adding a day of meetings on Tuesday (March 13) with executive branch officials for C-level executives.
The Symposium isn’t just a great opportunity to learn and network with aviation colleagues, it’s also an excellent opportunity to raise your company’s visibility in the industry and get the word out about your products and services. ARSA offers four levels of sponsorship: Platinum ($10,000), Gold ($7,500), Silver ($3500), and supporter. All sponsorship levels give visibility in event materials and considerable exposure. Companies bringing multiple team members should consider Platinum or Gold sponsorship, which provides free registrations, the opportunity to have your name associated with a specific part of the program and access to the exclusive E2E Briefings.
As part of ARSA’s commitment to developing the next generation of repair station leadership, it is encouraging attendees to bring other members of their team – particularly younger engineers and technicians – to help them tap into all the value and resources the association provides.
With the FAA bill poised to be front and center as ARSA members take to the Hill for Legislative Day, this will also be a critical time to make the industry’s presence felt on the political stage. The association hopes more members than ever before will answer the call to action and make this industry’s voice heard on the Hill.
As ARSA’s team continues to refine the agenda for the meeting, it is putting out the call for members interested in participating in panel discussions throughout the conference. Here are some of topics being considered and questions panelists can help answer:
New technologies for aviation maintenance.
New technologies to enhance efficiencies are coming on line every day. How is your company taking advantage of these rapid changes? Are you using 3D printing, augmented reality, live video streaming, unmanned aircraft systems, or other new and innovative technologies in your maintenance and manufacturing? What technologies are you using to manage your data? What regulatory issues or hurdles have you had to overcome as you incorporate innovative technologies?
Bridging the generation gap.
ARSA members spend considerable time, energy, and money recruiting the next generation workforce. What are your recruitment strategies? What are you doing to develop, train and retain that talent once you’ve got the right people in the jobs? How do you transfer knowledge and corporate culture? Does your company use in-house mentoring? How do you create opportunities for internal advancement and professional growth?
Doing business with government.
More and more ARSA members are providing goods and services to government … or want to. Is your company doing business with the Department of Defense (DoD) or some other part of the federal government? What about state and local entities (air national guard, police, emergency management, etc.)? Are you exploring opportunities in these areas? What challenges have you encountered (either serving these customers or identifying where to start)? How did you solve them? Where do you see opportunities for growth? Have you applied to DoD for Source Approval Request for PMA parts or DER repairs? If so, what was your experience with the process? What DoD policies make life difficult for contractors and what can ARSA do to create a better environment for small companies doing business with the military or other parts of the government?
Doing business internationally.
The maintenance industry is inherently global and serving international customers is an important line of business for many repair stations. Balancing competing – and sometime contradictory – regulatory requirements will always be a challenge, but what other problems have you encountered and how have you addressed them? What issues have you encountered importing customer parts into the country for repair? How do you find and develop your international customer base? How do manage a global workforce? How do you manage competing regulatory obligations? What legal or cultural issues have arisen doing business overseas? What government resources have you used to help facilitate your international growth?
Planning for success.
The most successful companies don’t just do what they do well, they think about and plan for future opportunities and challenges. What does your company do to keep its finger on the pulse of industry commercial and business trends? How do you incorporate that information into your medium- and long-term business plans? How does your company plan for succession?
The drones are coming!
Drones are becoming commonplace in a variety of industries. Because drones over 55 pounds must have an airworthiness certificate and be maintained under part 43, repair stations are well-positioned to service the drone maintenance market. Does your company service drones? Do you plan to in the future? How big of a maintenance market will drones become? Given that drones are often operated by companies not familiar with aviation regulations, what challenges have you encountered in tapping into this new customer base?
Those are just some of the topics we’re considering for this year’s Symposium in addition to all the great regulatory content related to maintenance and manufacturing. If you’re interested in participating on panels on any of the foregoing topics, shoot an email to brett.levanto@arsa.org. And feel free to suggest other panel topics you think would be of interest to your industry colleagues.
Click here to visit the event page to see the agenda, learn about sponsorship opportunities and plan for your attendance now.
ARSA Works
ARSA’s Filler Continues European Regulatory Engagement
On Nov. 30 Managing Director & General Counsel Marshall S. Filler represented ARSA at the first meeting of EASA’s Engineering & Maintenance Technical Committee, the successor group to the E&M Stakeholder’s Technical Body (STeB).
In 2015, EASA’s management board approved a restructuring of the way industry advises the agency in matters under its jurisdiction. Under the new structure the Stakeholder’s Advisory Body (SAB Plenary) will now oversee five Committees (Commercial Aeroplane Safety, General Aviation, Rotorcraft Strategy, Drones Strategy and Certification Strategy) and five Technical Committees (Flight Standards, Design and Manufacturing, Engineering and Maintenance, Aerodromes and Air Traffic Management and Air Navigation). The Committees typically meet twice each year.
Similar in concept to the FAA’s Aviation Rulemaking Advisory Committee (ARAC) the current SAB structure is intended to improve coordination among EASA management and the various government and industry advisory bodies and committees while promoting awareness, transparency and balanced representation by industry stakeholders.
During the first meeting of the EM.TEC, members elected Ric Peri of the Aircraft Electronics Association – Europe as its Chair and Erik Moyson of the International Air Carrier Association as the Co-Chair. Both individuals will serve a 30-month term (presumably both will receive time off for good behavior). Members of the various SAB committees were required to sign a document acknowledging the Code of Conduct for outside experts supporting EASA, which among other things, prohibits the release of information about the committee’s deliberations unless the data has previously been made public.
Within that constraint, ARSA can report that the EM.TEC discussed several issues of interest to ARSA’s members in the EU and other AMOs outside the U.S. that are subject to EASA Part-145. Committee members also received briefings on EASA’s latest cyber-security efforts, the status of the agency’s bilateral agreements with the U.S., Canada, Brazil, China and Japan and an update on the status of various EASA rulemaking tasks (RMT), including RMT.0018 relating to parts documentation. ARSA members in the United States. will be interested to know that EASA and the FAA are continuing their work to resolve the remaining parts documentation issues in the Maintenance Annex Guidance (MAG).
ARSA to White House: Government Should Trust Its Own Aviation Safety Approvals
On Nov. 17, ARSA submitted a document to the White House identifying an important opportunity for the Department of Defense (DoD) to enhance efficiency and reduce costs related to maintaining its fleet of commercial derivative aircraft (CDA). The association’s white paper was sent to White House Director of Policy and Interagency Coordination Carlos Diaz-Rosillo as a follow-up to discussions with maintenance industry leaders during the 2017 ARSA Strategic Leadership Conference executive branch briefing.
ARSA’s position is the FAA, through its civil aviation oversight, already determines whether Parts Manufacturer Approval (PMA) parts and Designated Engineering Representative (DER) repairs are compliant and fit for use on the aircraft from which CDA are derived. Forcing previously-approved parts and repairs to go through the cumbersome SAR process costs government resources and wastes taxpayers’ money while ignoring the civil aviation sector’s outstanding safety and reliability record. Since SARs are rarely granted, DoD is not benefiting from the cost savings associated with PMA parts and DER repairs.
“By law, DoD has broad authority to make airworthiness determinations in any manner it chooses,” the submission said, citing Title 10 of the U.S. Code and a template from the Defense Logistics Agency. “Unfortunately, this department has translated this authority into an extraordinarily burdensome series of policies and instructions that require aircraft parts manufacturers and maintenance contractors – including those with Commercial Off-the-Shelf (COTS) solutions already approved for use in civil aviation by the FAA – to go through a redundant, expensive, slow and burdensome SAR process to gain DoD approval.”
ARSA recommended the government revise its policies to trust its own aviation safety agency, the FAA. The association urged the White House to work with DoD to recognize “any approval issued by the FAA for a product, material, part, component, process or appliance as eligible for use on a CDA.”
To read the full ARSA submission, click here. To get some deeper discussion of how the DoD can help itself by learning from the FAA, check out the “Legal Brief” in this edition of the hotline.
For more information regarding ARSA’s support for its members with military business, contact Executive Vice President Christian A. Klein (christian.klein@arsa.org).
ARSA Works with Quadrilateral Group Towards “Practical Compliance”
On Nov. 9 and 10, the quadrilateral Maintenance Management Team (MMT), which is comprised of the FAA, Transport Canada, EASA and Brazil’s ANAC, met in Ottawa to discuss issues affecting existing bilateral maintenance agreements. The MMT is similar to the almost 10-year-old Certification Management Team (CMT), and the four authorities used this first official meeting to present governance plans including annual meetings and associated industry days. The group’s official charter will likely be finalized by the end of the year.
In preparation for the event, ARSA worked with several other industry trade associations to develop and execute the agenda for the Nov. 10 industry day:
Industry Day – Nov. 10 – Review
Participants were briefed on ICAO’s efforts to minimize duplication associated with the certification and surveillance (i.e., audits) of Approved Maintenance Organizations (AMOs). As most ARSA members know, most States of Registry require their own AMO certificates instead of approving or accepting those issued by other authorities. Although ICAO’s efforts will not affect the State of Registry’s authority over continued airworthiness it will, by developing more robust AMO guidance, encourage States to strongly consider approving or accepting the certificates issued by other authorities or, at the very least, rely on audits performed by other civil aviation authorities. This is clearly a step in the right direction although the results of the effort will not be known for many years.
Not surprisingly, parts documentation was discussed again – the participating groups (except for Transport Canada) addressed this topic during an unofficial meeting in June 2016 under the auspices of the FAA-EASA Joint Maintenance Coordination Board after the agencies’ International Safety Conference – including commercial and commercial off-the-shelf parts (COTS) parts and the current requirement in the Maintenance Annex Guidance (MAG) that they be accompanied by a Form 1 or 8130-3 when installed in maintenance subject to that agreement. Although EASA will soon issue a Notice of Proposed Amendment (NPA) to reduce the number of parts that will require Form 1 (perhaps setting the stage for subsequent MAG changes), the rulemaking process will take more time and is fraught with uncertainty.
In the meantime, industry reminded the two agencies that certificate holders have no practical compliance path because the vast majority of commercial and COTS parts are not traceable to a production approval holder and consequently are not accompanied by Form 1 or 8130-3 as required by the MAG (except for standard and fabricated parts). An ARSA-led industry coalition recommended a solution earlier this year (i.e., that the parts not require a Form 1 or 8130-3 if they are traceable to an approved design; a C of C would suffice). Unfortunately, the issue remains open although discussions between the two authorities are continuing.
More progress was made in the area of parts documentation associated with single releases for maintenance performed on aircraft. The issue is whether parts installed on a U.S.-registered aircraft in the European Union must have Form 8130-3 if only a single release is to be issued, which is normally the case for aircraft maintenance. Such parts should not require Form 8130-3, although the MAG states otherwise. ARSA is hopeful this will be addressed in MAG change 7.
Finally, Transport Canada is working to develop guidelines to accept work performed by appropriately-certificated maintenance facilities outside the geographical borders of the United States or Canada (or another country that does not have a maintenance agreement with Canada). The theory is that if Transport Canada or the FAA would accept work from an appropriately certificated organization inside the United States or Canada, why would they not recognize the same maintenance when performed by an FAA or TCCA certificate holder outside either country? The problem arises due to the geographic limitations inherent in most bilateral agreements although there are ways to address it if the authorities are willing to do so. The FAA and EASA have issued numerous “foreign” AMO certificates compared to a much smaller number for Canada and Brazil. If a maintenance facility in Mexico, for example, held an EASA Part-145 certificate but wanted to work on U.S. State of Registry articles, the FAA would require that it obtain an FAA foreign repair station certificate instead of recognizing its EASA certificate. EASA would do the same. Perhaps the two authorities should rethink this.
Industry is hoping the MMT will lead by example and eventually adopt mutual recognition of each other’s maintenance certificates without special conditions. It would set a positive example for the rest of the world and would not adversely affect the industry’s excellent safety record.
The next MMT meeting will be in Brazil in October 2018 in an as-yet undisclosed location – the most likely candidates are Sao Paulo or Brasilia.
ARSA Adds to Quality Discussion at Airline Workforce Forum
On Nov. 7 and 8, Airlines for America (A4A) hosted its second annual AMT Career Forum at JetBlue headquarters in Long Island City, New York. ARSA Vice President of Communications Brett Levanto joined the group to help add “the repair station perspective.”
The agenda included a series of roundtable discussion on marketing, recruitment, regulatory oversight and educational programs. Participants representing A4A’s member airlines, the FAA, New York-area aerospace training programs, maintenance providers and several aviation trade associations explored the reality of finding and retaining technically-capable mechanics.
While many publications – including ARSA’s 2017 member survey report – have carefully reported the shortage of qualified technicians, forum participants took the next step in the discussion by focusing on the quality of available talent in addition to the quantity of applicants.
“If we’re going to change the shape of curve, [the broad aviation community’s] resources need to get plugged into this effort,” said A4A Managing Director of Engineering and Maintenance Bob Ireland, describing the increasingly dire need for maintenance shops to reverse recent workforce trends. At every break in the agenda, Ireland – who organized the event – reinforced that attendees were expected to turn valid discussion into valuable action.
Levanto joined Jim Sokol, HAECO Americas president of MRO services, to review the workforce realities of FAA-certificated repair stations. They discussed business management, regulatory requirements, onboarding time and the balance of A&P mechanics, repairmen and non-certificate-holding technicians. The group reviewed data from two of ARSA’s workforce-related “quick questions” as well association-proposed amendments to the House and Senate bills to reauthorize the FAA.
“This is a great venue for an important discussion,” Levanto said. “Last year [at the inaugural forum, hosted at A4A’s headquarters in Washington, D.C.] I thought we had a great group, but you could feel us gain momentum this week: Everyone was actively engaged, candid and open to learning about what’s really going on in the maintenance workforce. We just can’t work anymore without this kind of proactive interaction.”
For information about Levanto’s presentation or general support for workforce development initiatives, contact him at brett.levanto@arsa.org.
Final Documents/Your Two Cents
This list includes Federal Register publications, such as final rules, Advisory Circulars and policy statements, as well as proposed rules and policies of interest to ARSA members.
Legal Briefs
Editor’s note: This material is provided as a service to association members for educational and informational purposes only. It does not constitute legal or professional advice and is not privileged or confidential.
Educating in Efficiency: Teaching DoD About Civil Aviation Safety
By Christian A. Klein, Executive Vice President
On Nov. 17, ARSA submitted a document to the White House identifying an important opportunity for the Department of Defense (DoD) to enhance efficiency and reduce costs related to maintaining its fleet of commercial derivative aircraft (CDA). The white paper provided the Trump administration a prime opportunity to improve government efficiency through DoD’s Source Approval Request (SAR) process. By some estimates, the federal government could save tens of billions of dollars by eliminating the duplicative SAR process for third-party parts and repairs used to support DoD’s fleet of Commercial Derivative Aircraft (CDA).
You can see what ARSA said in the “ARSA Works” section of this edition of the hotline, here’s some deeper insight into how these pieces can fit together.
Parts Manufacturer Approval (PMA) for civil aviation replacement and modification articles and Designated Engineering Representative (DER)-approved maintenance and alteration processes are the methods by which FAA determines compliance and fitness for use on civil aviation aircraft, including those from which CDA are derived.
By law, DoD has broad authority to make airworthiness determinations in any manner it chooses.[1] Unfortunately, the department has translated this authority into an extraordinarily burdensome series of policies and instructions that require aircraft parts manufacturers and maintenance contractors – including those with Commercial Off-the-Shelf (COTS) solutions already approved for use in civil aviation by the FAA – to go through a redundant, expensive, slow and burdensome SAR process to gain DoD approval.
As a result of this redundant burden, the DoD is not taking advantage of cost savings associated with FAA-approved parts and repairs which are proven to provide an equivalent or better level of safety and reliability.
Accepting FAA Approvals Will Improve DoD Safety, Efficiency and Readiness
Existing FAA certification processes are equivalent to, and in many cases better than, parallel DoD standards and specifications. For example, many of the FAA certification processes allow for input from industry committees and standards groups, allowing safety and performance improvements to be more easily incorporated.
ARSA members that have applied for SARs indicate that, although allowed by DoD policy and regulations, SARs based upon reverse-engineering or any other non-Original Equipment Manufacturer data are not granted. Most DOD program offices will apparently not even consider such SAR applications. As a result, DoD has limited its ability to take advantage of FAA-approved solutions, even though the department requires initial certification of its derivative aircraft from the FAA.
This is an example of government inefficiency. The FAA’s regulatory framework ensures the safety of U.S.-registered aircraft operating worldwide. Together, the FAA and America’s civil aviation sector have forged an outstanding and unprecedented safety record. Commercial air carriers also have an enviable reliability record. According to the Department of Transportation, in 2016 just 1.17 percent of flights were cancelled and in December 2016, “only 6.59 percent [of flights were delayed] by factors within the airline’s control, such as maintenance or crew problems.” By comparison, according to an April 2017 Air Force Times article, “[m]ission-capable rates — the metric by which the Air Force measures how much of its fleet can fight or fly other missions at any given time — are trending downward, slowly but steadily. In [FY] 2014, mission-capable rates for all of the Air Force’s airplanes and helicopters were just shy of 74 percent. One year later, that rate had dropped to 73 percent. It fell even further in 2016, to about 72 percent.”
Accepting FAA Approvals Can Save DoD – and Taxpayers – Tens of Billions of Dollars
Rand’s National Defense Research Institute (NDRI) recently explored ways DoD could reduce operating and support costs without affecting safety or reliability by making increased use of PMA parts and DER repairs on CDA engines. In the case of the F103 engine used on the KC-10 aircraft (civilian DC-10), NDRI estimated savings at roughly 20 to 25 percent – more than $1 million – per overhaul, an average of $50 million per year. The institute estimated that making greater use of commercial refurbished parts or of PMA parts and DER repairs for commercial-derivative military engines could save the DoD more than $80 million annually. It is important to note that NDRI’s report only examined engines; there are similar opportunities to save money in every other aviation maintenance area.
A similar study by the Institute of Defense Analysis (IDA) on the use of FAA maintenance data for DoD CDA cited estimates of “tens of billions” in savings annually to DoD if it followed commercial practices on systems derived from commercial aircraft. While stating that it had not independently estimated potential savings, IDA found that “significant savings are plausible.”
With all the foregoing potential safety, efficiency, readiness, and cost benefits, it seems logical that DoD should revise its applicable regulations and policies to recognize any approval issued by the FAA for a product, material, part, component, process or appliance as eligible for use on a CDA.
What Do You Think?
As ARSA explores this issue further, we welcome input from members. What experience have you had with the SAR process? Has your company had source approval requests approved? If so, how efficient was the process? How could it be improved? If you SAR was not approved or hit a dead end, what went wrong? Did the DoD analyze your request in detail, reject it out of hand, or simply fail to act? Send your comments to me at christian.klein@arsa.org.
ARSA on the Hill
Is Now the Winter of Our Legislative Discontent?
By Christian A. Klein, Executive Vice President
It’s an unusually busy winter on Capitol Hill and a lot has to happen before lawmakers leave town for the holidays.
Although tax reform has hogged the spotlight (more on that later) the top priority is keeping the government’s doors open and lights on. The current continuing appropriations resolution funding federal operations expires on Dec, 8 (Editor’s note: Since the hotline went to press just before this deadline, you may be able to find out exactly what did happen as you read this). If Congress fails to agree to a new spending plan for the rest of fiscal year 2018 (which began in October), the government could shut down. Although air traffic control and TSA security at airports are considered “essential” and wouldn’t be affected, many FAA employees would be furloughed, causing headaches and delays for the aviation industry at large.
Although possible, it’s hard to imagine that a shutdown will occur given that Republicans control both Congress and the White House. However, the fact that the spending bill would have to overcome a potential filibuster by Senate Democrats gives them leverage in the negotiations. One major sticking point for Democrats includes resolving the immigration status of so-called “dreamers”, brought to the country illegally as children and granted special protections during the Obama administration. Trump has said he’ll end the Dreamer program if Congress fails to act. One potential compromise in the appropriations package is giving Dreamers lawful permanent status in exchange for more border security funds, a top Trump priority.
A Taxing Debate
Tax reform has been the major focus on Capitol Hill for some weeks. Republicans scored a major victory on Dec. 2 with narrow Senate passage of a massive tax cut bill. The House passed its version last month. The focus now is on a House-Senate conference to reconcile the two versions and come up with something will pass muster with House conservatives and be able to win the support of at least 50 Republican senators.
Because the bill is proceeding under special budget rules, the bill can’t be filibustered by Democrats and only a simple majority is necessary to pass it. Vice President Pence could cast the tie-breaking vote if two Senate Republicans decides to jump ship. Given the spectrum of opinions among Senate Republicans and lingering concerns about the bill’s impact on the national debt, a deal and final passage are still far from certain.
What’s in the Bill?
While the business community broadly supports the concept of tax reform, there’s considerable ambivalence among groups in Washington, D.C. about the bills currently under consideration. The 20 percent corporate tax rate established by both bills and changes to tax rules for companies operating internationally would be very positive changes, but other things that are – and aren’t – in the bills are causing heartburn. For example, the Senate tax bill would maintain the corporate alternative minimum tax (AMT), which could limit corporations’ ability to take advantage of various tax breaks. Transportation and construction interests are grumbling that the bill doesn’t include new taxes to support infrastructure investment and, in fact, takes a step backwards by eliminating tax-exempt private activity bonds that help build, among other things, airports.
There’s also frustration that although a long-stated goal for tax reform is to restore certainty to the tax code, many of the provisions expire in a few years (a trick to reduce the bill’s long-term cost and keep within budget parameters). For example, the bills greatly expand business expensing, but those changes aren’t permanent and both versions eliminate the business interest deduction for larger companies. The legislation also changes rules relating to the deductibility of research and development costs and eliminates the domestic production deduction.
Aircraft Management Service Payments Exemption from Excise Tax
One provision of the Senate bill of potential interest to some ARSA members would clarify that certain payments to aircraft management companies by aircraft owners are exempt from the air transportation excise tax.
To make a long story short, the federal government imposes an excise tax on domestic air transportation. The tax has two parts: 7.5 percent on amount paid for the transportation services and a flat dollar amount for each combined takeoff and landing. Whether payments by aircraft owners to management services companies are subject to the air transportation excise tax has been a matter of dispute between industry and the IRS.
Aircraft management services companies are hired by aircraft owners to manage the asset. The services could include scheduling, flight planning, maintenance, and providing pilots and crew, and regulatory compliance. In such an arrangement, aircraft owners generally pay a base fee for the management services and an additional fee to cover the cost of actually using the aircraft for a flight.
The Senate bill would clarify that amounts paid by aircraft owners to management companies for maintenance and support are exempt from the excise tax. Specifically, according to the Joint Committee on Taxation,
Exempt payments are those amounts paid by an aircraft owner for management services related to maintenance and support of the owner’s aircraft or flights on the owner’s aircraft. Applicable services include support activities related to the aircraft itself, such as its storage, maintenance, and fueling, and those related to its operation, such as the hiring and training of pilots and crew, as well as administrative services such as scheduling, flight planning, weather forecasting, obtaining insurance, and establishing and complying with safety standards. Aircraft management services also include such other services as are necessary to support flights operated by an aircraft owner.
To read more about the provision, go to page 50 of the Joint Committee on Taxation’s description of the Senate tax bill.
Since the provision is not included in the House bill, its fate will be determined by House and Senate conferees hashing out the bill’s final details. We’re interested in hearing from ARSA members that provide management services that would be exempt under the new law. Send your comments to christian.klein@arsa.org.
What About the FAA bill?
With tax and appropriations bills sucking up all the bandwidth on the Hill, there’s been no movement on the FAA reauthorization bill. The current short-term extension of the legislation expires at the end of March (perfect timing for symposium). The House and Senate bill also contain important ARSA-backed provisions that would improve the regulatory environment for repair stations and address the maintenance industry technician shortage.
The bills have been held up in the House and Senate by different issues. The House bill would turn control of the nation’s air traffic control to a non-governmental entity, which air carriers support and the general and business aviation communities oppose. The Senate legislation contains language that would provide more flexibility for pilot training, which some key Senate Democrats oppose.
Given the press of other business, it’s highly unlikely an FAA bill will move in 2017. However, ARSA and other aviation groups are pushing to make it the top priority in early 2018. Plan to join us for ARSA’s Legislative Day on March 14th to help us move the ball forward.
So You Won’t Forget: FAA Bill Maintenance Amendments Box Score
ARSA Proposal | In House Bill | In Senate Bill |
Adding “aviation maintenance” to stakeholders on new Certification & Oversight Advisory Committee | Yes – Amendment by Rep. Hank Johnson (D-Ga.) and Rob Woodall (R-Ga.) adopted in committee by voice vote | Yes – Amendment by Sen. Jim Inhofe (R-Okla.) adopted in committee by voice vote |
Asking FAA to explore ways to enhance value of repairman certificates | No – Rep. Eddie Bernie Johnson (D-Texas) has filed amendment | Yes – Amendment by Sen. Jim Inhofe (R-Okla.) adopted in committee by voice vote |
Directing FAA to undertake rulemaking to reinstate voluntary surrender of repair station certificates | No – Rep. Dan Webster (R-Fla.) has filed amendment | Yes – Amendment by Sen. Jim Inhofe (R-Okla.) adopted in committee by voice vote |
Directing GAO to study causes, effects and solutions to aviation technician shortage | Yes – Amendment by Rep. Cheri Bustos (D-Ill.), Brenda Lawrence (D-Mich.) and Bruce Westerman (R-Ark.) adopted in committee by voice vote | No – ARSA is working to identify sponsor |
Creating grant program to support aviation maintenance workforce development initiatives | No – ARSA is working to identify sponsor | No – Sens. Jim Inhofe (R-Okla.) and Richard Blumenthal (D-Conn.) planning to sponsor amendment on Senate floor |
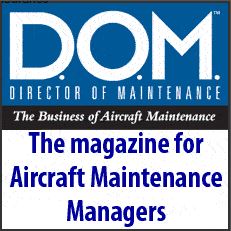
Quality Time
Editor’s note: The views and opinions expressed by contributing authors do not necessarily state or reflect those of ARSA and shall not be used for endorsement purposes.
Breaking Silence – More “Lessons on a Long-Fought-For Exemption”
Last month’s edition of the hotline shared “lessons on a long-fought-for exemption” courtesy of Advanced Composite Structures Florida (ACSF) and ARSA’s management firm Obadal, Filler, MacLeod & Klein, P.L.C. To help readers continue their education on the matter, ARSA caught up with ACSF Director of Business Development and Support David Stone to see how that exemption has been put to work:
(1) After receiving the exemption from the FAA to represent foreign military surplus composite main rotor blades as “suitable for installation,” describe the process by which ACS began performing work using the blades. From a regulatory compliance standpoint in particular, how did you perform the self-evaluation and revision to your capability list as described in §§ 145.209(d) and 145.215?
The addition of the blades to our capability list was actually very easy; we used our repair station quality manual procedures and form. Since the company already works on similar articles it was merely a matter of filling out the self-evaluation sheet, changing the capability list and informing the local office of the addition.
(2) Describe the experience of working with the local FSDO in implementing the exemption.
Since the local office was fully aware of the company’s efforts, there were few glitches on implementing the exemption. The office reviewed the inspection procedure and we added it to our repair station quality manual as an appendix. The FSDO had to issue a new page to our Operations Specifications indicating our ability to work under the exemption and we had to add some verbiage to the FAA Form 8130-3. These steps (and other directly required by the exemption) were accomplished with little fuss.
(3) Describe your communication with customers regarding the newly-recognized “suitability” of the CMRBs.
When we were going through the process of developing and having the exemption accepted, we were advised not to speak to anyone – including customers – regarding the project due to sensitivities within the agency and industry. This meant a two-year blackout period where we could not give anyone even the slightest bit of hope that help was on the way.
Now that the exemption is in place, we have done a lot of catching up with customers. Word of the exemption has spread very quickly via word of mouth as the UH1 world is very tightly knit and one press release with OFM&K seemed to go very far.
Reception of the blades as finally being suitable for installation on restricted category helicopters has been very positive. There are no more lingering doubts about the blades which, for years, were argued over between UH1 operators, FSDOs, PMIs and repair stations. Now it’s just a matter of UH1 operators assessing their needs, setting a budget and bringing the rotor blades into operation.
(4) Now that you’ve begun work, how do you assess the value of the long effort to get the exemption? What advice would you give another certificate holder facing the same opportunity?
The long effort has paid off in many ways other than the direct result of these blades listed by serial number on the exemption and being available to a new group of operators. Undertaking such a complex issue required learning in great detail many new subject areas. Obscure FAA regulations, blade design and engineering processes, military acquisition and disposition procedures, technical and production data applicability, repair and modification processes and interagency operations were just some of the subjects in which we had to become fluent in order to merely articulate what it was we needed to accomplish.
The vast amount of knowledge gained during this time has helped us to not only become the global authority on these composite rotor blades, but made ACS’ personnel much more capable in their individual capacities.
My advice to others seeking a similar opportunity is:
(1) Be certain that you are committed to seeing it to the end regardless of popular opinion and discouragement from regulators.
(2) Surround yourself with people, in every area of need (technical, legal, etc.) who are committed to the same goal and are actually capable of success.
(3) Keep your head down and talk to NO ONE about your project until it is finalized.
ITAR Compliance – Small Business Sanctions
By Thomas McVey, Esq., Williams Mullen
Note: The views and opinions expressed by contributing authors do not necessarily state or reflect those of ARSA and shall not be used for endorsement purposes. This article contains general, condensed summaries of actual legal matters, statutes and opinions for information purposes. It is not meant to be and should not be construed as legal advice.
Do you know what “ITAR” means? Is your company registered? Do you know if it should be? If you’re not sure, click here to take a look at Mr. McVey’s article from last month’s edition of the hotline to find out.
A recently-announced ITAR enforcement case involving a supplier of military spare parts sends a valuable message to small and mid-sized government contractors of every type.
The case involves Bright Lights USA, Inc., a small New Jersey manufacturer. According to the Directorate of Defense Trade Controls (DDTC) charging letter, the company’s business primarily consists of “manufacturing minor spare parts (including rubber stoppers, seals assemblies, and grommets) for both private- and public-sector customers.” Many of these parts transitioned off of the U.S. Munitions List (USML) beginning October 2013 as a result of Export Control Reform.
[To review the documents related to the Bright Lights Case and consent agreement, click here to visit the DDTC website.]
When supplying military parts, the Company periodically sought to obtain components from foreign suppliers. According to the DDTC, when ordering foreign-made parts the company sent drawings of export-controlled components to foreign suppliers to obtain quotations without obtaining the requisite export licenses. DDTC also claimed the company posted drawings of controlled items online to solicit quotations, including on a manufacturing sourcing website where the drawings could be accessed by foreign persons.
DDCT concluded that Bright Lights had “significant training and compliance program deficiencies” and charged the Company with a number of violations including:
(i) Exporting ITAR-controlled technical data to foreign suppliers without a license, including to China and India.
(ii) Exporting defense articles without a license to persons in the U.K., Spain, Portugal, Turkey and the UAE.
(iii) Violating the ITAR recordkeeping requirements for failure to maintain records of ITAR-related activities for a five- year period.
Bright Lights was assessed a $400,000 civil penalty but no criminal prosecution.
Firms performing work for government contracts frequently ask questions about the application of ITAR requirements, including how ITAR is applied to small and mid-sized companies. The Bright Lights case squarely addresses many of these questions. Here are the most important:
(Q1) Does the State Department expect small companies to comply with ITAR, and will it actually pursue enforcement cases against them?
Absolutely yes. Being a small or mid-sized company does not exempt a contractor from ITAR requirements. These obligations apply to companies large and small, and small contractors do not get a “free pass” due to their size. In fact some of the most sophisticated U.S. defense technologies are developed by small and mid-sized firms. This case clearly confirms that DDTC will initiate enforcement actions against small and mid-sized companies.
(Q2) Isn’t DDTC really interested in complex defense systems and end items and not incidental “spare parts”?
Absolutely no. DDTC is extremely interested not just in large “end items” but also in subsystems, parts, components, accessories and attachments for defense products. These comprise an important part of the defense supply chain and the government is extremely interested in compliance at all levels, including by prime contractors, subcontractors, second and third tier suppliers and service providers. As the Bright Lights case demonstrates, DDTC will definitely prosecute companies for ITAR violations involving spare parts.
(Q3) If a product is removed from the USML under Export Control Reform, doesn’t DDTC lose interest in the item?
Absolutely no. As set forth in the Bright Lights case, DDTC will pursue enforcement actions even for products that were removed from ITAR jurisdiction under Export Control Reform. DDTC is very interested in the integrity of the ITAR regulatory system – it will pursue enforcement actions even if particular items are decontrolled or transferred to another agency for regulation.
(Q4) Are the ITAR recordkeeping requirements really that important? Do these warrant diverting valuable compliance resources from other high priority uses?
The ITAR recordkeeping requirements are extremely important and exporters should treat these seriously. The recordkeeping requirements are an important law enforcement tool for DDTC in conducting export investigations. In addition, if DDTC discovers shoddy recordkeeping practices in an investigation, this may suggest that the company has lax compliance procedures and possibly other violations as well. It is imperative for contractors to follow these requirements carefully in their compliance practices. The Bright Light case clearly confirms that DDTC will prosecute companies for recordkeeping violations.
(Q5) Does DDTC lose interest in a violation if it occurred more than five years ago?
Not always. Export enforcement agencies may request companies subject to enforcement actions to waive applicable statutes of limitations and seek penalties for actions that occurred prior to the five-year limitation. In the current case Bright Lights executed multiple agreements with DDTC to toll the applicable statute of limitations during DDTC’s investigation.
(Q6) I can see how DDTC wishes to control the export of physical products – is it also interested in the transfer of ITAR-controlled technical data?
Absolutely yes. In fact, the export of technical data without a license is often considered as egregious as the export of physical products and possibly worse. If you illegally export one physical product, the bad guys get one product. If you illegally export the technical data related to a product, the bad guys can manufacture a thousand of them. The illegal export of controlled technical data (including disclosure to foreign persons in the U.S. and to your company’s own employees) is raised in many ITAR compliance cases and is considered among the most serious export violations.
The Bright Lights case sends an important message – export compliance is important for small and mid-sized companies performing work subject to ITAR. Some of the aerospace and defense industry’s most sensitive products and services are supplied by small and mid-sized companies, and the integrity of the supply chain is critical for even the smallest of replacement parts and components. The stakes are high in light of the potential civil and criminal penalties, including fines of up to $1 million and twenty years’ imprisonment. While the $400,000 civil penalty in the Bright Lights case is significant, it is small when compared to the possible criminal sanctions imposed in other ITAR cases.
Steps that small and mid-sized companies can take to come into compliance with ITAR include:
(i) Reviewing the jurisdiction and classification of their products and services to determine if they are controlled under ITAR and the Export Administration Regulations.
(ii) Based upon these classifications, determining the licensing and other requirements that apply. (iii) adopting ITAR compliance programs and conducting employee compliance training. Additional details regarding the ITAR requirements can be found at: ITAR For Government Contractors.
Companies performing work with ITAR implications have been forewarned – DDTC, along with its companion agencies the Bureau of Industry and Security, Office of Foreign Assets Control and Customs and Border Protection, do not factor a company’s “smallness” into account in administering compliance requirements.
Thomas McVey is the Chair of the International Practice Group at Williams Mullen in Washington DC where he advises clients on export control issues under ITAR, the Export Administration Regulations and the OFAC Sanctions Laws. Additional articles on ITAR, EAR and US sanctions programs are available at: www.williamsmullen.com/ITAR_Publications.
Training
ARSA, Barfield Team with Commerce Department for Civil Aviation Webinar
ARSA Executive Vice President Christian A. Klein and Bryan King of association member Barfield Precision Electronics will participate in a special Department of Commerce webinar on the World Trade Organization Agreement on Trade in Civil Aircraft on Jan. 18.
The webinar builds on the work ARSA has done over the past year to clarify the applicability of the treaty to aircraft parts imported into the United States for repair (see below). The session will cover:
- What aircraft and aircraft parts are covered the agreement.
- What countries signed it and what are their obligations.
- How U.S. aerospace exporters benefit.
- How U.S. importers, including repair stations, can bring aircraft parts into the United States duty-free under the agreement.
The webinar is part of the Commerce Department’s effort to improve understanding about the opportunities and obligations created by the treaty within the government and among customs brokers, freight handlers and aviation companies. Klein will discuss guidance ARSA created to help members navigate customs rules and take advantage of the agreement (order your copy below); King will discuss his company’s experiences with the agreement and best practices to ensure compliance.
The webinar will take place at 2:00 p.m. EST on Jan. 18. The cost to participate is $25. For more information or to register, go to:
https://emenuapps.ita.doc.gov/ePublic/event/editWebReg.do?SmartCode=8QB6
The guidance is available for free to ARSA members and may be ordered by visiting arsa.org/publications or completing the form below.
To see all of the association’s resources for establishing duty-free rates, visit arsa.org/regulatory/customs.
Access ARSA's Duty-Free Parts Importation Training On-Demand
Click here for session information
On Oct. 11, Executive Vice President Christian A. Klein hosted an hour-long session on parts importation requirements. Klein reviewed the issues surrounding duty-free import of civil aviation parts and articles and introduced the association’s resources for managing the process. Attendees will be given access to the ARSA Advisory 2017-01, “Importing Parts for Repair Duty Free Under 19 CFR § 10.183.”
More information on the issue can be found at: arsa.org/regulatory/customs.
Session Information:
Importing Aircraft Parts for Maintenance – Establishing Duty Free Rates
The session reviews the World Trade Organization’s exemption of civil aviation products and parts from import duties and describes the U.S. implementation of rules and guidance to support duty-free importation. It then walks through the association’s resources for ensuring that eligible imports are made free of Customs tariffs.
Click here to register and get access for 90 days.
Registration for an ARSA-provided training session includes:
- Unlimited access for 90 days to the recording made available after the live session is complete.
- A copy of the presentation and all reference material with links to relevant resources and citations.
- A certificate upon completion of the class, as well as any test material.
The association’s training program is provided through Obadal, Filler, MacLeod & Klein, PLC, the firm that manages ARSA. To go directly to OFMK’s online training portal, visit potomaclaw.inreachce.com. To learn more about the association’s training program and see course availability, visit arsa.org/training.
Get ARSA's Advisory on Importing Aircraft Parts (Members Only)
ARSA Maximizes Training Time in Singapore
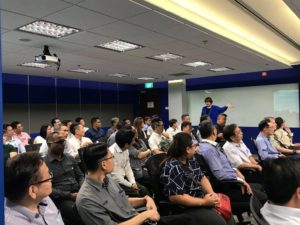
Sarah MacLeod speaks with SAQG workshop participants during a session in Singapore on Nov. 9. Photo courtesy SAQC.
On Nov. 9, Executive Director Sarah MacLeod conducted the Singapore Aerospace Quality Group’s (SAQG) fourth workshop, a gathering of more than 50 aviation professionals hosted in the small republic. The workshop’s participants were quality and engineering personnel representing 26 companies, most with strong international business interests.
MacLeod summarized the FAA’s efforts to overhaul its Flight Standards and Aircraft Certification organization; she also provided an overview of the agency’s designee and self-disclosure programs. The sessions closed with Sarah’s insight into the American rulemaking process, which focused participants on proactive engagement.
The SAQG is an initiative of the Association of Aerospace Industries – Singapore (AAIS) and was developed as a tool for AAIS to cultivate technically-focused professional communities. The group hosted MacLeod’s workshop to take advantage of her travel to Singapore to present regulatory training for FAA-certificated repair stations, which was administered through ARSA’s management firm Obadal, Filler, MacLeod & Klein, P.L.C.
Of the topics covered by MacLeod’s presentation, most are presented by sessions currently available on-demand from ARSA’s training program (bundle purchases available for various topics):
Self Disclosure – The Elements
This session reviews the elements of self-disclosure established by the FAA. It covers the who, what, why, when, where and how of filing a voluntary self-disclosure report with the agency. Additionally, it covers how the agency is to handle the report and its expectations for follow up actions.
Self Disclosure – How to Avoid Self-Exposure
This session reviews the best methods for investigating a potential non-compliance, including how to distinguish between business and regulatory requirements and how to use language that relates facts to the regulations without creating unnecessary consternation or scrutiny.
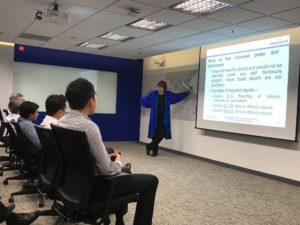
Sarah MacLeod speaks with SAQG workshop participants during a session in Singapore on Nov. 9. Photo courtesy SAQC.
The Rulemaking Process – Overview
This session provides an overview of how federal agencies make regulations that have the force and effect of law. Specifically, it reviews the agencies that must follow the Administrative Procedure Act, the procedures governed by the Act as well as other methods by which an agency can obtain recommendations from the public on its rulemaking activities and mandates.
The Rulemaking Process – Effective Comments
This session provides methods for submitting effective comments on FAA rulemaking proposals and on other documents that are posted for feedback from stakeholders.
Administrative Agencies & Their Powers
This session reviews why federal administrative agencies are created and how they use their powers to regulate activities within their jurisdiction. It also covers the basic procedures agencies must follow to create or revise regulations.
Administrative Agencies – The FAA & NTSB
This session reviews the creation and powers of the two agencies most prominent in civil aviation – the Federal Aviation Administration and the National Transportation Safety Board.
The session also included tailored content that can be provided through private sessions with OFM&K.
For more information about the association’s training resources, visit arsa.org/training.
To learn about MacLeod’s visit to Singapore, or for more information about the SAQG workshop, contact Vice President of Communications Brett Levanto (brett.levanto@arsa.org).
Part 145 – From Soup to Nuts
Take advantage of ARSA’s first intensive training: a four-hour exploration of 14 CFR part 145 by Executive Director Sarah MacLeod. Specially recorded with a hand-picked corps of live participants, MacLeod goes line-by-line through the repair station rule. The group’s open discussion explores the rule’s application and reviews the practical implications of obtaining and maintaining a repair station certificate.
For those in the maintenance community who demand a complete understanding of part 145, the most trustworthy source is the ARSA team that helped write it. Access the session now and receive unlimited viewing for 90 days. (Note: Pricing is based on per-hour member and non-member training rates).
Complying with Part 145 – “Soup to Nuts” (Four Hours)
Upon completion of this session, participants will have the tools to understand:
- The totality of the regulations governing the work of an entity holding a part 145 air agency certificate for a repair station from the FAA.
- How to research regulatory questions relating to work by a part 145 repair station.
- The difference between regulatory compliance and commercial obligations.
Registration for an ARSA-provided training session includes:
- Unlimited access for 90 days to the recording made available after the live session is complete.
- A copy of the presentation and all reference material with links to relevant resources and citations.
- A certificate upon completion of the class, as well as any test material.
Click here to register and get immediate access.
The association’s training program is provided through Obadal, Filler, MacLeod & Klein, P.L.C., the firm that manages ARSA. To go directly to OFM&K’s online training portal, visit PotomacLaw.inreachce.com. To learn more about the association’s training program and see course availability, visit arsa.org/training.
Complying with MAG 6
To see all of ARSA’s work on the MAG, visit arsa.org/mag.
For more than two years, ARSA has been leading an industry wide effort to “smooth” implementation of changes 5 (and now 6) to the U.S.-EU Maintenance Annex Guidance. Take advantage of that experience and learn to utilize the association’s Form E100 as a method of compliance with new parts documentation requirements.
Complying with MAG 6 – Completing ARSA Form E100
Description: This session provides an overview of the documentation requirements that United States repair stations with European Aviation Safety Agency part 145 approvals must follow when performing maintenance on EU-registered aircraft and components to be installed thereon—that is, when a “dual release” is issued for the work performed.
Instructors: Marshall S. Filler & Sarah MacLeod
Click here to register and get unlimited access for 90 days.
NOTE: Registration for this session is open to any interested participant. However, ARSA Form E100 is available only to association member organizations.
Registration for an ARSA-provided training session includes:
- Unlimited access for 90 days to the recording.
- A copy of the presentation and all reference material with links to relevant resources and citations.
- A certificate upon completion of the class, as well as any test material.
The association’s training program is provided through Obadal, Filler, MacLeod & Klein, P.L.C., the firm that manages ARSA. To go directly to OFM&K’s online training portal, visit PotomacLaw.inreachce.com. To learn more about the association’s training program and see course availability, visit arsa.org/training.
From Down Under – CASA’s Human Factors Resources
The term human factors refers to a wide range of issues that affect how people perform tasks in various environments. Whether a technician is performing line maintenance, a comprehensive avionics check, or at home preparing dinner for family, there are a variety of social and personal skills that complement the necessary technical acumen for appropriately completing their work.
By fully exploring and understanding the human capabilities and limitations involved in maintenance operations, your business can develop the best possible fit between your people and the technical systems in which they work.
CASA Resources
The Australian Civil Aviation Safety Authority’s (CASA) Human Factors for Engineers resource kit contains a series of guides, workbooks, and videos designed to provide a strong focus on human factors training within the aviation environment. This content includes:
- A variety of useful models (including PEAR—People, Environment, Actions, Resources) for managing human factors in maintenance
- A series of practical examples
- International regulatory requirements (including FAA documents),
- Strategies for mitigating problems
Praise from the FAA
The FAA’s chief technical and scientific adviser, Dr Bill Johnson, praised CASA’s human factors training resources. “I have never seen a more professional and comprehensive package,” Mr Johnson said. “It is the new international yardstick (or metric ruler) by which other human factors training programs will be measured.”
To access the resource kit: click here.
To access CASA’s full list of online offerings: click here.
Excerpt from CASA’s Human Factors Resource Guide for Engineers:
Using the ‘Rule of three’ in the field
One of the company’s Cessna 31Os has encountered a propeller control problem en route and has diverted to an intermediate field for a precautionary landing. The pilot reports that the aircraft has diverted and is now AOG. The company has dispatched you and the maintenance supervisor to sort out the problem. The passengers have been picked up and delivered to their destination in the spare aircraft. The chief pilot wants the aircraft repaired and returned to base as soon as possible the following day to pick up a charter the following evening.
The aircraft requires a prop change. It’s been a long day and you and the maintenance supervisor are approaching the end of your duty limits – a situation classified as ‘amber’ (use caution).The aircraft is parked in the open beside the aero club hangar. The weather has turned very blustery and a rain cell is approaching – again, amber. The sun is about to go down and although you have powerful hand-held torches (flashlights), the lack of lighting could cause difficulties with the prop change – amber.
Three ambers mean STOP. You now need to re-assess the situation. What options are there?
- When is the aircraft actually required back at base?
- Can you delay the task until the weather improves?
- Can the prop change wait until first light tomorrow?
- Is it possible to contact the on-site aero club to request the use of their hangar?
After you have reviewed the options, you have to decide how you will manage the risk. That answer depends on the context.
Your enquiries reveal that the spare aircraft can actually pick up tomorrow afternoon’s charter; and the president of the aero club has offered the aero club hangar for you to complete the prop change. Rather than just ‘getting on with it’, stopping, taking the time to find out more and review your options now substantially reduces the risk level associated with the task.
Regulatory Compliance Training
Test your knowledge of 14 CFR § 65.15 – Duration of certificates.
Click here to download the training sheet.
Membership
Terrell Siegfried Brings Life-Long Passion, Sense of Mission to ARSA Board
ARSA’s board of directors is an essential part of the association’s future. Directed by the bylaws to “supervise, control and direct the affairs of the Association…determine its policies…[and] actively prosecute its purposes,” the directors and officers of the board further ARSA’s work through insight, guidance and proactive support.
Terrell Siegfried, assistant general counsel at NORDAM and newest member of ARSA’s board, joined ARSA’s communications team for a brief introductory interview. Take a moment to get to know Siegfried as he learns his new role.
Tell us a little bit about yourself. What’s your professional background? How did you wind up in your current position?
From the time I was very young, I wanted to be a lawyer – in particular a business lawyer. So, I went to college at the University of Tulsa on a football scholarship and earned a business degree. I then began working at NORDAM for a few years to gain a basic business background before attending Notre Dame Law School. After law school, I went to work as a business lawyer for a number of years before returning to NORDAM to practice in its legal department. I am currently NORDAM’s assistant general counsel and corporate secretary.
NORDAM is well-known in many MRO circles, but for our readers who may not be familiar with it, tell us a little bit about the company.
NORDAM as we know it today, was founded in 1969 by my father, Ray Siegfried II. He was working for an insurance agency at the time and visited NORDAM to collect on a performance bond premium that had been issued to this small manufacturing company. My father learned that the company didn’t have enough money to pay the premium bond and shortly after filed bankruptcy. Although there was only a dozen or so employees, he felt the business had promise and was able to ultimately purchase it. He kept the name “NORDAM” because it sounded similar to his alma mater, Notre Dame.
My father led the company until his passing in 2005. Today, we have four siblings and a cousin working in leadership roles at the company, including my sister Meredith, who is CEO.
We are proud that we have remained family owned and privately held for nearly 50 years. We’re headquartered in Tulsa, Oklahoma and currently employ around 2,500 people worldwide, making us one of the largest independently-owned aerospace companies. In addition to being involved in the MRO business, we also design, certify and manufacture integrated propulsion systems, nacelles and thrust reversers for business jets; build composite aircraft structures, interior shells, custom cabinetry and radomes; and manufacture aircraft transparencies, such as cabin windows, wing-tip lens assemblies and flight deck windows.
Learn more about NORDAM at www.nordam.com.
What do you see as the major strategic challenges and opportunities facing NORDAM and the industry over the next five years?
It is a very interesting time for our industry and in particular third-party repair stations working in the nacelle, composite structures and flight control market. Over the past five years, many new dynamics have come into play including improved airline financial performance, changes in airline fleet mix and the importance of protecting intellectual property. These represent just a few of the areas which are influencing strategic decisions between airlines, manufacturers and maintenance organizations.
We expect to see the OEMs engage more in the aftermarket and also a shift to new generation aircraft entering the MRO market as they begin to age. The result is that new technologies surrounding the nacelle and composite structure maintenance and repair markets will become increasingly relevant – more so than over the past twenty years. Maintenance organizations must continue to evolve capabilities in both human resources and repair diversity, while building networks to provide solutions for customers on a global basis. Of course, achieving operational excellence in this market is key, but flying families safely must continue to be our priority.
What made joining ARSA’s Board attractive to you? What do you hope to accomplish as a Board member?
At NORDAM, we have a motto: “We fly families safely.” We want each of our stakeholders to always have safety at the forefront of their mind, and each part they repair or manufacture will be installed somewhere on an airplane that you, me, your family, my family, anyone’s family will fly on. We want all families to fly safely to their destination. To fly families safe requires, at a minimum, that MROs have the right regulations in place, with effective compliance and training programs.
ARSA’s mission hits right at the heart of those ingredients. ARSA offers strong regulatory and legislative advocacy to better ensure the right regulations are in place, they offer compliance assistance and training opportunities, as well as workforce development, all of which are geared to assuring families fly safely to their destination.
Joining the ARSA Board, through its impact and outreach at a federal level, facilitates the opportunity to positively impact the MRO industry and to continue the positive trajectory of flight safety. I will also continue to raise awareness for the legislative needs that support programs to develop skilled technical workers. Gone are the days where you had the option of buying an insurance policy at your departure gate; and that is due to a strong and healthy MRO industry.
From your perspective, how can ARSA address some of the opportunities and challenges you’ve just identified?
The presence of ARSA in our industry is more relevant now than ever before. As the cost of spare parts increases, and with the reduced availability of technical data, the airlines have fewer and fewer options available to them in the market to access affordable repairs. Maintenance organizations must continue to evolve through onboarding new personnel, growing capabilities and building their networks.
ARSA can continue its contribution to MRO’s success by giving a voice and representation of the industry to the policy makers. It can provide the top-notch regulatory and policy training, and facilitating growth of the maintenance organization’s network with precise and experienced counsel. ARSA should continue its efforts to help repair stations navigate not only the FAA requirements, the accessibility of foreign repair stations, and also the ever-changing global compliance and certification landscape.
On a more personal note, what do you love about your job?
It sounds very cliché, but I honestly really enjoy the people I have the privilege of working with at NORDAM. As a lawyer for the company, I get to work with people at all levels of the organization. It provides me with a variety of work and a variety of individuals to work with. Each day is challenging and each day is different. However, it is gratifying when you have the chance to use your skillset to find a solution that betters the company, and consequently, the 2,500 or so stakeholders who make up NORDAM.
What do you do for fun outside the office?
Aside from spending time with my wife and children, I enjoy hunting and fishing. I also love watching my alma maters, Tulsa and Notre Dame, in sports, although, depending on the year, it can also be heartbreaking!
ARSA thanks Terrell Siegfried for his time and contribution to this edition of the hotline. The views expressed in this interview do not state or reflect those of ARSA and shall not be used for endorsement purposes.
Welcome & Welcome Back – New & Renewing Members
ARSA’s members give the association life – its work on behalf of the maintenance community depends on the commitment of these organizations. Here’s to the companies that joined or renewed in November:
New Members
AE and C Services, LLC
AerSale, Inc.-Goodyear*
Britt Metal Processing, Inc.
Matinaire Aviation, LLC
MRO Holdings
Trace Aviation
*Previous membership lapsed in 2011, so this member is “new” all over again.
Renewing Members (Member Since)
Aircraft Inspection Services, Inc. (2013)
Airway Aerospace, Inc. (2016)
Aviation Fabricators (2015)
Aviation Repair Solutions, Inc. (2006)
Avocet Aviation Services, LLC (2014)
Fox Equipment Services, Inc. (2016)
HarcoSemco (1998)
Intrepid Aerospace, Inc. (2016)
Midway Aerospace (2004)
Millennium International (2013)
Palm Beach Aircraft Propeller, Inc. (2001)
Rotron, Inc., dba Ametek Rotron (2016)
Soniq Aerospace, LP (2016)
The Barden Corporation (Schaeffler Aerospace) (2012)
Quick Question – Drone Maintenance
Repair stations must plan carefully in order to perform work on existing aircraft fleets while meeting needs presented to the market by new equipment. Over the past few years, enhancing technical competencies and commercial demand have introduced unmanned aircraft systems into the world’s airspace.
International regulatory regimes are trying to catch up with quickly-advancing “drone” technology, and ARSA’s members can help the association grasp how these aircraft are making their way into maintenance facilities. This month’s “quick question” provides a first look at the issue:
For more information about this or any other question, contact Brett Levanto (brett.levanto@arsa.org).
Click here to see what questions have been asked and answered…and keep a lookout for more.
A Member Asked…
Q: We recently had an onsite audit from a charter operator so it could add us to its approved vendor list. While we passed that onsite review, we are now being told that our mechanics have to go through the charter’s training program in to order to be added to its list.
We only perform work on component parts, we are not using the charter’s paperwork and we are not releasing its aircraft for return to service. Is it really required that we go through their training program?
A: Thanks for asking! Unfortunately, the answer is “it depends” on two considerations:
(1) IF the operator’s has a “maintenance program” under part 121 or 135 AND that program has requirements under part 121, subpart L (see in particular § 121.368) or part 135, subpart J (see in particular § 135.426) AND those “requirements” include training, then the answer is “yes” – as a contract maintenance provider you have to follow the air carrier “requirements” (see § 145.205).
(2) IF the CONTRACT requires or will require the training as a term, then again, “yes.” you would have to get your people trained or not sign or fulfill the contract.
So, maybe the answer is “yes,” but you need to know “why”!
Have a question for ARSA? Click here to let us hear it.
Make ARSA’s Voice Your Own: Advertise
ARSA has a menu of advertising opportunities for arsa.org, the hotline and the ARSA Dispatch.
Take advantage of these great opportunities today to showcase your company, a new product or event. For more information go to arsa.org/advertise.
Stand Up for ARSA by Sponsoring in 2018
In order to provide world-class resources for its members, the association depends on the commitment of the aviation community. By sponsoring events and activities, supporters can help ARSA’s work on behalf of repair stations to endure.
Need a place to start? For information about opportunities, including sponsorship of the 2018 Annual Repair Symposium (click here for info), contact Vice President of Communications Brett Levanto (brett.levanto@arsa.org).
Resources
ARSA strives to provide resources to educate the general public about the work of the association’s member organizations; should you need to provide a quick reference or introductory overview to the global MRO industry, please utilize AVMRO.ARSA.org.
AVMRO Industry Roundup
ARSA monitors media coverage on aviation maintenance to spread the word about the valuable role repair stations play globally by providing jobs and economic opportunities and in civic engagement. These are some of this month’s top stories highlighting the industry’s contributions.
You can explore these stories through ARSA’s Dispatch news portal.
Industry Calendar
Aerospace & Defence MRO South Asia Summit – New Delhi – Jan. 18-19
Airline Engineering & Maintenance: Middle East – Dubai – Jan. 22
MRO Middle East – Dubai – Jan. 23-24
Aero-Engines Americas – Fort Lauderdale, Florida– Jan. 31-Feb. 1
MRO Latin America – Panama City, Panama – Feb. 14-15
HAI HELI-EXPO – Las Vegas – Feb. 27-March 1
MRO East Asia – Hanoi, Vietnam – March 7-8
ARSA Legislative Day & Annual Repair Symposium – Arlington, Virginia – March 15-17
ATEC Annual Conference – Arlington, Virginia – March 15-17
MRO Americas – Orlando, Florida – April 10-12
Previous Editions
2017: | Jan | Feb | Mar | Apr | May | June | July | Aug | Sept | Oct | Nov | |
2016: | Jan | Feb | Mar | Apr | May | June | July | Aug | Sept | Oct | Nov | Dec |
2015: | Jan | Feb | Mar | Apr | May | June | July | Aug | Sept | Oct | Nov | Dec |
2014: | Jan | Feb | Mar | Apr | May | June | July | Aug | Sept | Oct | Nov | Dec |
2013: | Jan | Feb | Mar | Apr | May | June | July | Aug | Sept | Oct | Nov | Dec |
2012: | June | July | Aug | Sept | Oct | Nov | Dec |
the hotline is the monthly publication of the Aeronautical Repair Station Association (ARSA), the not-for-profit international trade association for certificated repair stations. It is for the exclusive use of ARSA members and federal employees on the ARSA mailing list. For a membership application, please call 703.739.9543 or visit http://arsa.org/membership/join/. This material is provided for educational and informational purposes only. It does not constitute legal, consulting, tax or any other type of professional advice. Law, regulations, guidance and government policies change frequently. While ARSA updates this material, we do not guarantee its accuracy. In addition, the application of this material to a particular situation is always dependent on the facts and circumstances involved. The use of this material is therefore at your own risk. All content in the hotline, except where indicated otherwise, is the property of ARSA. This content may not be reproduced, distributed or displayed, nor may derivatives or presentations be created from it in whole or in part, in any manner without the prior written consent of ARSA. ARSA grants its members a non-exclusive license to reproduce the content of the hotline. Employees of member organizations are the only parties authorized to receive a duplicate of the hotline. ARSA reserves all remaining rights and will use any means necessary to protect its intellectual property.
© 2017 Aeronautical Repair Station Association